Figure 3, Tech n ical p ape r, Uv lamp system components – PCT Engineered Comparison of UV and EB Technology for Printing and Packaging Applications User Manual
Page 4
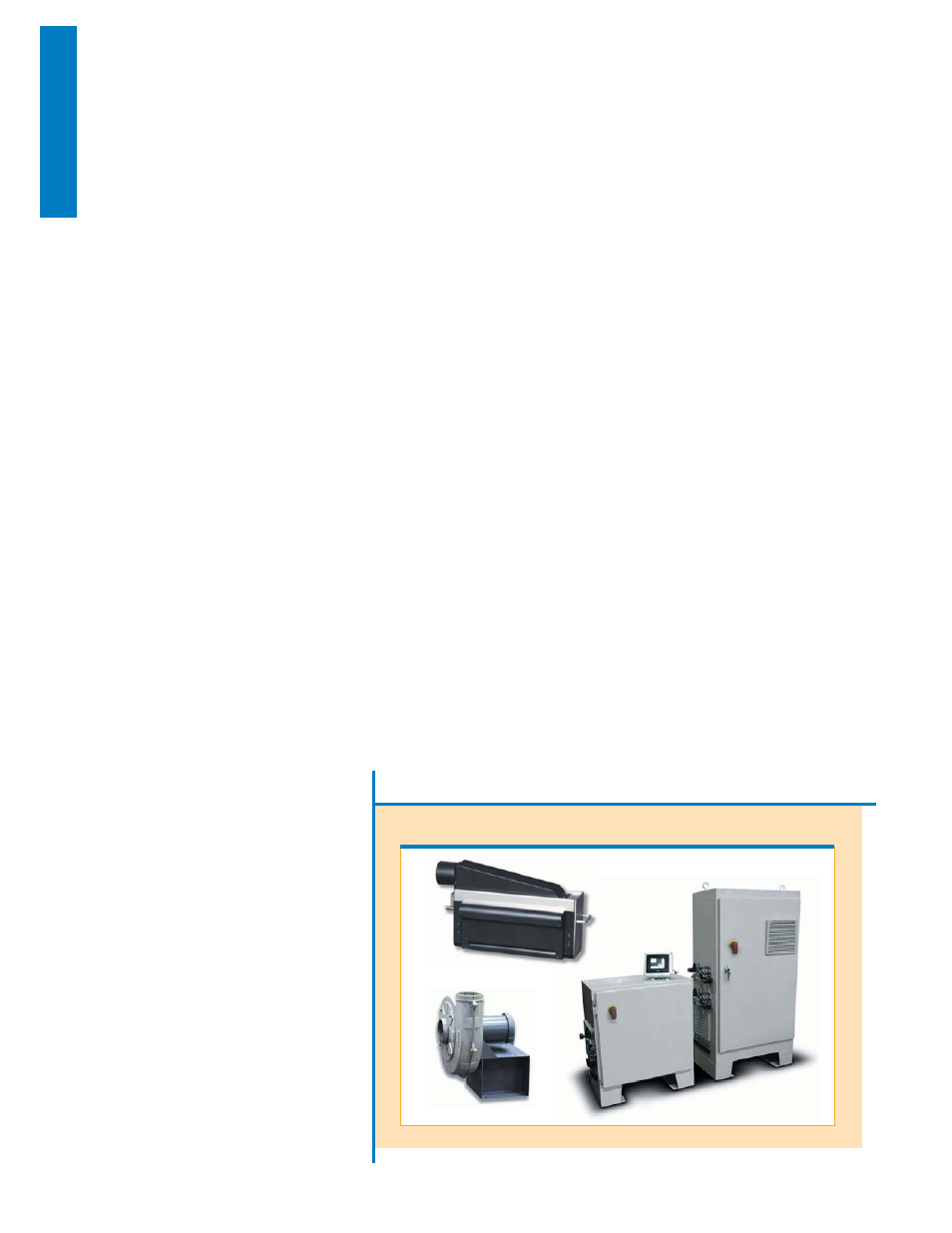
30 RADTECH REPORT SEPTEMBER/OCTOBER 2008
Tech
n
ical P
ape
r
for printing and packaging applications
is completely shielded and interlocked
to contain the damaging UV energy. In
most cases, no special personal
protective equipment (PPE) is
required other than the PPE normally
recommended in the printing and
packing production plant environment.
In addition to UV energy hazards,
mercury lamps also operate at very high
temperatures. Hazards from thermal
skin burns are minimized by the lamp
housing which surrounds the bulb.
Electrons from EB equipment
present limited hazards because of
their limited ability to penetrate. The
main hazard of EB is the secondary
X-rays that are generated when
electrons interact with matter,
including metal components within the
EB reaction chamber. Modern EB
equipment is completely self-shielded.
The shielding is interlocked and
monitors are present which will shut
down the EB unit if X-rays are
detected. Radiation is not present if
the machine is not energized. Most EB
installations will include a person
trained as a Radiation Safety Officer
(RSO). Periodic radiation surveys are
typically conducted to supplement the
continuous monitoring of the equipment.
Worker exposures above normal
environmental background levels are
extremely rare.
Both UV and EB equipment are
very safe to operate and there are no
significant drivers for selection of
one technology over the other based
on safety.
Equipment Size
The components of typical UV
curing systems include the lamp,
power supply, air handling equipment
(blowers) and control panels. These
components are pictured in Figure 3.
The lamp (which includes the bulb,
reflectors, shielding and heat
management components) is relatively
compact and lends itself well to
interstation installation between
printing decks (Figure 4). Interstation
installation allows curing of each ink
color. Multiple colors are combined in a
“dry trapping” process to create the
graphic image. Interstation curing also
allows press designs in which the
printed side of the web may be turned
up against an idler roll between stations.
Original industrial EB equipment
was quite large (Figure 5). Modern
low-voltage EB equipment can be less
than one-half the size of original
industrial EB equipment. In spite of
the size reduction, it is still not
practical to use this equipment for
interstation curing; though the smaller
footprint is still very attractive for
end-of-press installations.
9
The most
common installation of this type of
equipment is at the end of a web offset
press used for the production of
folding cartons (Figure 6). Offset
(lithographic) printing uses paste inks
which are designed to be “wet trapped”
without any interstation drying. This
lends itself well to EB curing at the end
of the press with a single EB unit. The
development of modern low-voltage
EB equipment coincides nicely with
the development of web offset presses
incorporating variable repeat length
technology. This has facilitated
expansion of web-offset printing
technology beyond folding cartons to
flexible packaging and labels.
10
Flexographic printing utilizes liquid
inks so, historically, it has been necessary
to use interstation curing to dry trap
inks. This interstation curing has been
achieved by thermal or UV curing
technology. Recently new technology
(Wetflex™) has been developed to wet
trap flexographic inks.
11
Wet trapping
allows interstation curing to be
eliminated and replaced with a single EB
curing station at the end of the press
(Figure 7). This technology has also
been shown to give extremely low dot
gain which results in superior quality
printing. It should be noted that Wetflex
is limited to central impression (CI) flexo
press configurations in which the printed
side of the web does not contact idler
rolls until after EB curing. Flexographic
CI printing is often the preferred
Figure 3
UV Lamp system components
Photos courtesy of Mark Andy Inc.
Power Cabinet
UV Lamp Cassette
Blower