Tech n ical p ape r – PCT Engineered Comparison of UV and EB Technology for Printing and Packaging Applications User Manual
Page 7
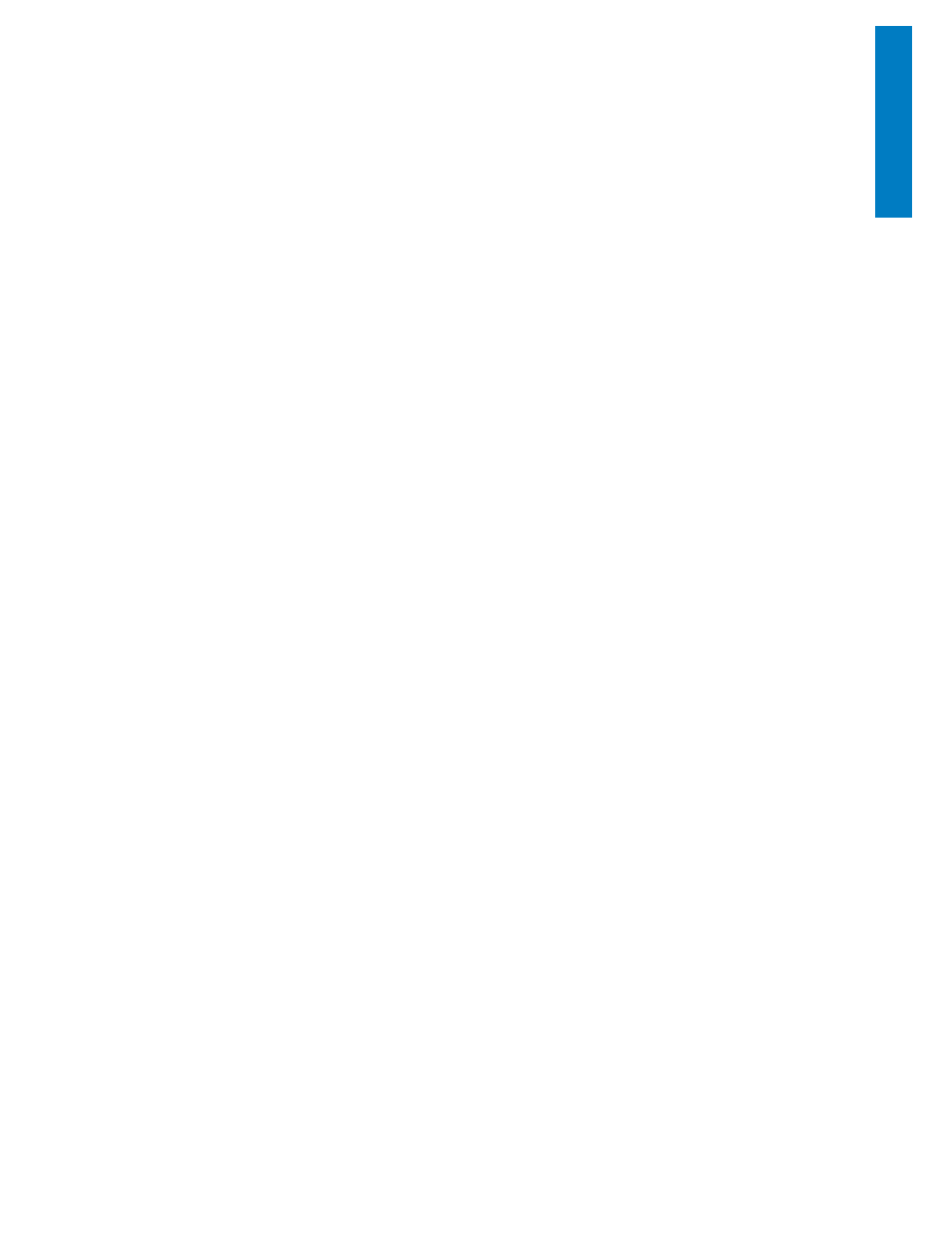
SEPTEMBER/OCTOBER 2008 RADTECH REPORT 33
Tech
n
ical P
ape
r
migration of the photoinitiator and
their fragments may be a concern.
