Cashco PGR-1 User Manual
Page 9
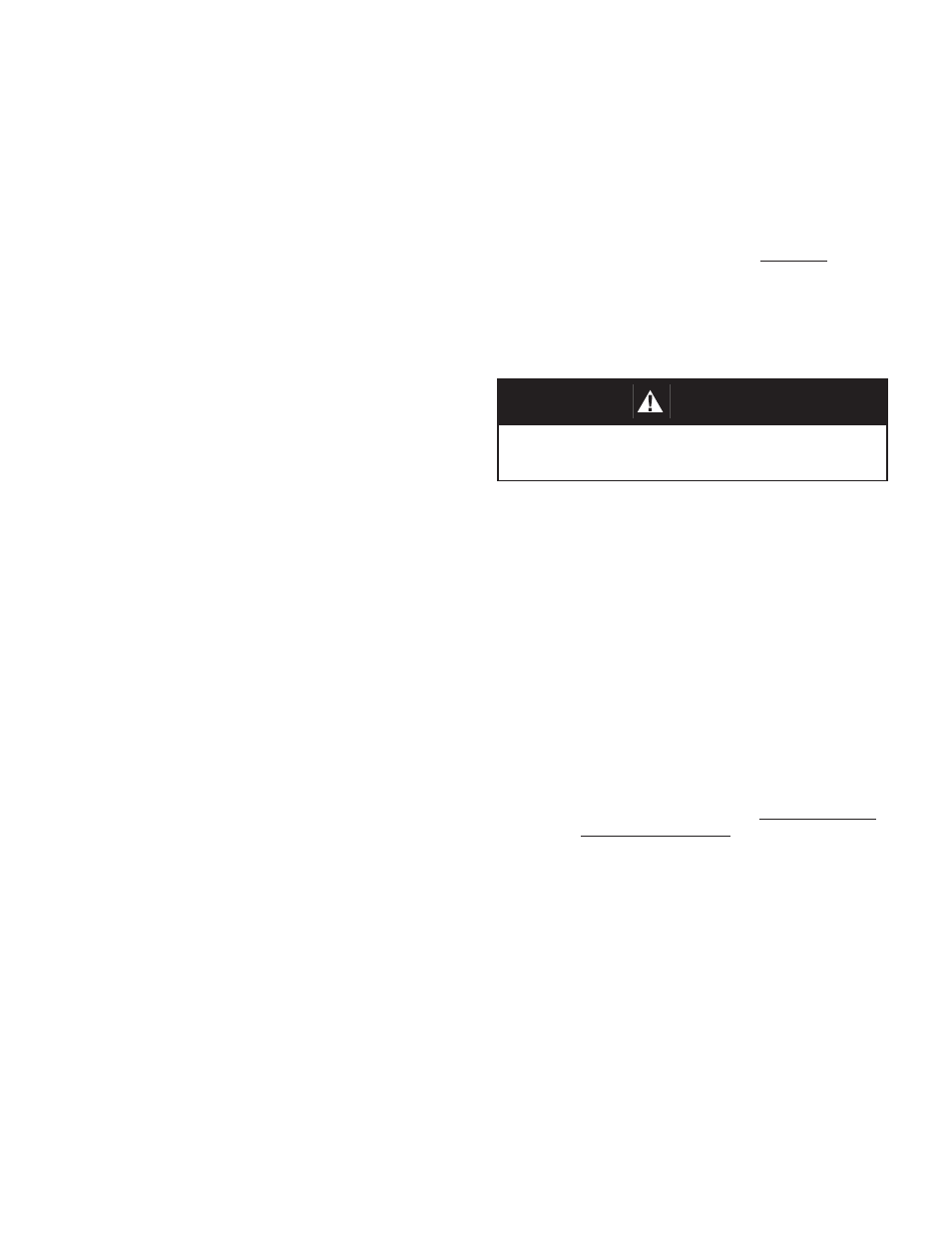
IOM-PGR-1
9
1. Loosen adjusting screw nut (71) one revo-
lution CCW. Relax range spring (75) forces
by rotating adjusting screw (68) CCW until
removed from spring chamber (62).
