Warner Electric ER 825 and 1225 Heavy Duty User Manual
Page 3
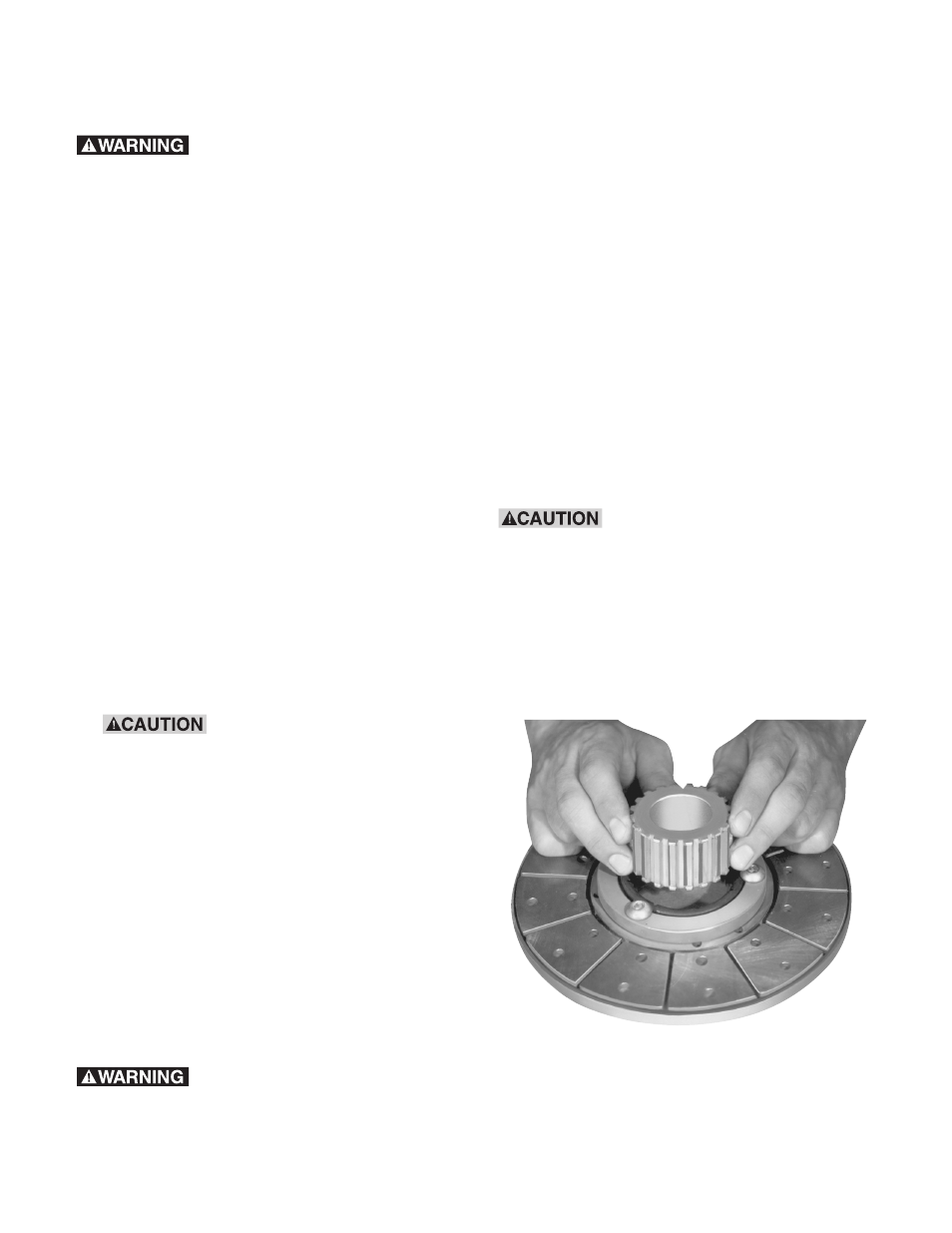
3
Warner Electric • 800-825-9050
P-251 • 819-0121
Sizes ER-825 and ER-1225 with Spline
Drive Armatures Installation Instructions
Failure to follow these
instructions may result in product damage,
equipment damage, and serious or fatal injury
to personnel.
Basic Mechanical Considerations
Electrically released brakes require special
mounting considerations. Please review the items
listed below prior to starting installation contained in
steps 1-12.
A. If the brake magnet is to be mounted to
a surface of magnetic material, isolate the
brake approximately 1/2 inch from the
surface with a plate or spacer of non-
magnetic material.
B. If a choice of armature shaft material exists, this
should also be nonmagnetic. Materials such as
type 302-304 stainless have been used very
successfully.
C. In order to minimize stray flux, the unit should be
exposed as much as possible or, if enclosed, it
should be placed in a housing of nonmagnetic
material such as stainless steel or aluminum.
D.
must be exercised when the
armature is moved close to the magnet
assembly since the permanent magnets create a
very strong attractive force. Injury may result if
fingers are in between the armature and
magnet when the gap is 1/2" or less.
E. Foreign Materials: If units are used on
machinery where fine, abrasive dust, chips, oil or
grit are dispelled into the atmosphere, a
protective screen over the unit may be
necessary. Where units are used near gear
boxes or transmissions requiring frequent
lubrication, means should be provided to
protect the friction surfaces from oil and
grease to prevent serious loss of torque
Applications requiring a vertical
shaft mounting must be reviewed and approved
by Warner Electric Applications Engineering.
Note: Failure to set control voltage using the step by
step procedures in this manual may cause
overheating and premature failure.
Section 1
Step 1:
Check to insure that the magnet and its
mounting surface are clean and free from burrs.
Step 2:
Bolt the magnet in place with capscrews and
lockwashers.
Note: The magnet pilot diameter must be concentric
to the shaft within .010 inch T.I.R. The magnet
mounting surface must be square with the shaft
within .006 inch T.I.R. measured at the bolt circle.
Step 3:
Assemble the splined armature assembly
(armature, splined armature adapter and autogap are
preassembled) to the hub.
New armatures shipped from the
factory are flat to within .005 inch and this
flatness must be retained to maintain full torque.
Any attempt to pry the armature loose from the
magnet will distort the armature. When
adjusting the armature position, apply any
required force only to the hub, not to the outer
edge of the armature. Also, use care when
handling the armature as dropping may also
cause distortion.
Figure 1
Step 3A:
Place the armature-splined adapter assembly
on a flat surface, segments up. Press the splined hub
(retainer ring end first) through the autogap spring and
splined armature adapter.