8 orion 3a manifold, valve adjustment procedure, Orion 3a manifold, valve adjustment procedure, Section 4.2.8 – Condec PIN8010 User Manual
Page 17
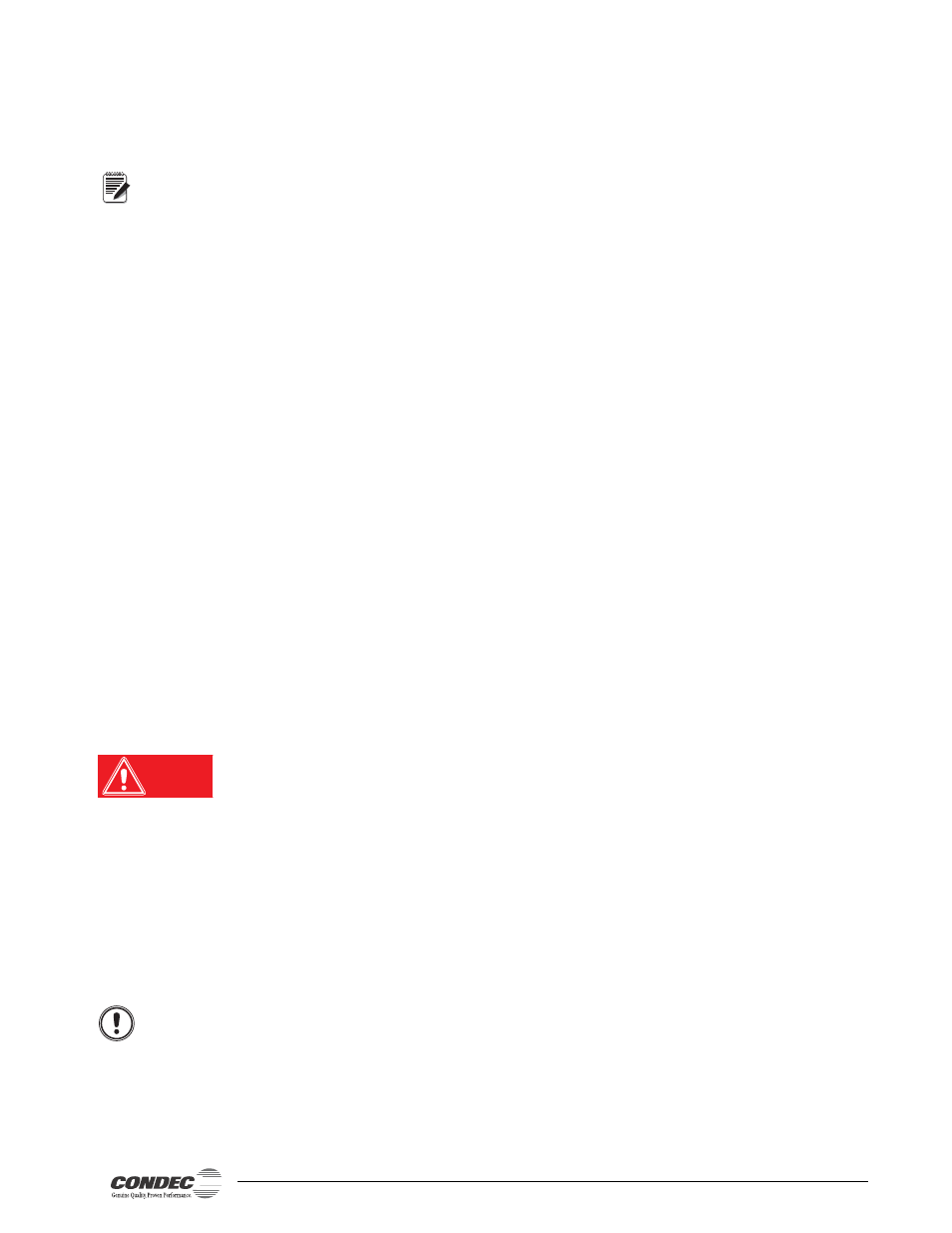
Maintenance & Service
11
4.2.8
Orion 3A Manifold, Valve Adjustment Procedure
Tools required:
hex wrench (.050")
hex wrench (.061")
Note
See Table 4-2 on page 22 and Figure 4.3 on page 22 for additional parts information.
