Ransburg, Null data - type 00, Operational data - type 01 – Ransburg DynaFlow Programmers Manual User Manual
Page 14: Dynaflow, Programer's manual - introduction
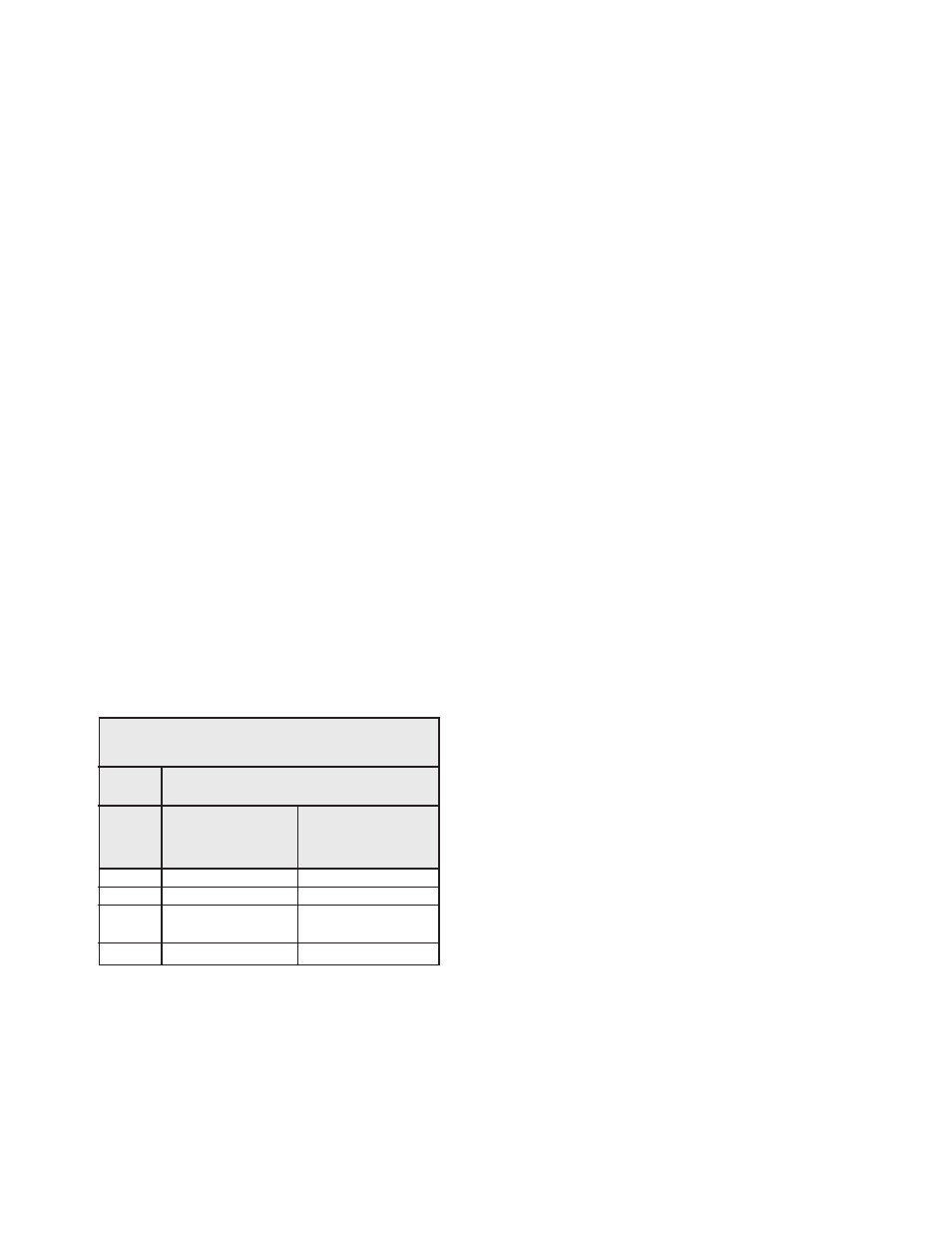
The System Configuration and Gun Configuration
data must be sent first to the DynaFlow Interface
Module when the system is powered up, or com-
missioned for the first time. The Job Table data
must then be sent for each Job for each Gun.
The configuration and flow totals data are stored
in non-volatile memory in the DynaFlow Interface
Module and therefore do not need to be sent
after a power cycle unless only to "Refresh" the
information to be certain of its content.
All gun, channel, and job numbers are sent as
one-based values. In other words, gun or channel
numbers are sent as 1 to 8 and job numbers are
sent as 1 to 100.
Null Data - Type 00
A BTW must always precede a BTR in order to
inform the DynaFlow Interface Module what data
is to be returned in the next BTR. Null BTW com-
mands can be used when no data must be sent
prior to the next BTR. If the next BTR Type does
not require a Gun # or Channel # and/or Job #,
those fields may be zero. Otherwise, the Next BTR
Type, Gun # or Channel # and Job # specify the
appropriate data to be returned in the next BTR.
Word
Description
0
1
2
3
BTW Type
Next BTR Type
Next BTR Gun #
or Channel #
Next BTR Job #
Units/
Value
00
00, or 01 to 08
0, or 1 to 8
0, or 1 to 100
NULL DATA - TYPE 00
BTW
The gun job numbers and set points may be
specified as zero if no change is desired for a gun.
However, if a set point is specified as non-zero, a
valid job number must be specified.
In PID Mode, the set point is cc/minute.
In Transparent Mode, the Gun Set Point represents
a 0 to 100% request that is passed directly to the
analog output. For 2K operation, the lower byte is
the % resin and the upper byte is the % catalyst,
where 0 to 255 reperesents 0% to 100%.
In Open Loop mode (Transparent mode with DIP
switch 3 up on the Channel Card), the set point
value is used directly as a cc/minute set point to
use for picking an output value from the Lookup
Table.
Operational Data - Type 01
RIO Operational Data block transfers are used for
normal process control while painting parts. This
assumes the system and applicators have been
initially configured.
10
DynaFlow
Programer's Manual - Introduction
Ransburg
LN-9406-00.3