2. Loosen spring chamber (62) by placing
wrench on “fl ats” and rotating CCW making
sure not to use the fl at where the vent hole
is located.
3. Remove spring chamber (62), spring (75)
and spring button (65).
4. Remove the diaphragm subassembly
con sist ing of the pressure plate nut (70),
lock wash er (69), pres sure plate (63), dia-
phragm (72), push er plate seal (73) and
pusher plate (64).
5. Loosen pusher plate nut (70) and separate
all parts (63, 64, 69, 72 & 73) of the dia-
phragm subassembly.
6. Inspect pressure plate (63) to ensure no
de for ma tion due to over-pressurization. If
de formed, replace.
7. Clean all re us able metal parts according to
owner's pro ce dures.
8. Reassemble diaphragm subassembly
by plac ing pusher plate seal (73) over
thread ed post of pusher plate (64), plac-
ing diaphragm (72) and pressure plate
(63) over the threaded post. Assure the
pressure plate (63) is placed with curved
outer rim down next to the diaphragm (72)
surface. Place a thread sealant compound
on the threads of the push er plate post (64).
Apply 15 in-lbs torque to tighten the nut.
9. Place spring (75) over the pusher plate
nut (70) of the diaphragm subassembly.
10. Place multipurpose, high temperature
grease into de pres sion of spring button
(65) where ad just ing screw (68) makes
contact. Set spring but ton (65) onto range
spring (75); en sure spring button is laying
fl at on top of spring.
11. Rotate the spring chamber (62) CW by
hand into the threaded portion of the body
(61) ensuring not to cross thread. Continue
ro tat ing CW until fi rmly seated against the
upper di a phragm. Tighten to 30-35 ft-lbs
(41-47 N-m) torque value.
12. Reinstall ad just ing screw (68) with nut (71)
into the spring chamber (62).
13. Pressurize with air and spray liquid leak
de tec tor to test around body and spring
cham ber for leakage. En sure that an outlet
pressure is main tained during this leak test
of at least mid-range spring level; i.e. 20-80
psig (1.4-5.5 Barg) range spring, 50 psig
(3.4 Barg) test pres sure min i mum.
TRIM REPLACEMENT -
1. Secure stabilizer body (61) in a vise with
the body cap (66) oriented up and the
spring chamber (62) down wards.
CAUTION
To prevent damage to the body, use soft jaws when secur-
ing body in a vise. Position body so that vise closes over
the inlet and the outlet connections.
2. Loosen and remove body cap.
3. Remove piston spring (67), and piston
(74). Note that the seat and piston guide
are in te gral parts of the body (61) cast ing.
Inspect integral seat and guide for ex ces sive
wear, espe cially at seat sur fac es. Replace if
worn, nicked or de pressed. If integral seat
is nicked, use seat lapping com pound to
remove.
NOTE: Pis ton (74) assembly is a com po si-
tion seat, Cashco, Inc. does not recom mend
at tempt ing to remove the com po si tion seat.
If composition seat is damaged, re place
entire piston assembly.
4. Clean
fl at mating surfaces of body (61) to
body cap (66) shoulder. Be careful not to
scratch either surface.
5. Clean debris from within the body (61) cav-
ity. Parts to be reused should be cleaned
ac cord ing to own er's pro ce dures.
6. Slide the post end of the piston (74), slowly
into the body cavity.
7. Place piston spring (67) over spring hub of
the piston (74).
8. Apply pipe thread sealant to the body cap
(66) threads. Thread body cap into body.
When body cap is fully down against body
at the body cap shoulder, impact the body
cap into the body tight. NOTE: When unit is
put into service and pressurized, these two
parts seal metal-to-metal with no gasket.