Cashco 964 User Manual
Page 7
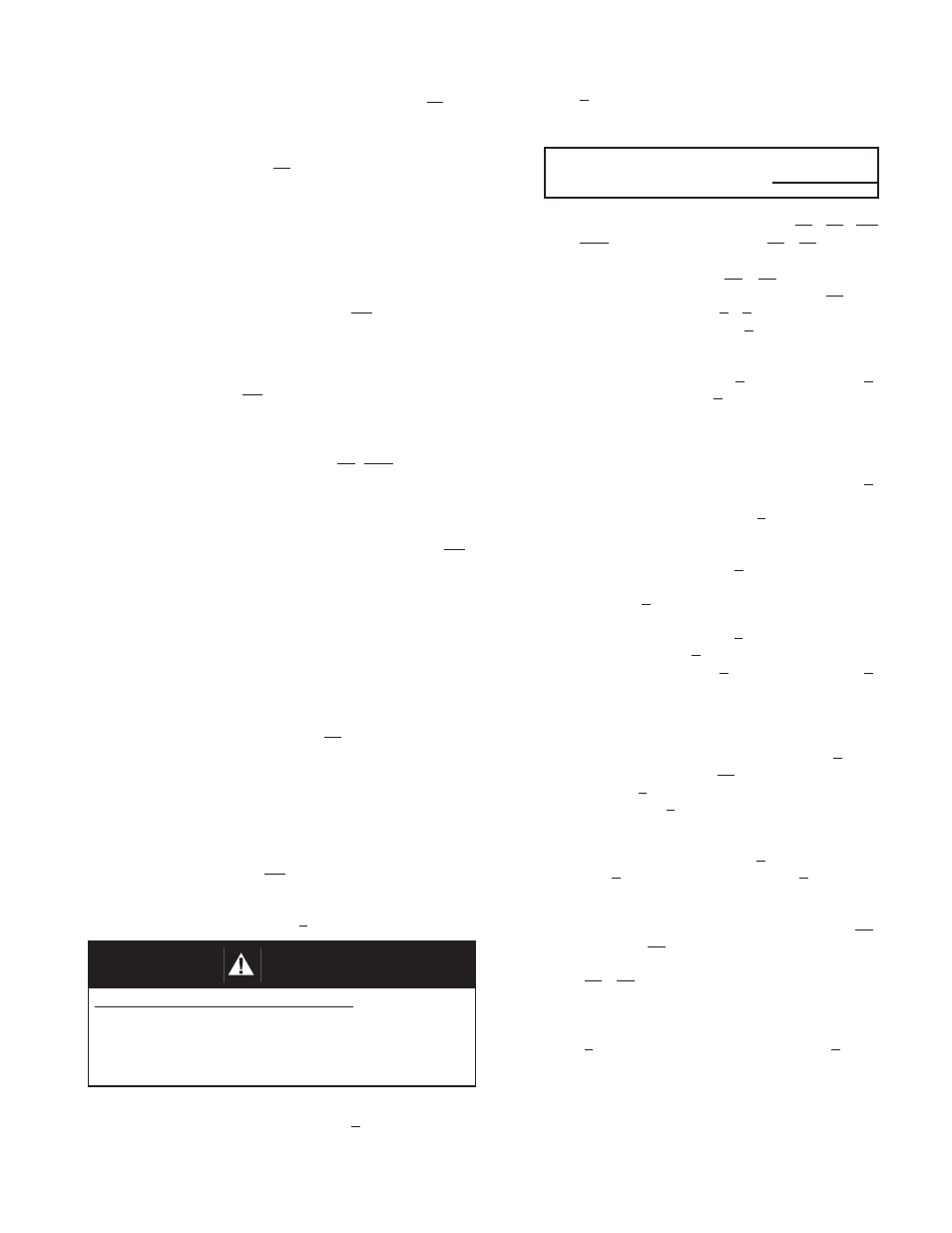
IOM-964
7
(6) is fully re laxed. Record the num ber of
rev o lu tions required to loos en; record in the
fol low ing box:
29. Engage valve stem (3) into ac tu a tor stem (19) the
same number of rev o lu tions recorded in Step 9.
