Maintenance, Wear adjustment, Torque adjustment – Dings Dynamics Group 60 Series End Mount NEMA 4X User Manual
Page 5: Pivot stud adjustment, Friction disc replacement
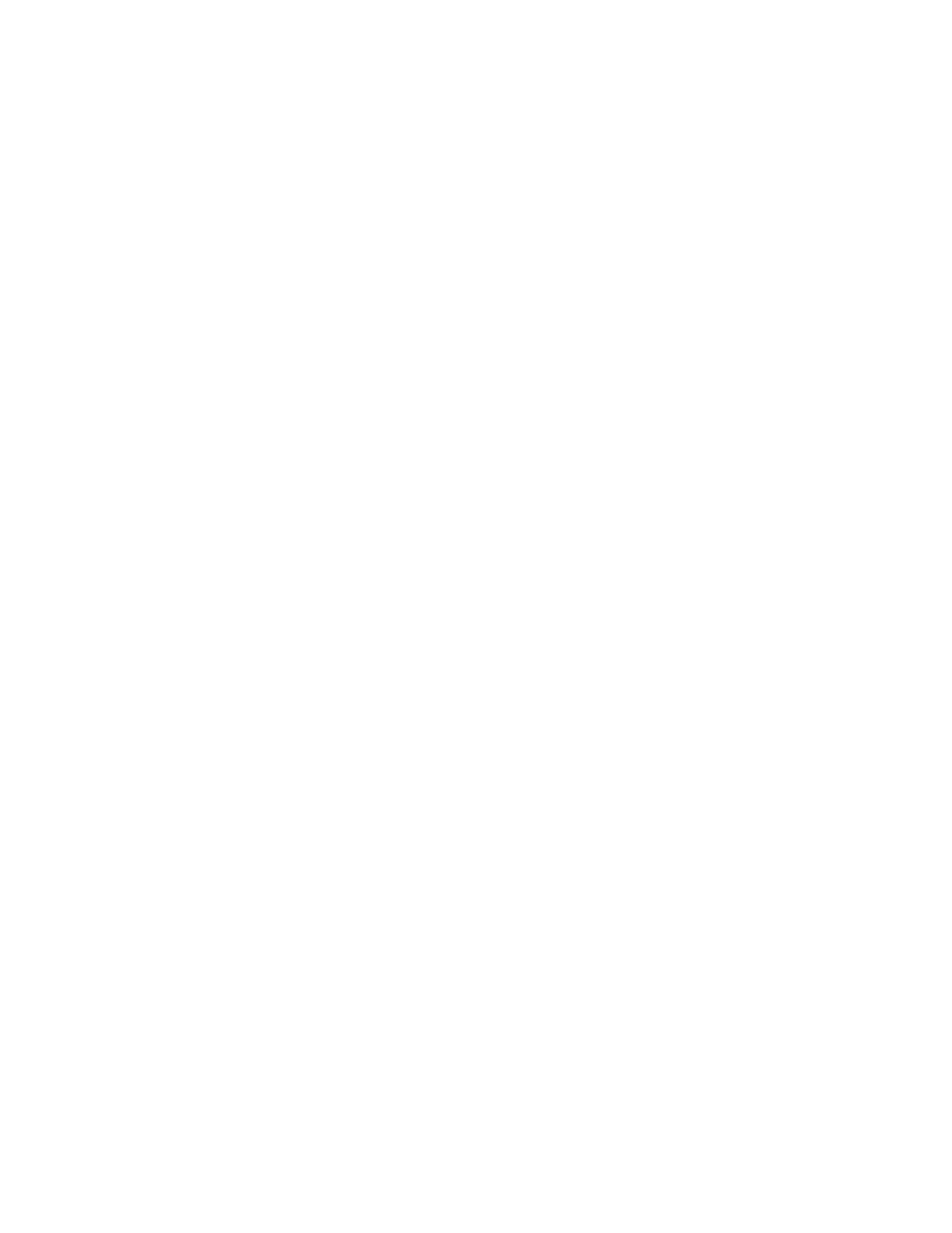
MAINTENANCE
CAUTION: Before attempting to service or remove
any components, make certain that the power is
disconnected and that the load is completely removed,
secured or blocked to prevent injury or property
damage.