(* denotes reference to Figure 2-1 on page 5.)
1. Locate the male end of the supplied output port fitting (PN 55542) found within the top cover. Connect
with the output port (*9).
2. Connect the other end of the output port fitting, male 7/16-20 37 degree (AN-4) JIC thread, to Condec
3030, Condec DPDG, or the customer-supplied pressure electronic calibration standard. If necessary, use
adapters or a hose. Use a cheat seal pad (PN 54854) between the output port fitting (PN 55542) and the
hose/adapter. Properly tighten all connections.
3. If using the optional external cylinder PN 59533, connect the male end of the input hose (*3) to the
female CGA-580 brass cylinder (*5) valve fitting.
If not using the optional external cylinder, connect the male end of the input hose (*3) to the female
CGA-580, customer-supplied, regulated pressure source.
4. Connect the swivel fitting end (7/16-20) of the input hose (*3) to the input port (*4) fitting using a cheat
seal pad (PN 54854) between the mating surfaces. Properly tighten all connections.
5. If not already done, remove the Orion 3A pressure and vent valve knobs (3) using the .061" hex wrench.
6. Energize the electronic calibration standard attached to one of the output ports (9) and let it warm up.
7. To adjust the pressure (coarse) valve, use a .050" hex wrench to loosen the set screw (34) on the locknut
(2) and turn the locknut clockwise to its stop.
8. Check to see that the knob insert (4) is securely fastened to the valve shaft (11). If it is loose, re-tighten
the set screws (23) with the .061" hex wrench.
9. Close the pressure (coarse) valve by turning the knob insert (4) clockwise until you feel the valve needle
seat on the O-ring (valve is now in closed position).
10. Rotate gears on both isolation valves (two inner valves), counter-clockwise until they stop, then rotate
clockwise 1/2 turn (opening isolation valves).
11. With a pressure source connected to the input port (*4). Use the Condec REG 1000 (*10), to increase the
regulated pressure (monitor the regulated pressure gauge [*7]) to 1,000 PSIG. Enable the power switch
(*2) and monitor the pressure as it builds in the accumulator gauge (*7). Turn the power switch (*2) off
when 8,000-10,000 PSIG has been achieved.
Do not operate the unit in continuous mode without an operator being present.
DANGER
12. Open the vent valve (*12) to atmosphere, then close the vent valve (*12).
13. Slowly open the pressure (coarse) valve by turning the knob insert (4) counter-clockwise until the
displayed pressure increases. Then turn the knob insert slightly clockwise until the pressure stops rising.
14. Mark a radial line at the 12 o'clock position on the knob insert.
15. Turn the knob insert (4) clockwise to move the mark to the 6 o'clock position.
16. Turn the locknut (2) counter-clockwise until it contacts the bottom of the stop washer. Tighten the set
screw (34) on the locknut with the .050" hex wrench.
17. Install the pressure (coarse) valve knob (3) on the knob insert (4) and engage its gear (5) with the smaller
isolation valve gear (6). Turn the knob clockwise until the isolation valve is slightly snug.
Important
Do not use excessive torque when tightening pressure (coarse) valve knob. Doing so may damage the seat.
18. Remove the pressure (coarse) valve knob. Align the set screws (25) with indentations on the knob insert
(4). Install the knob on the knob insert while engaging the knob gear (5) with the isolation valve gear (6).
19. Tighten the set screws (25) with the .061" hex wrench. The pressure (coarse) valve is now adjusted.
20. To adjust the vent valve, follow steps 7-8 replacing the term pressure (coarse) valve with vent valve.