Cashco DAP User Manual
Page 4
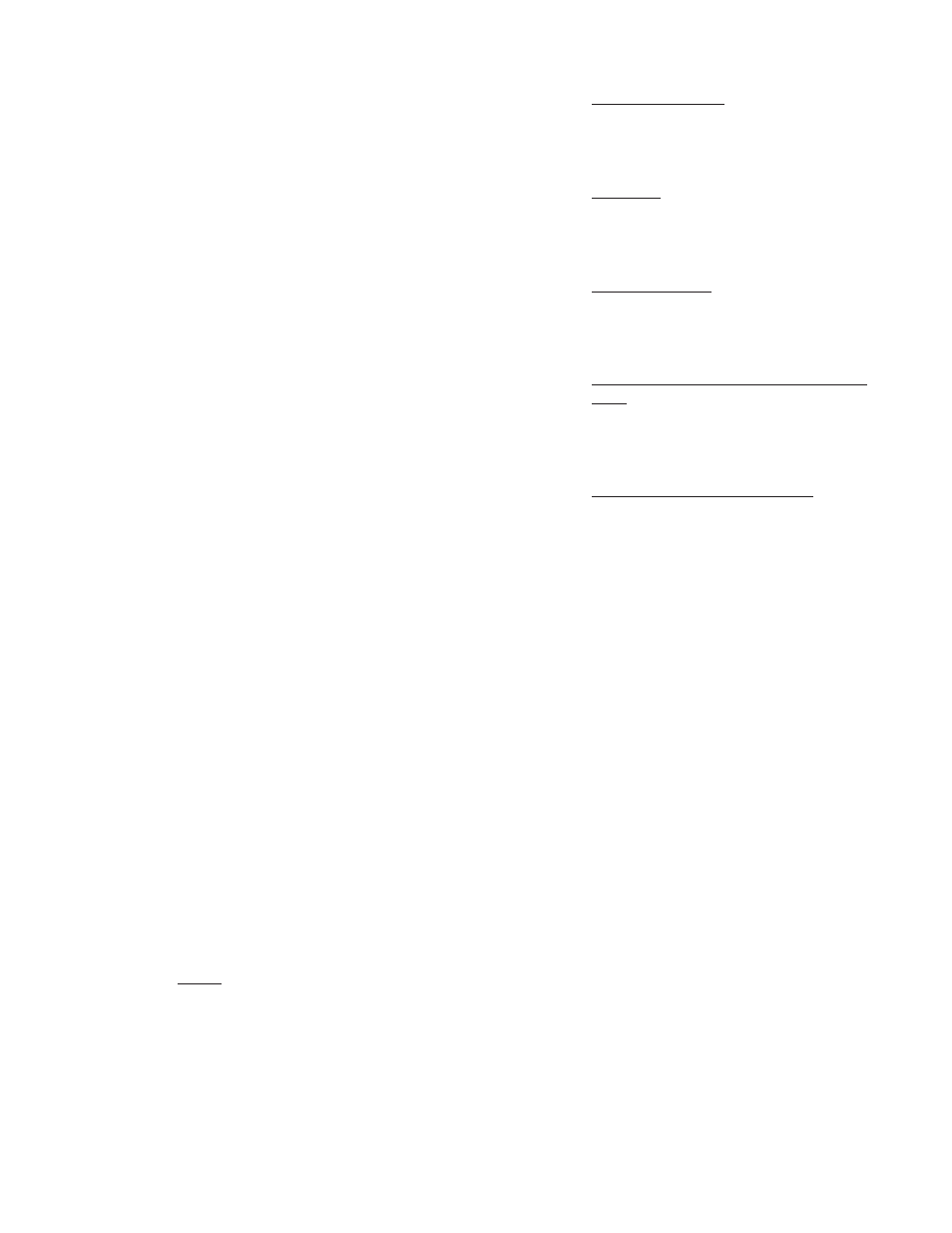
IOM-DAP
4
11. Remove three cage bolts (18) that secure
cage (19) in the body (23).
12. Remove plug (20), cage (19), lower retainer
ring (109), seat ring (21), and stem seal o-ring
(14) from body by pulling stem upwards and
out of body (23) cavity.
13. Remove the plug (20), lower retainer ring
(109), and stem seal (14) from the cage (19).
Inspect for unusual signs of wear or leakage.
Discard stem seal (14). Replace plug (20) or
lower retainer ring (109), if badly worn.
14. Remove seat ring (21) from lower end of
cage (19). Inspect for unusual signs of wear.
Dis card following inspection.
15. Inspect piston (77). Remove the upper retainer
screws (110) securing the up per re tain er ring
(108) to piston. Re move upper retainer ring.
16. Remove upper dynamic actuator seal (78).
Inspect for wear, leakage, damage, etc.; dis-
card when inspection is completed.
17. Remove o-ring cage seal (15). Inspect for
signs of leakage. Discard cage seal (15).
18. Remove o-ring body/cover dome seal (65).
Inspect for signs of leakage. Discard following
inspection.
19. If supplied with "internal" sensing, remove
internal sensing drilled plug (32) using 5/32"
(4mm) Allen wrench.
20. If installed, remove lower piston spring (22)
from body (23) cavity.
21. Remove body (23) from vise. Solvent clean
all removed metal parts to be used at re as-
sem bly.
C. Inspection of Parts:
1. After inspection, dis card the old “soft goods”
parts (i.e. o-rings, seals, gaskets, etc.). These
parts MUST be re placed with fac to ry supplied
new parts.
2. Inspect the metal parts that will be reused. The
parts should be free of surface con tam i nants,
burrs, oxides, and scale. Rework and clean the
parts as necessary. Surface con di tions that
affect the regulator performance are stated
below; replace parts that can not be re worked
or cleaned.
3. QC
Requirements:
a. Regulator plug (20);
1. 16
rms
fi nish on its seating surface
for tight shutoff.
2. No major defects on bottom guide
spin dle.
b. Cage
(19);
1. 16 rms fi nish on cylinder bore. No
“ledges” formed due to wear from
moving dynamic balancing side seal
(27).
c. Cover Dome (25);
1. 16
rms
fi nish on cover dome cylinder
bore. No “ledges” formed due to wear
from moving upper dynamic actuator
seal (78).
d. Lower guide bushing (24) (non-re place -
able):
1. 16
rms
fi nish in bore.
2. Max 0.015 inch (0.38 mm) clearance
be tween plug (20) spindle and lower
guide bushing (24).
e. Internal sensing drilled plug (33);
1. Ensure that bore is minimum 0.125
inch (3.20 mm). Drill out as re-
quired.
4. Staging Material for Reassembly.
a. Inspect and clean parts, as necessary,
from the spare parts kit. (See Ar ti cle
VII.A.4. comments con cern ing cleaning
for ox y gen service.)
b. Lay out all the regulator parts and check
against the bill of material.
D. Main Regulator Reassembly:
1. Place body (23) in a vise.
2. If equipped with "internal" sensing, reinstall
internal sensing drilled plug (32), use com pat-
i ble thread sealant.
3. Insert the lower piston spring (22) into the
body (23), if supplied.
4. Fit o-ring cage seal (15) into body groove.
5. Place o-ring stem seal (14) over threaded end
of plug (20) down to proper position.
6. Lower plug (20) into body (23) cavity, in sert ing
the plug spindle into the lower guide bushing
(24), ensuring that the lower piston spring
(22), if installed, is properly positioned in the
bottom of the body and around the plug.