Wear Adjustment
CAUTION: Load to be removed or blocked. Brake will be
inoperative during this procedure.
Refer to Fig. 4.
Before air gap “A” reaches .100”, adjustment is required. Any
delay in adjusting the magnet air gap will result in eventual
loss of torque.
1. To adjust, remove cover acorn nuts (23), washers
(22), and pull cover (20) off to expose adjusting
screws (15H) and magnet air gap “A”. (You may
have to tap lightly with a rubber mallet.)
2. Measure air gap “A” using 3/8” to 1/2” wide feeler
gauge. (Measure at center of magnet.)
3. Turn two square head adjusting screws (15H) until
air gap “A” measures:
.045/.050 for 1 disc models
.050/.055 for 2 disc models
.060/.065 for 3 or 4 disc models
Air gap should be the same on both sides.
Torque Adjustment
Caution: Load to be removed or blocked. Brake will be
inoperative during this procedure.
Refer to Fig. 4.
The magnetic disc brake is factory set for rated static torque.
The brake can be adjusted to reduce torque which increases
stopping time. Do not attempt to adjust brake for higher
torque, as this will cause premature coil burnout.
1. To adjust, remove acorn nuts (23), washers (22),
and pull cover (20) off to expose torque locknuts
(15T), which are above torque springs (15S).
2. To increase stopping time and reduce torque, turn
two locknuts (15T) counterclockwise, increasing
spring length. Each full turn reduces torque 7% to
10% depending upon the model.
Pivot Stud Adjustment
CAUTION: Load to be removed or blocked. Brake will be
inoperative during this procedure.
This adjustment is made at the factory and may be required
when replacing the magnet assembly (15A) or the armature
(15J).
The purpose is to regulate the height of the armature plate
(15F) so that when the magnet (15A) is energized, the
armature (15J) is parallel with it. This is required for quiet
operation.
1. Remove cover acorn nuts (23), washers
(22), and pull cover (20) off. (You may
have to tap lightly with a rubber mallet.)
2. To adjust, hold the nut (19) which is adjacent to
washer (18) and loosen the other nut (19) and
remove it from the stud.
3. Energize the magnet and turn remaining nut (19)
counterclockwise slowly until the magnet becomes
noisy. Turn magnet on and off serveral times until
you find the position where the magnet first becomes
quiet.
At this point, turn nut (19) 1/3 turn (two flats) in a
clockwise direction. Hold nut in this position and turn
magnet on and off to make sure the magnet does not
become noisy.
4. Holding this nut in place, screw on other nut and
tighten it against the nut you are holding. Tighten
firmly.
5. Operate the manual release. If the release does not
operate properly, see “Manual Release Adjustment”
on page 7.
Friction Disc Replacement
Caution: Load to be removed or blocked. Brake will be
inoperative during this procedure.
If brake model number has a prefix VO or VU, see
page 8.
When total wear on a rotating friction disc (13) reaches
1/16”, replace disc, referring to Figs. 4 and 10:
1. Disconnect power.
2. Remove cover per step 1 under “Wear Adjustment”.
3. Remove operator assembly (15) by removing screws
(16) and pivot stud (10). Item 10 has a hex socket in
end of stud for removal.
NOTE: Do not loosen nuts (19) on pivot stud (10),
or “Pivot Stud Adjustment” (on page 6) will have to
be made. Retain loose parts; washer (18), bushing
(17), and compression spring (11).
4. Replacing the friction disc
Remove worn rotating discs (13) and stationary discs
(12). Replace worn discs and install new discs in the
same order. Install stabilizer clip (14), if furnished, on
rotating discs prior to installing.
5. Re-assembly of operator assembly (15)
Turn two screws (15H) counterclockwise five turns.
Place operator assembly (15) onto brake bracket (2)
and install two screws (16). Replace compression
spring (11), bushing (17), washer (18), and pivot
stud (10) which has the two nuts (19) in place.
Tighten firmly.
6. Readjust magnet air gap “A” as described under
“Wear Adjustment”.
7. Check manual release operation before replacing
cover. Adjust per “Manual Release Adjustment”
on
page 7
if required.
8. Replace
cover
(20), washers (22), and acorn nuts (23).
Tighten nuts to 5 lb-ft. of torque.
5