Cashco 521 User Manual
Page 14
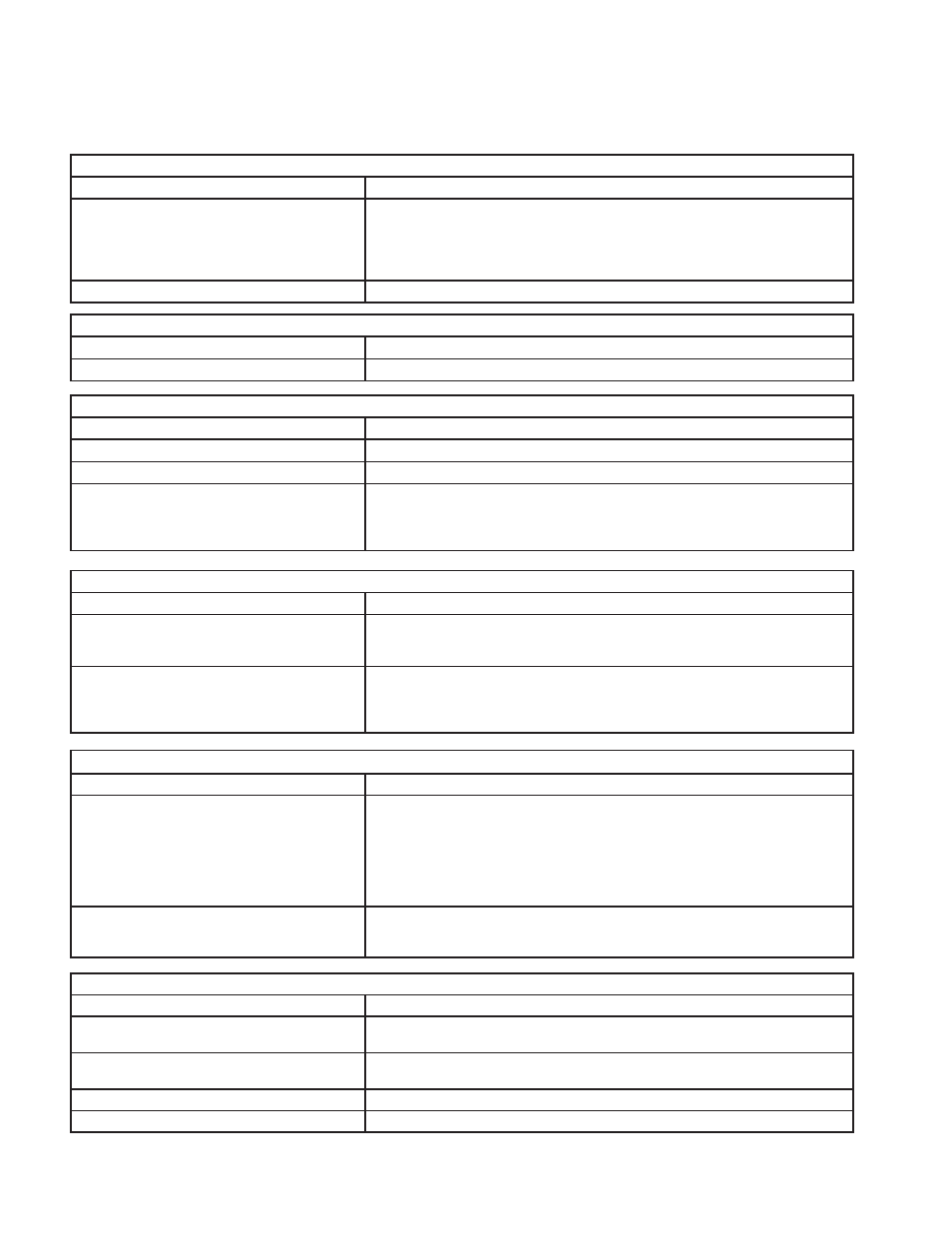
IOM-521
14
SECTION VII
VII. TROUBLE-SHOOTING GUIDE:
1. Valve is "jumpy" in stroking.
Possible Causes
Remedies
A. Excess packing friction.
A1. Re-align body--stem--actuator.
A2. Packing follower too tight; back packing gland nut out.
A3. Install positioner.
A4. Increase bench set by changing to stiffer actuator range spring. May require
positioner if not installed. May require different airset.
B. Installed
backwards.
B. Install
per
fl ow arrow. Direction is only FTO.
2. Valve/actuator makes "screeching" noise.
Possible Causes
Remedies
A. Excess pressure drop.
A. Bring pressure drop within design limits.
3. Valve exhibits "excess" vibration.
Possible Causes
Remedies
A. Excess pressure drop.
A. Bring pressure drop within design limits.
B. Excessive cavitation in liquid service.
B. Change operation parameters to relieve causes of cavitation.
C. High outlet velocity.
C1. Reduce fl ow rate and/or pressure drop.
C2. Use multiple valves in series or parallel.
C3. Increase outlet pipe size.
C4. Use larger valve body with reduced trim.
4. Valve exhibits "excess" seat leakage.
Possible Causes
Remedies
A. Excess pressure drop.
A1. Reduce pressure drop conditions.
A2. Convert to reduced trim.
A3. Increase actuator thrust by changing actuator range spring.
B. Excess body and/or plug wear.
B1. Oversized valve operating too close to seat; go to reduced trim.
B2. Remove abrasive particulate.
B3. Possible excess cavitation in liquid service. Change operation parameters.
B4. Replace body assembly if seat is badly worn. Replace plug if badly worn.
5. Bonnet gasket leakage.
Possible Causes
Remedies
A. Improper bonnet bolting drawdown.
A1. Remove bonnet taking necessary safety precautions. Inspect bellows to
determine if primary seal at body/bellows is damaged. If bellows is damaged,
replace
bellows.
A2. Inspect secondary seal bonnet gasket for uneven thickness.
Replace bonnet gasket.
A3. Draw down bonnet bolting evenly and in a cross pattern; use bonnet bolting
torque levels indicated herein.
B. Cantilevered actuator.
B1. Do not allow use of the actuator as a "step" upon which personnel may climb.
B2. Do not "set" any added weight on the actuator.
B3. Install vertically.
6. Body fl ange leakage.
Possible Causes
Remedies
A. Over-tightening
fl ange bolting.
A. Loosen bolting, replace/install new gasket, retighten fl ange bolting in s
cross-pattern
evenly.
B. Improper pipe supports and anchors.
B. Provide piping anchors and guides at control valve station.
Restrain bending movements.
C. Corroded
fl ange bolting.
C. Replace with corrosion resistant fl ange bolting.
D. Used outside pressure/temperature limits.
D. Bring process variables within range of application; see Graph 1 in 521-TB.