Warner Electric E220 Electromagnetic Single Disc User Manual
Page 3
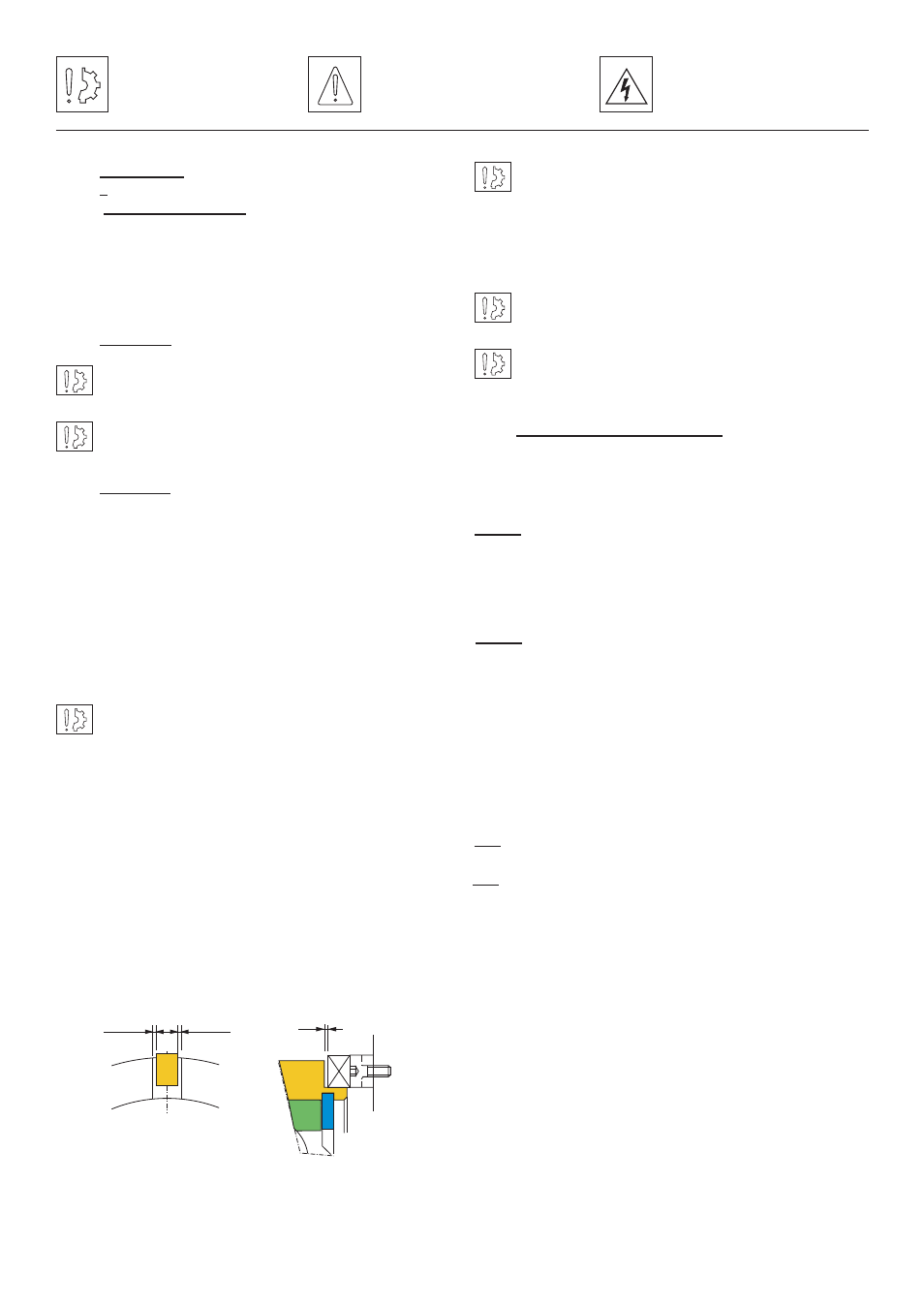
Warner Electric Europe • +33 (0)2 41 21 24 24
P-2033-WE • 2/13 3
In the case where two co-axial shafts are
fitted, the recommended set over is 0,05 mm
maximum. The angular misalignment should
not be greater than 0,1 mm over a length of 100
mm. If this is the case, use a VAR05 (flexible
coupling).
Never dissociate the assembled moving
armature (331) (specially factory assembled).
Never pull or hit the assembled moving armature
(331), which risks permanently deforming the
elastic arms.
3.3.1 Installing VAR00 and VAR02
After adjusting the drive keyway, fit the assembled
induc tor onto the shaft and clamp it axially.
VAR00:
After adjusting the drive keyway, fit the assembled
moving armature (331) on the shaft and clamp it axially
on the shaft.
VAR02:
Fit the assembled moving armature (331) onto its
support housing and clamp it axially.
It is essential when assembling the 2 parts to respect
the travel P (measured in disengaged position) (see
appendix 1). To ensure axial wedging, provide for this
purpose adjustment spacers in the adaptation. Also
check, in the disengaged position, the free rotation,
without contact, of the moving armature assembly
(331).
NB: In operation, the adjusted travel at start-up can
reduce, the moving armature not returning to its initial
position. It is not necessary to make a further adjustment
unless there is rubbing, in the disengaged position,
between the friction surfaces.
3 Installation
3.1
Transport / storage
Our clutches and brakes are supplied in packaging
guar anteeing a preservation period of 6 months with
land or air transport, or after transport by ship to
neighbouring conti nents (without crossing the tropics).
3.2
Handling
Avoid any impacts on the equipment so as not
to alter their performance.
Never carry the equipment by the electrical
supply cable.
3.3
Installing
E210 clutches are supplied reamed to tolerance H7 and
splined to tolerance P9 to NF E22175/DIN6885/ISO
R773/BS 4235.
E220 clutches are supplied hubs reamed to tolerance H7
and splined to tolerance P9, and armatures assembled
reamed to tolerance H8.
We recommend a tolerance H6 for the shaft and F7 the
centring of the assembled armature.
Important: Do not forget to stop the inductor
(101) rotating by means of a fixed part shaped in
the slot.
Check the play between the inductor and this part (see
fig. 1): 0,5 minimum in rotation - 1 mm at base of slot.
The part should not cause any strain on the bearings. In
case of vibrations, it is strongly recommended to insert a
damp ing elastic slot between the anti-rotation device and
the anti rotation slot and to fix the coil’s cable the nearest
of it to avoid whipping.
Symbol designating
an action that might
damage the brake
Symbol designating an action
that might be dan gerous to
human safety
Symbol designating an
elec trical action that might be
dangerous to human safety
1
0,25
0,25