KB Electronics KBRG-212D User Manual
Page 21
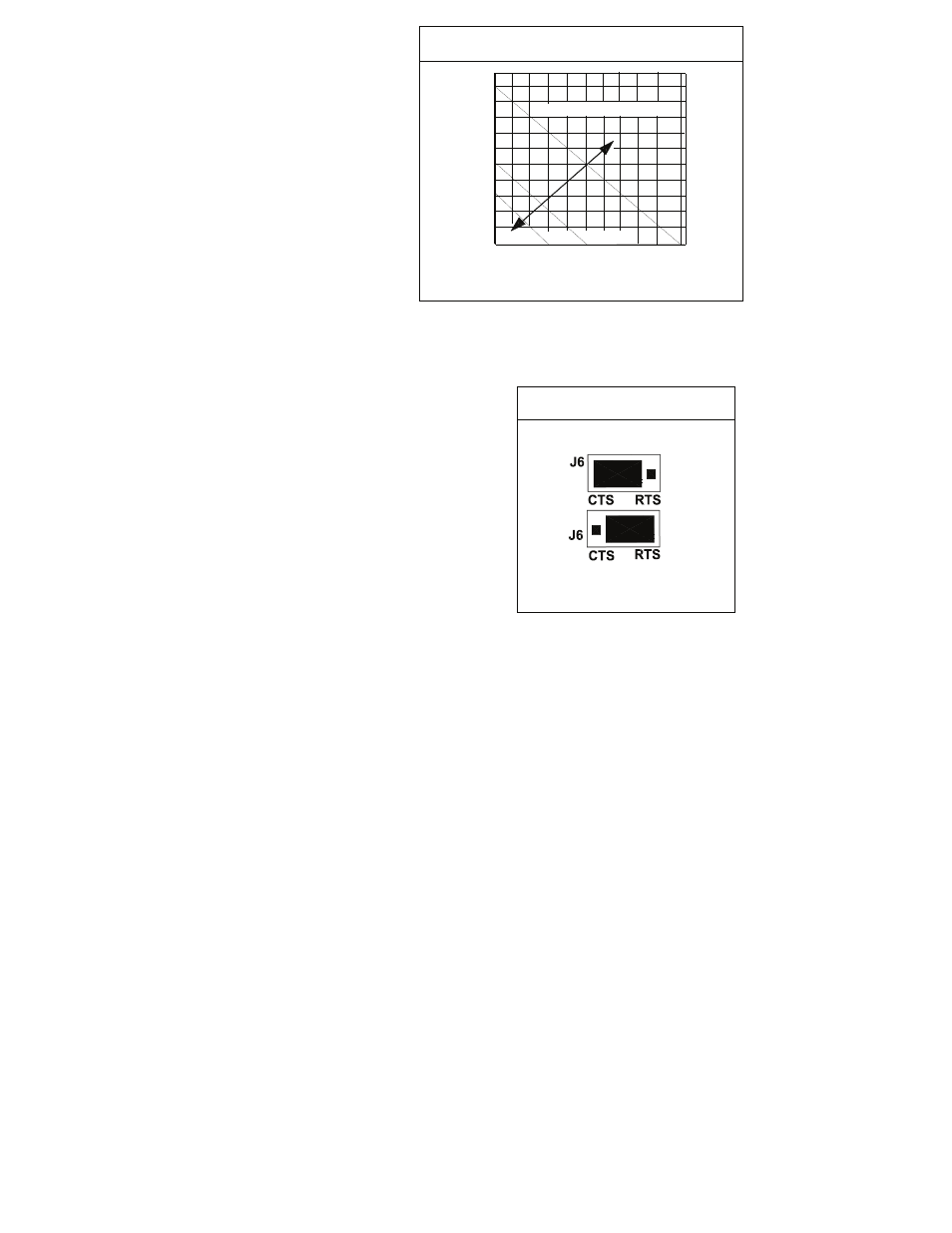
21
In the torque control mode
(J5 set to TRQ), the
KBRG-212D will vary the
maximum motor torque as
a function of the voltage
input to terminals “SIG”
(signal) and “COM”
(common). This voltage
can be derived from the
wiper of the main
potentiometer or from an
analog input (voltage
following). If the motor
torque is greater than the
load torque, the motor will
rotate. If no load is
applied to the motor, the
motor will rotate at a
speed proportional to the
torque setting as set by
the main potentiometer (See Figure 13, on page 21). By using the FACC and RACC
Trimpots, the application of torque can be made more gradual or less gradual as
required by the application. A maximum torque can be established using the current
selector jumper, J2, which can be further modified by using the FCL and RCL Trimpots.
7.4 J6 – Coast to Stop (CTS) Regenerate to
Stop (RTS)
-
This function operates in
conjunction with the Enable circuit, which is
used to start and stop the control
electronically. If the circuit connecting
terminals “EN” and “COM” on terminal block
TB1 is opened, the control will cause the
motor to stop. When jumper J6 is in the
factory position (
RTS), the motor will
regenerate to a stop. The stop time is
controlled by the Forward Acceleration
(FACC) and Reverse Acceleration (RACC)
Trimpots. If J6 is changed to the coast to stop
(CTS) position, the motor will coast to a stop
when the “EN” - “COM” circuit is opened. See
Figure 15.
Note:
Control will not run unless a jumper or closed contact is connected between the
“EN” and “COM” terminals.
FIGURE 14 - MOTOR SPEED vs.
APPLIED MOTOR LOAD (TORQUE MODE)
APPLIED MOTOR LOAD (%) TORQUE
MOT
O
R S
PEED (
%
)
HIGHER TORQUE SETTING
100
90
80
70
60
50
40
30
20
10
0
0 10 20 30 40 50 60 70 80 90 100
LOWER TORQUE SETTING
FIGURE 15 – J6
CTS / RTS JUMPER
(Coast to Stop)
(Regenerate to Stop)
Shown in the Default Position