LEESON Micro Series Compact Inverters User Manual
Page 67
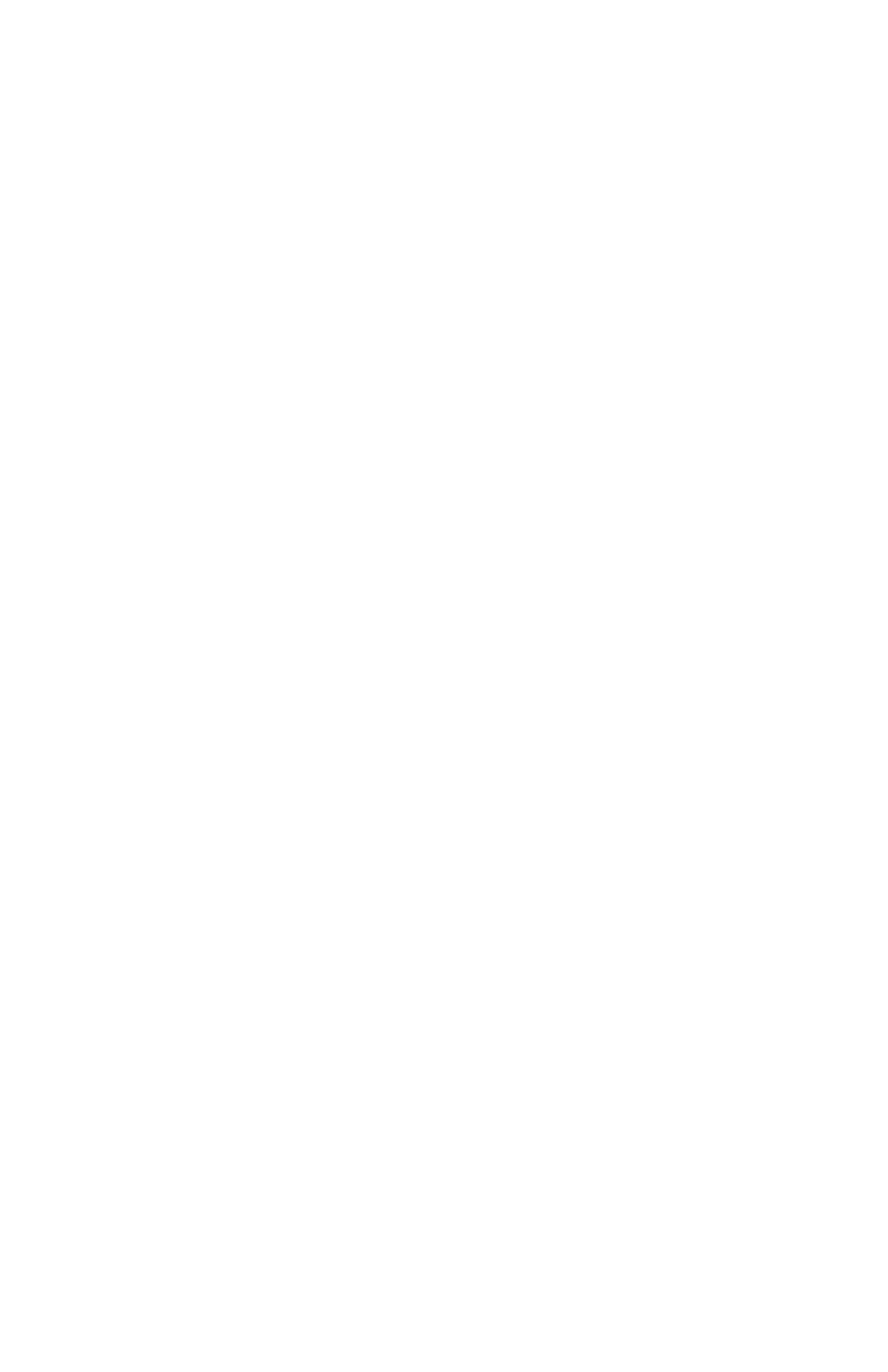
Example:
SLEEP THRESHOLD is set to 15 Hz and SLEEP DELAY is set to 60 seconds. If the drive
operates below 15 Hz for 60 seconds, the drive will “go to sleep” and the motor will stop. The drive’s
display will indicate SLEEP, and the drive will remain “sleeping” until the drive commanded to a speed
equal to greater than 17 Hz. At this point, the drive will “wake up” and ramp the motor up to the
commanded speed .
