PCT Engineered Air Quench System for Steel Rails User Manual
Air quench system for steel rails, System features
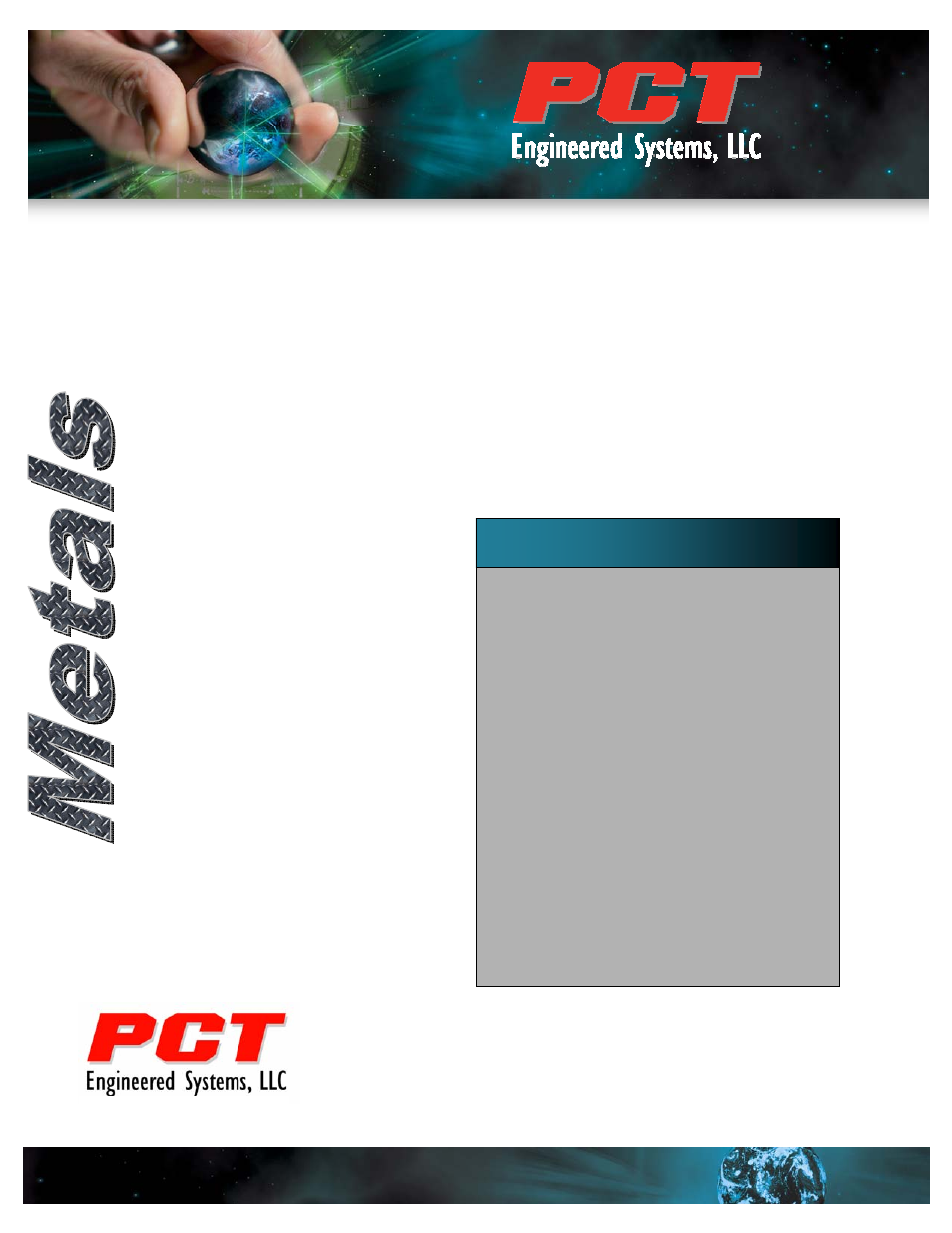
© 2006 PCT Engineered Systems LLC. All Rights Reserved
8700 Hillandale Road.
Davenport, IA 52806
563.285.7411
FAX 563.285.7433
www.teampct.com
The Solutions Team
Air Quench System for Steel Rails
The Application
An international steel equipment manufacturer was selected to supply a railroad rail air quench
system to a U.S. steel plant. The plant produces premium rail used to handle the lateral forces on
curved sections of railroad track. The OEM contracted the electrical control system to Allen-Bradley
Drive Systems.
Allen-Bradley Drive Systems asked PCT Engineered Systems to partner with them to provide the
MMI and PLC programming needed to supplement their efforts. PCT was the integrator of choice
because of our material handling experience, plant floor database programming abilities and drive
control expertise.
The PCT Solution
PCT designed, developed, installed and
commissioned a feature-rich SCADA
application using USDATA’s Factory Link
package to control the air quenching system.
The package was developed in an OS/2
platform. The system included three SCADA
nodes communicating over a LAN and the
three Allen-Bradley PLC’s that controlled the
drives and sequencing of the in-line quench
systems.
PCT’s combination of plant floor process
knowledge, extensive software programming
and drive control experience made integration
of process data acquisition and tracking a
reality for the manufacturer.
According to the manufacturer’s project
manager, “We would like to thank PCT for the
seamless support and assistance you have
given to us to carry out this project.”
This unique air quench system is one of only
two of its kind worldwide.
System Features
• Production scheduling and in-process tracking
of the rails through the quench process.
• Multiple databases that handle scheduling for
every rail entering the quench systems.
• Data logging operations that are easily
retrieved after being entered as historical data.
• Mathematical modeling and optimization for
controlling and regulating the amount of air
pressure and volume of air applied in the
quench; as well as temperature control and
other parameter controls, all based on the
recipe in use.
• More than 20 different quenching recipes,
allowing the operator to easily choose the
correct setup to produce the different rail
characteristics, including metallurgical
properties
.