Figure 2, Tech n ical p ape r, Depth/dose profiles for low-voltage eb – PCT Engineered Comparison of UV and EB Technology for Printing and Packaging Applications User Manual
Page 3
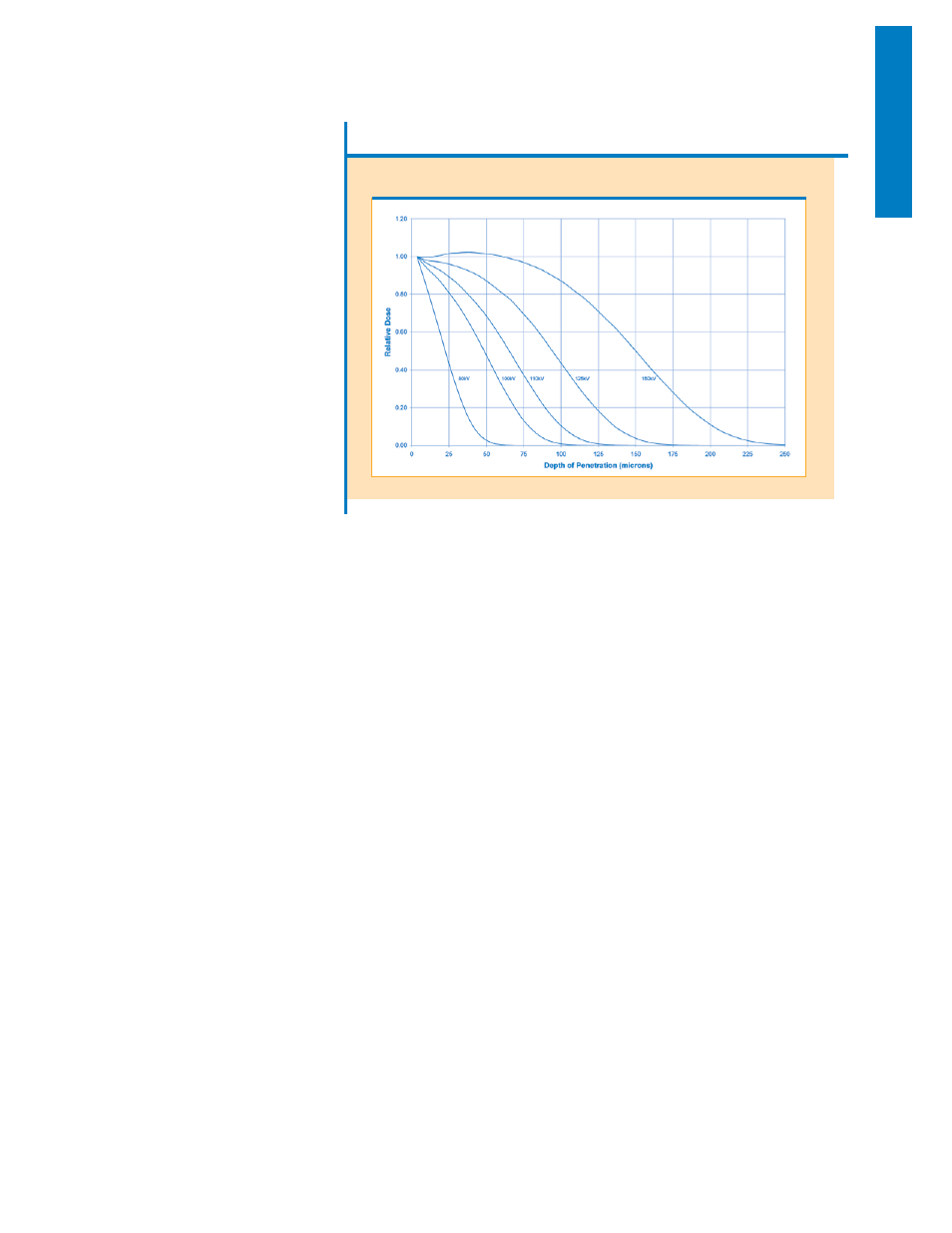
SEPTEMBER/OCTOBER 2008 RADTECH REPORT 29
Tech
n
ical P
ape
r
material. Clear materials are “optically
thin.” In general, UV energy can easily
penetrate clear materials such as
overprint coatings and clear films.
Even if a portion of the UV spectrum is
blocked by a clear layer (such as a PET
film), effective curing can usually be
achieved throughout the thickness of
the layer by selecting the proper
photoinitiator package. Penetration of
UV energy becomes a significant
challenge when curing “optically thick”
pigmented materials. Many pigmented
printing inks can be UV cured as long
as the pigment loading and/or ink
thicknesses remain relatively low. It is
typically difficult to UV cure through
printed, white opaque, heavy black or
metallic inks.
3
Penetration of UV energy can be
controlled, to a degree, by the peak
irradiance of the lamp. The peak
irradiance depends on the power and
the focus of the lamp system. High-
power, tightly focused lamps can
improve curing of some higher OD ink
layers
4
; however, the OD can reach a
point in which curing is not possible
with any commercial lamp system.
EB penetration depends upon the
mass density and thickness of the
material. Electrons penetrate more
deeply through lower density materials
(such as polyolefin films and paper)
compared to high-density materials
such as metal foils. Mass density and
thickness taken together may be
expressed as the basis weight of the
material. For most printing and
packaging applications, the basis
weight is expressed in units of grams/
meter
2
or pounds/3000 ft
2
. Electrons
are “color blind” and penetration is not
affected by pigments and opaque
substrates. EB is ideal for curing high-
opacity white, black and metallic ink
layers. EB can also penetrate reverse
printed, metalized and white films as
well as papers to instantly cure adhesive
layers for laminating applications.
5
EB penetration is controlled by the
accelerating potential (voltage) of the
EB equipment. Figure 2 shows EB
penetration as a function of voltage.
Low-voltage EB equipment operating
from about 70 to 125 kV is ideal for
curing thin inks, coatings and film
layers used in most printing and
packaging applications.
6
UV and EB Equipment
The most common UV equipment
for printing and packaging applications
is based on medium-pressure mercury
lamps. These lamps may be energized
through electrodes (arc type) or by
microwaves (electrodeless). Medium-
pressure mercury lamps produce a
characteristic UV-emission spectrum
with multiple peaks between 250 nm to
450 nm. Mercury lamps may also be
doped with various elements to shift the
spectral output to better match the inks,
coating or adhesive that is being cured.
Other types of lamps, such as
xenon lamps, are available but are not
commonly used for printing and
packaging applications. UV-light emitting
diodes (LEDs) are now available with
higher powers, but their use is still
quite limited in printing and packaging
materials.
7
EB equipment is based on electrically
operated filaments and grids contained
within a vacuum chamber. The
electrons are accelerated through a
window/foil structure to reach the
substrate at atmospheric pressure.
EB equipment includes “curtain” and
scanning type units. The curtain type
is used almost exclusively for printing
and packaging applications. Most EB
equipment includes an active pumping
system to maintain a vacuum in the
electron gun chamber. A new
generation of modular 10- and 16-inch
wide EB equipment based on
permanent vacuum emitters is also
now available. There have been some
initial investigations incorporating
these modular emitters in printing
applications.
8
UV and EB Equipment Safety
UV lamps used in printing and
packaging applications produce
significant short wavelength UV
output. This intense UV energy can
cause skin and eye damage.
Commercial UV lamp equipment used
Figure 2
Depth/dose profiles for low-voltage EB