Figure 6, Figure 7, Tech n ical p ape r – PCT Engineered Comparison of UV and EB Technology for Printing and Packaging Applications User Manual
Page 6
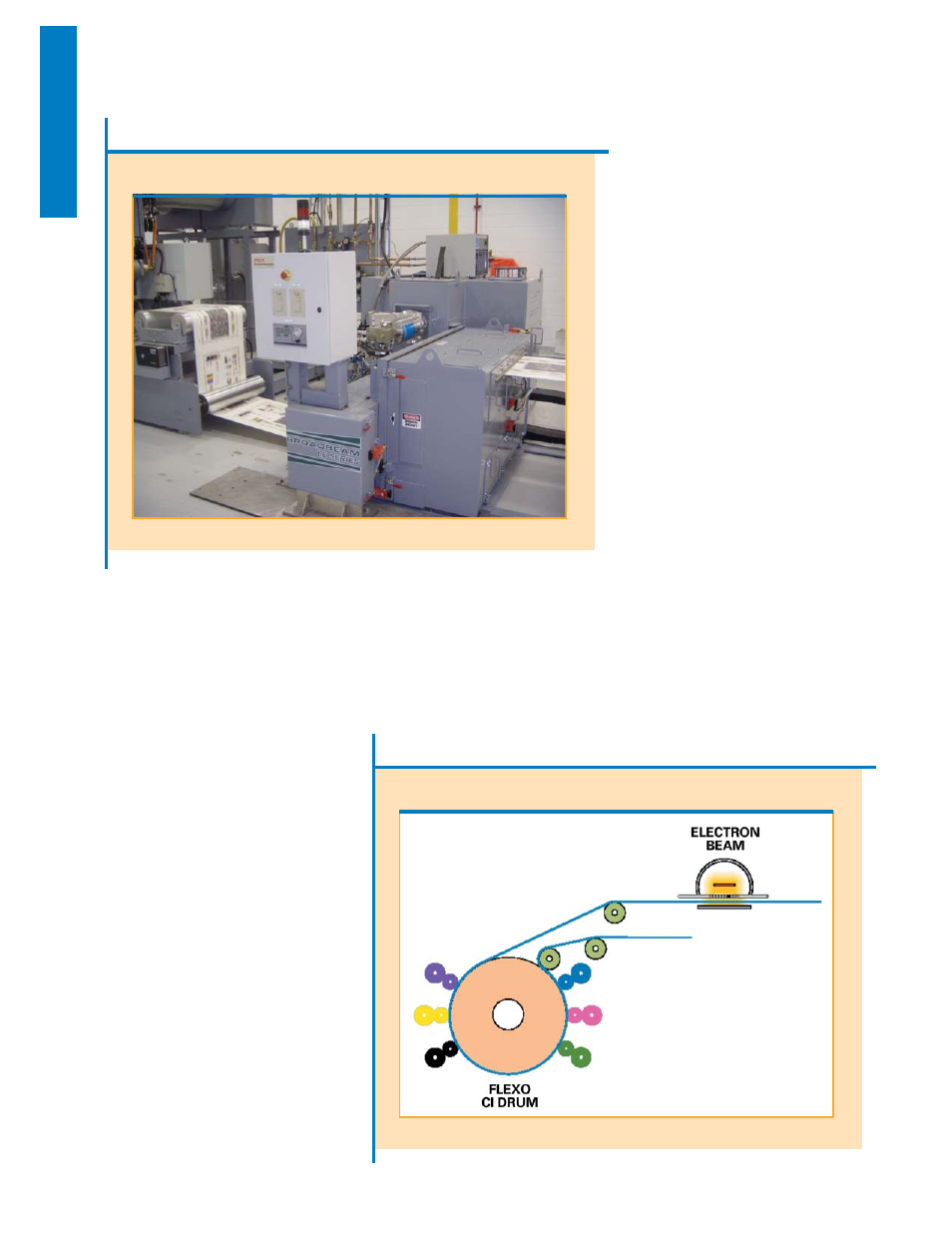
32 RADTECH REPORT SEPTEMBER/OCTOBER 2008
Tech
n
ical P
ape
r
adhesives for printing and packaging
applications. This may be due in part
to a declining cost of photoinitiators
following the expiration of some key
patents. Comparison of UV and EB
operating costs is, therefore, more
related to the equipment itself.
With mercury-based UV lamps,
about one-half of the electrical energy
input is converted to UV energy. The
remaining energy is lost as heat. Some
additional electrical energy is consumed
in the operation of blowers for air
cooling which is most common for
printing and packaging applications.
EB equipment is more efficient at
converting electrical energy into curing
energy compared to UV equipment.
Some additional electrical energy is
needed for vacuum pumps and water
cooling of the emitter. Another
operating cost of EB is nitrogen, which
is needed to inert the curing zone for
most ink and coating applications.
A detailed comparison of operating
costs for UV and EB can be made for a
specific application. Often, this analysis
will show similar costs for UV and EB
and significant savings compared to
thermal curing.
Inerting
Free radical curing—commonly
used in both UV and EB applications—
is inhibited by atmospheric oxygen.
Oxygen itself exists in a biradical
(triplet) state and will rapidly diffuse
into the surface of an ink or coating
and terminate the polymerization
(curing) reaction.
UV formulations can be designed to
cure in an air atmosphere. In air curing
systems, the radical initiation
essentially outcompetes the oxygen
termination. This is possible because of
the high surface irradiance illustrated
in Figure 1. The ability to UV cure in
air can be advantageous for some
printing and packaging applications. In
particular, air curing is very important
in sheet-fed printing. Sheet-fed
equipment is very difficult to inert
because of the mechanisms present to
transport the sheet through the press.
In some cases, it may be advantageous
to inert UV-cured systems. Inerting can
greatly accelerate UV curing which can
increase line speed, reduce the number
of lamps, and/or reduce the amount of
photoinitiator needed for curing.
Inerting may be an attractive option for
food packing applications in which
Figure 6
Low-voltage EB equipment on web offset press
Figure 7
WetFlex™ EB flexographic printing