Tech n ical p ape r – PCT Engineered Comparison of UV and EB Technology for Printing and Packaging Applications User Manual
Page 8
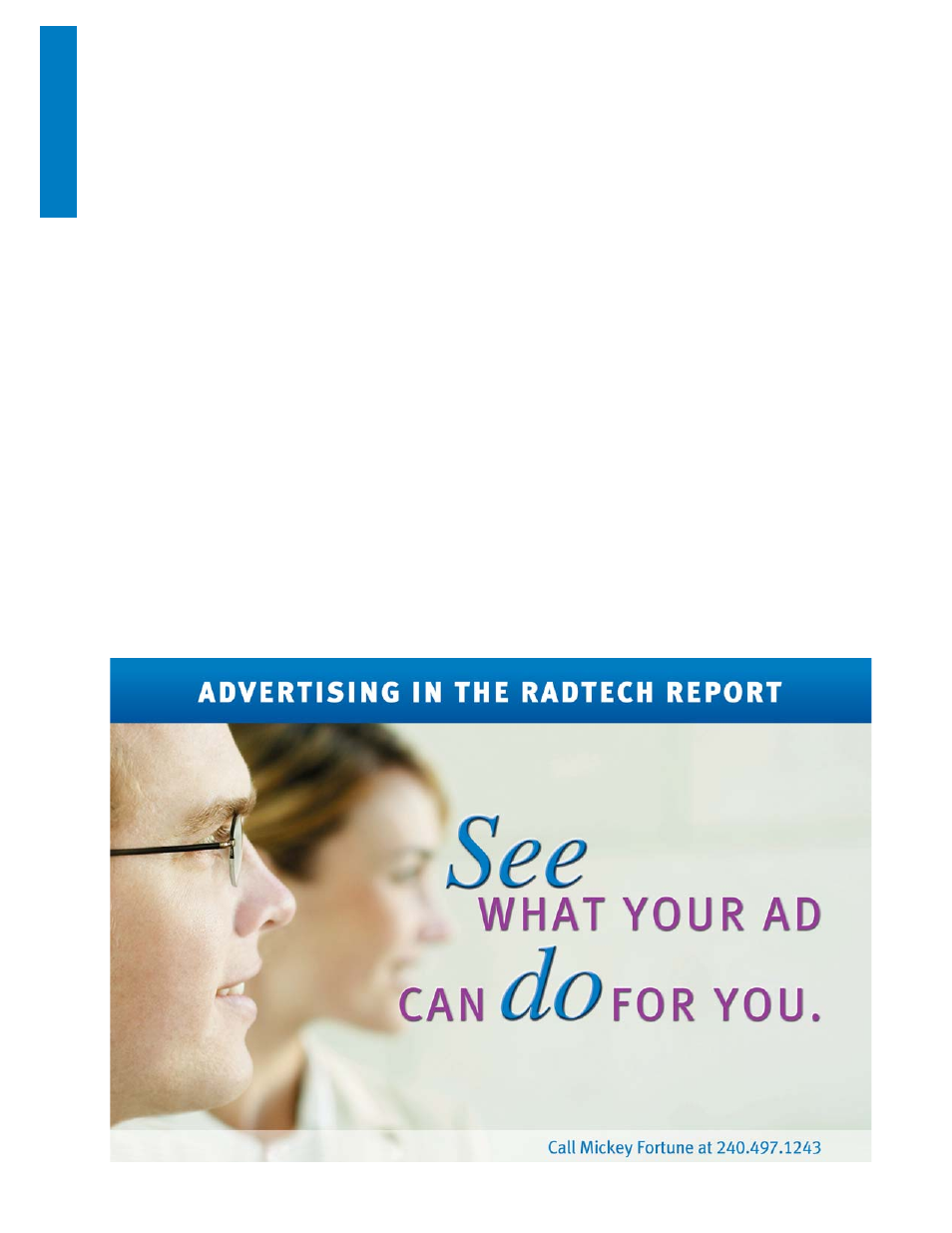
34 RADTECH REPORT SEPTEMBER/OCTOBER 2008
Tech
n
ical P
ape
r
Since EB does not require an
initiator, it is often considered to be
more “food friendly.” EB-induced
breakdown of components of inks,
coatings, adhesives and substrates may
be a source of other taint, odor and
migration issues that merit
investigation for a given application.
In many packaging constructions,
the functional barrier is obvious and
there is no reasonable expectation of
adulterating the food. Examples
include labels on rigid containers and
folding cartons that have an additional
inner layer of packaging around the
food. There are many constructions in
which the barrier is less obvious. This
may include cases in which a relatively
thin polyolefin film is the only layer
between the UV/EB material and the
food. It may also include applications
in which the UV/EB printed/coated
surface is in contact with the food
contact surface during roll-to-roll or
cut-and-stack processing of the
packaging allowing off-setting to occur
prior to filling. Migration testing or
calculations can often be used to
establish food law compliance in
these cases.
18
The recent successful
Food Contact Notification (FCN) can
also help assure food law compliance
and provide additional assurances for
end-users.
19
Consistency/Maintenance
Process consistency and
maintenance required to assure
product quality may also merit
consideration when comparing UV and
EB technology. The output of UV
lamps will decrease as the lamps age.
This decrease may not be uniform
across the spectral output with short
wavelengths output degrading before
longer wavelengths. This can affect the
surface versus throughcure
characteristics of the process. The
aging may also not be uniform across
the width of the lamp causing
inconsistent curing at the edges of the
sheet or web relative to the center. The
process itself may be able to tolerate
this variability in lamp output. The
most common way to minimize the
variability is by preventive
maintenance which consists primarily
of bulb replacement and reflector
cleaning or replacement. The typical
lamp maintenance interval is about
1,000 to 3,000 hours. The cleanliness
of the process can have a major effect
on the need for maintenance. Ink mist,
paper dust and other sources of
contamination will shorten the useful
life of the lamp. Lamp temperature
control is also critical for maximum life.
EB output tends to be very consistent
with time. No significant change is
expected with age. Variability in cross-
web uniformity is typically less than
10%. Essentially, all EB systems are