Warner Electric FB-375, 475, 650 User Manual
Page 6
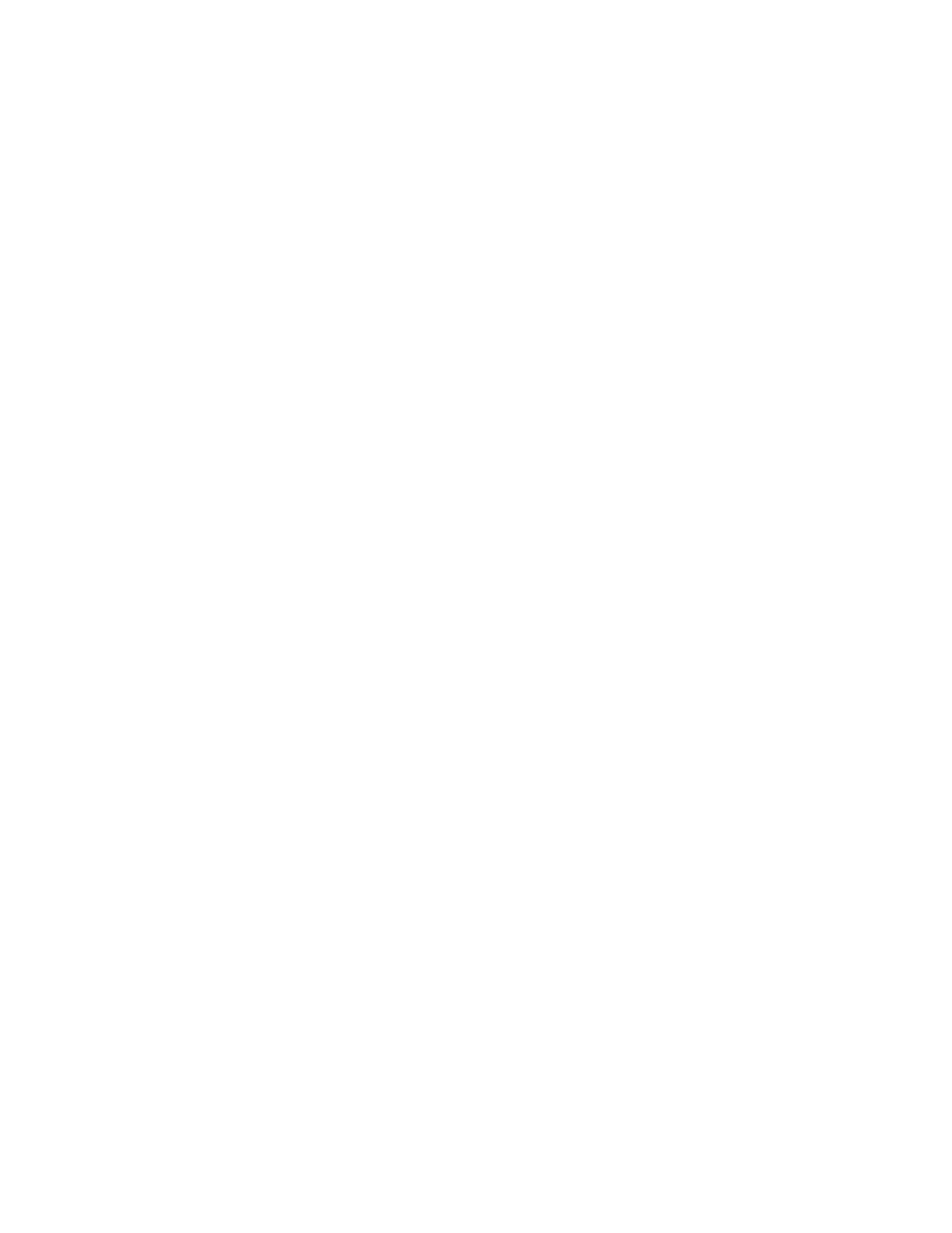
6
Warner Electric • 800-825-9050
P-237 • 819-0289
Power Supplies for Electrically Released
Brakes. Electrical Connections and
Adjustments.
Step 4:
Connect the brake to an adjustable
voltage/current control following the
instructions for that control. Warner Electric’s
controls are suitable for these brakes.
Note: FB brakes are polarity sensitive.
The positive terminal of the brake must be
connected to the positive terminal of the
control and vice versa.
Note: For failsafe or Electrically released
brake units (FBB, MBFB, FBC, ER or FB)
see instruction on proper electrical setup
procedure.
Instructions for setting the optimum
release voltage of permanent magnet
applied/electrically released brakes
In a permanent magnet applied/electrically
released brake, the attractive force between the
brake surface is created by permanent magnets.
The brake is electrically released by applying DC
power to the electro-magnetic coil in the brake
that opposes the permanent magnets. Electrically
released brakes are polarity sensitive: the positive
lead of the power supply must be connected to
the positive lead of the brake, and the negative
lead of the power supply must be connected to
the negative lead of the brake. The power supply
applied to the brake must also be adjustable so
that the optimum release voltage for each
individual brake can be determined and set.
The following procedure describes how to set the
adjustable power supply to the optimum release
point of the brake. A volt-meter is required to
perform the procedure.
1. With the power off, connect the positive lead
of the power supply to the positive lead of the
brake and the negative lead of the power
supply to the negative lead of the brake.
2. Connect a volt-meter to measure the voltage
applied across the brake.
3. Adjust the power supply to its lowest
possible output, then energize the supply to
apply power to the brake.
4. Starting from the low point, slowly increase
the applied voltage until the brake armature
disengages from the magnet. Note and
record the applied voltage at this point.
5. Continue to slowly increase the applied
voltage until the armature re-engages the
magnet. If the maximum voltage available
from the supply does not cause the armature
to re-engage, the armature should be
manually assisted into engagement.
6. With the armature re-engaged, slowly
reduce the applied voltage until the armature
disengages from the magnet. Note and record
the applied voltage at this point.
7. The optimum release point for the brake is
half-way between the two recorded voltage
readings. Adjust the supply to this optimum
release voltage.
Autogap Adjustment
Step 5:
Turn the power on to electrically release the
brake. The armature should spring back
approximately 1/32-inch as shown. If the
armature fails to disengage, turn the control
knob on the brake control CCW to 0 and then
CW until the armature releases. You’ve now
reached the minimum release voltage. The
knob can be turned further CW to find the
most favorable release point.
If the armature
does not spring back, follow the autogap
adjustment procedure as follows (refer to
Figure 6):