38
SLEEP BW
(SLEEP BANDWIDTH)
This parameter allows the PID feedback signal to determine when drive should “wake up” when operating
in Sleep Mode. In process systems that utilize Integral Gain (see Parameter 78), the drive may cycle in and
out of Sleep Mode more often than desired, due to the Integral function of the PID algorithm .
When SLEEP BANDWIDTH is used, the feedback signal must decrease or increase (depending on whether
the system is normal or reverse-acting) by the programmed amount before the drive will “wake up”. This
parameter is set in PID units .
Example:
In a normal-acting system, the PID set point is 50 PSI, SLEEP THRESHOLD is set to 20 Hz,
and SLEEP BANDWIDTH is set to 5 PSI . The drive will enter Sleep Mode when the commanded speed
drops below 20 Hz for the time defined in SLEEP DELAY. The drive will wake up when the feedback
signal drops below 45 PSI (50 PSI set point minus 5 PSI bandwidth = 45 PSI), even if the commanded
speed is still below 20 Hz.
NOTE:
If SLEEP BANDWIDTH is set to 0, this function is disabled, and the drive will wake up when the
commanded speed exceeds the SLEEP THRESHOLD plus 2 Hz, as described in Parameters 36 and 37.
39
TB5 MIN
(TERMINAL TB-5 INPUT)
TB5 MIN selects the output frequency of the drive that will correspond to the minimum analog speed
reference input (0 VDC or 4 mA). This parameter is used in conjunction with Parameter 40 - TB5 MAX
to define a speed range that corresponds to the analog speed reference input (0 - 10 VDC or 4 - 20 mA).
40
TB5 MAX
(TERMINAL TB-5 INPUT)
TB5 MAX selects the output frequency of the drive that will correspond to the maximum analog speed
reference input (10 VDC or 20 mA). This parameter is used in conjunction with Parameter 39 - TB5 MIN
to define a speed range that corresponds to the analog speed reference input (0 - 10 VDC or 4 - 20 mA).
Example 1:
The drive is required to operate from 0 to 60 Hz in response to a 0-5 VDC speed reference
signal (rather than the “normal” 0-10 VDC). Because TB5 MAX is based on a 0-10 VDC (or 4-20 mA)
signal, the drive will operate at half of the TB5 MAX value if it is given a 5 VDC signal . Therefore, setting
TB5 MAX to 120 Hz will cause the drive to run at 60 Hz when it is given a 5 VDC speed reference signal.
NOTE:
The drive can be programmed for inverse operation so that as the speed reference increases, the drive
speed will decrease, and as the speed reference decreases, the drive speed will increase . This is accomplished
by setting TB5 MIN to the desired maximum output frequency, and TB5 MAX to the desired minimum
output frequency.
Example 2:
The drive is being controlled by a pressure transducer that provides a 4-20 mA signal
proportional to duct pressure. The minimum frequency desired is 20 Hz, and the maximum is 60 Hz. Set
TB5 MIN for 60 Hz, and TB5 MAX for 20 Hz. As the duct pressure rises, the output signal from the
transducer will increase, causing the speed of the drive to decrease . This results in a decrease in duct pressure
and a decreasing transducer signal . The drive responds to the decreasing signal by increasing speed, which
again raises the duct pressure . In this way, the average duct pressure can be maintained at a certain level . If
the acceleration and deceleration rates are set too fast however, the drive will react quickly to signal changes
which will cause the drive speed to “hunt” up and down excessively.
65