30. Tighten both jam nuts (18) up against position
in di ca tor plate (20).
31. Tighten packing nuts (15) evenly in ½ revolu-
tion increments, until the packing fl ange (4)
is resting evenly on the upper edge of the
bonnet (2) at the stuffi ng box. Snug both nuts
(15) tightly.
32. Raise actuator assembly (AA). (Note RP.)
Lower into body (1) over bonnet studs/bolts
(16). Align with match marks.
33. For ATO-FC action units, wiggle the ac tu a tor
as sem bly (AA) to assist in align ment.
34. For ATC-FO action units, pres sur ize ac tu a tor
to the “high er” number of the bench set range
in di cat ed on nameplate (12) plus 2 psig (.14
Barg); for 3-13 psig (.21-.90 Barg) bench set-
ting, pres sur ize to 15 psig (1.03 Barg). This
should “lift” the bonnet (2) and “seat” the plug
(3) fi rmly into the seat ring (11) for align ment
pur pos es. Wiggle the ac tu a tor as sem bly (AA)
to assist in align ment.
35. Wrench-tighten the bonnet bolt ing (16) (17) in
an al ter nat ing cross-pat tern in 1/4 rev o lu tion
in cre ments. Torque bonnet bolt ing to 50-55
ft/lbs (66-73 N-M).
36. For ATC-FO action units, release ac tu a tor
pres sure.
37. Hammer rap yoke nut (17) tight. It was loos-
ened in Step 16a.
38. Calibrate unit per Section V.
E. Diaphragm
Replacement:
1. Place valve’s body (1) in a vise with the ac tu a-
tor as sem bly (AA) directed up wards.
2. Release all air pressure loaded into the ac tu a-
tor’s upper casing (2).
Number of revolutions required
to relax actuator range spring:
WARNING
SPRING UNDER COMPRESSION! Pri or to re-
mov ing actuator cas ings’ bolting, re lieve spring
compression by backing out the spring ad jus tor.
Fail ure to do so may result in fl ying parts that could
cause per son al in ju ry.
4. Fully remove all casing bolting (10) (11), ex-
cept for two sets of bolting (10) (11) that are
180° across from each other. Loos en these
fi nal sets of bolting (10) (11) in al ter nat ing
se quence one rev o lu tion of the nut (11) at a
time. If the casings (2) (3) pull apart on their
own, the spring adjustor (4) may require more
loos en ing. Go back to 3 above.
5. Remove upper casing (2). Lift di a phragm (7)
from lower casing (3) fl ange. A putty knife
or similar device may be re quired to help
sep a rate.
6. Place a wrench on the lower stem jam nut
(18) and loosen diaphragm wash er nut (9)
CCW (viewed from above) to re mov al. Re-
move diaphragm washer (8); use putty knife
if nec es sary to pry away.
7. Remove di
a phragm (7) and ex am ine for
pos si ble cause of failure. Dis card used di a-
phragm (7).
8. Clean
di
a phragm plate (5), if nec es sary. Place
new di a phragm (7) into po si tion, align ing bolt
holes of di a phragm (7) with lower casing (3)
holes.
9. Apply a silicone rubber ad he sive/seal ant
sim i lar to Dow-Corning “Silastic” #732RTV at
the junc ture of the di a phragm plate (5) and
the ac tu a tor stem (19). Place di a phragm
washer (8) into po si tion. Tight en di a phragm
wash er nut (9) to 35 ft/lbs. (47 N-M) torque
using torque wrench.
10. Reposition upper casing (2) with low er cas-
ing (3) fl ange with diaphragm (7) be tween
fl ang es.
11. Reinstall diaphragm bolting cap screws (10)
and nuts (11); wrench-tighten fi rmly in al ter-
nat ing cross ing pattern. Fi nal-tight en bolt ing
(10) (11) to 20-25 ft/lbs (27-34 N-M) torque
using torque wrench.
12. Reapply compression to the range spring
(6) by ro tat ing the spring adjustor (4) CW
(viewed from plug end) the same num ber of
rev o lu tions re cord ed in box of Step 3, this
sub-section.
3. Rotate spring adjustor (4) CCW (viewed
from plug end) until ac tu a tor’s range spring