EB curing of free-radical inks and
coatings requires inerting to displace
the atmospheric oxygen in the reaction
chamber of the cure unit. EB energy is
deposited more evenly throughout the
thickness of the ink and coating.
The absence of excess energy at the
surface does not allow curing reactions
to compete with oxygen termination
(Figure 1).
EB laminating involves irradiation
of the adhesive that is contained
between two layers of substrate. EB
laminating does not require inerting
because the substrates are generally
effective at preventing the diffusion of
oxygen into the adhesive layer.
Inerting is most commonly achieved
with nitrogen gas. Nitrogen serves to
displace oxygen from the reaction
chamber. The most common source of
the nitrogen gas is a tank of liquid
nitrogen. The liquid offers the high-
purity nitrogen and volume needed for
the curing process. Most modern EB
equipment is designed with nitrogen
knives to remove the surface boundary
layer of air. Optimized inerting systems
can reduce the amount of nitrogen that
is used.
13
Effect on Substrates
Since EB is ionizing radiation, it
may affect the thermal and mechanical
properties of substrates. EB affects
different polymer films in different
ways. References are available which
describe the effects. Fortunately, with
the relatively low dose (20 to 40 kGy)
used in most curing applications, the
effects are minimal and the films are
still fully functional for the intended
application. Another strategy to
minimize film damage is to use low
voltage in the range of 70 to 110 kV.
These voltages allow the beam to easily
penetrate the coating and ink layer
while minimizing the energy at the
inner (food contact) layer. This is
particularly important when the inner
layer is designed to be heat sealed when
the packaged is filled and sealed.
14
In some cases where porous
substrates (such as paper or cavitiated
films) are used, it can be advantageous
to use EB to cure materials which have
penetrated into the substrate.
EB’s effect on the substrate can be
beneficial. Cross-linking may enhance
the properties of some polyethylene-
based films. EB-induced ionization of
the film surface may result in
enhanced adhesion by grafting of the
ink or coating layer. EB can also
heat exposure. Most arc lamp-based
web systems include shutters to
prevent the web from burning when it
is stopped. Other strategies used to
minimize lamp heat effects on the
substrates include dichroic reflectors,
hot mirrors and chill drums.
15
EB is a cooler process compared to
UV. Some internal components of the
EB emitter (including the window)
utilize water cooling. Little heat is
transferred to the substrate which
allows most packaging films to run
without any effect on the dimensional
stability of the film. A chill drum may
be integrated into the EB unit for
potentially be used for simultaneous
curing and surface sterilization of the
food contact layer.
Since UV is non-ionizing radiation,
effects on the substrates are minimal.
Since grafting is not expected, a primer
layer may be needed for adhesion to
some films.
Heat Control
Mercury lamps used for UV curing
produce significant heat. This is due to
high temperatures needed to create
and maintain a plasma within the
quartz bulb. Approximately one-half
of the electrical energy input into
the lamp is converted to heat (IR)
energy. UV systems for printing and
packing applications are commonly
cooled by moving high volumes of air
over the lamp. Water-cooled lamps are
also available.
Many packaging films may be
adversely affected by heat from the
lamps. High-speed transport of the
substrate under the lamp minimizes
applications that are very sensitive to
heat. In this configuration the
substrate is in direct contact with the
chill drum during irradiation.
Food Packaging
UV-curable coatings and inks have
been used in food packaging applications
for many years. These applications are
possible with packaging designs that
include a functional barrier between
the ink or coating and the food. Taint
and odor problems can usually be
prevented by using properly formulated
UV-curable inks and coatings.
Photoinitiators and photoinitiator
fragments can be a source of concern
for migration, odor and taint. New
systems have been developed that
include polymeric photointiators,
reactive photointiators,
16
and oligomers
that contain a “built-in” photoinitiator
moiety.
17
Some of these systems have
been effective but may still lack cost/
performance properties needed for
practical applications.
In general, there does not tend to be a significant
difference in cost between UV and EB inks,
coatings and adhesives for printing and
packaging applications.