Notice, Page 5 tg56b, Tools and equipment for testing – C.E. Niehoff & Co. N1607/N1611/N3215B/N2013 Troubleshooting Guides User Manual
Page 5
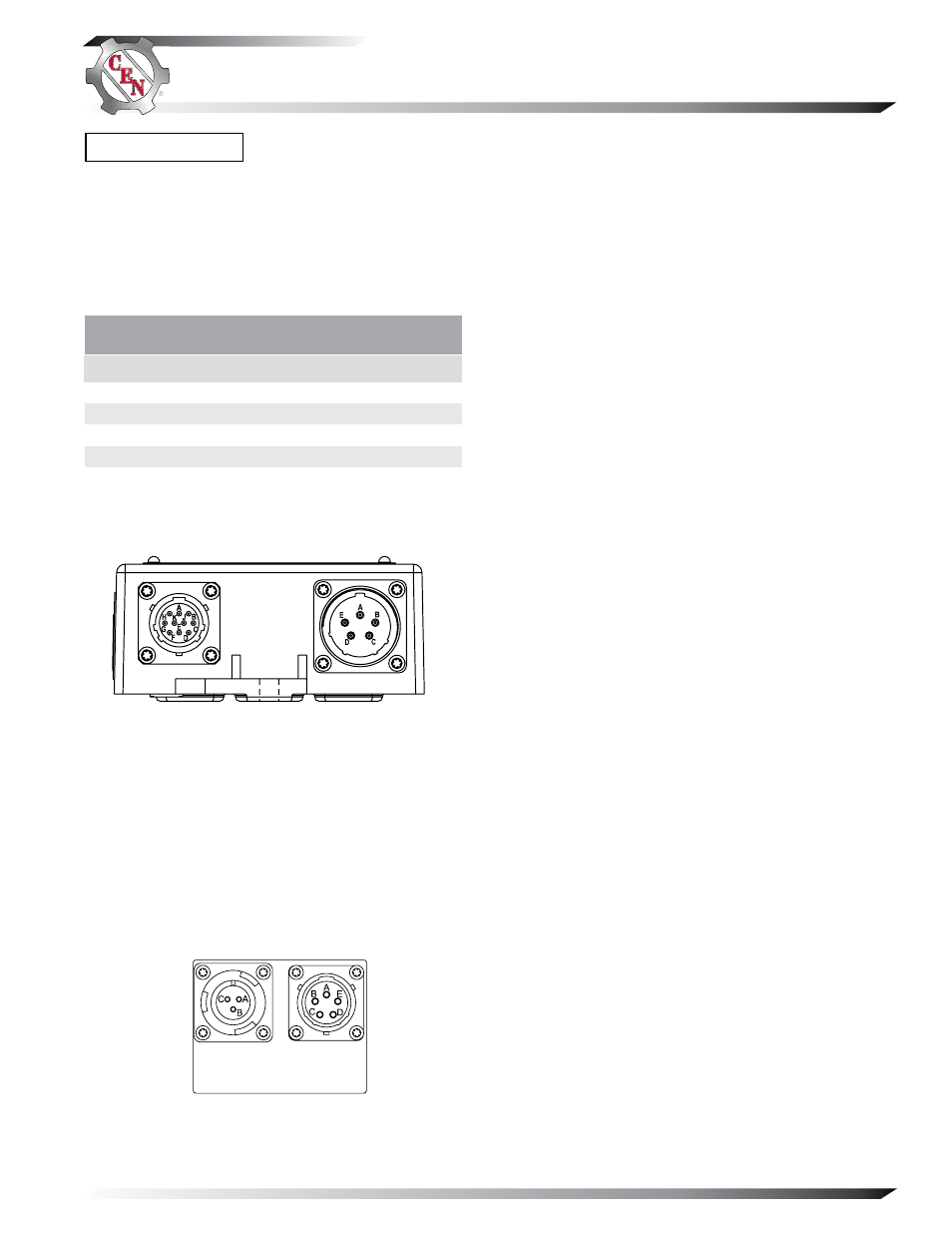
Page 5
TG56B
Section C: Advanced Troubleshooting
Tools and Equipment for Testing
• Digital Multimeter (DMM)
• Ammeter (digital, inductive)
Perform on-vehicle troubleshooting
before attempting on-bench tests
or static tests.
NOTICE
TEST PROCEDURE 1
The following tests will determine whether regulator
and cabling is functioning. If any cabling test fails,
fix cabling, otherwise, regulator is defective.
See Figures 6 and 7.
1. First check to make sure all cabling between
vehicle and regulator is tight.
2. With engine off, at 10-pin connector on regulator
make sure there is battery voltage between pin A
and vehicle chassis ground, then pin H and
vehicle chassis ground. Then check for 10K ohms
± 4K ohms between pins C & D.
3. With engine off, check for continuity between pin
A on 5-pin connector on regulator and pin A on
5-pin connector on alternator.
4. With engine running, check for battery voltage at
pin B on 5-pin connector at regulator.
5. With engine off, check for continuity between pin
C on 5-pin connector at regulator and ground.
Then check for continuity between pin D and B+
stud on alternator.
6. With engine off, check for continuity between pin
E on 5-pin connector on regulator and the pin
that drives the instrument panel regulator
warning light on vehicle.
TEST PROCEDURE 2
The following tests will determine whether alternator is
functioning.
During these tests, engine MUST BE running.
See Figure 7 and wiring diagram on page 2.
1. Disconnect harness at Connector #2 before start-
ing engine. Then, start engine. In harness plug, test
for battery voltage at socket A. If battery voltage
does not exist, vehicle wiring must be checked.
If battery voltage exists, go to Step 2.
2. All of the following tests must prove to be good:
a. Are there less than 2 ohms between socket A
in connector #2 and pin A in connector #1?
b. Does continuity exist between pin C in
connector #1 and alternator ground?
c. Using diode tester, are there 1-2 V between
pins C and D in connector #1?
d. Does continuity exist between pin D and B+
terminal on alternator?
If ALL tests are good, go to Step 3.
If ONE test is bad, alternator is defective.
3. With engine off: Connect one jumper between
socket A in connector #2 and one positive terminal
on battery pack or isolator. Connect one end of
second jumper to pin A in connector #1. Momen-
tarily touch the other end of the jumper to ground.
Spark will occur. Touch steel tool to alternator
shaft at drive end to detect significant magnetism.
If shaft is magnetized, regulator is defective. If
shaft is not magnetized, alternator is defective.
REG.
STATUS
TABLE 2 – N3215B Regulator/Alternator Lights
on Vehicle
System is OK.
Go to Test Procedure 1 on page 5.
Go to Test Procedure 2 on page 5.
Go to Test Procedure 2 on page 5.
Off
On*
Off
On*
ALT.
Off
Off
On
On
* If alternator light comes on within 30 seconds of regulator
light coming on, regulator has registered OVCO. If alternator
light does not come on within 30 seconds, go to Test Procedure 1.
Connector #1
Connector #2
Figure 6 — Regulator Connectors
Figure 7 — Alternator Connectors (ADE)
Connector
#1
Connector
#2
ALTERNATOR
CONNECTOR #1
SOCKET
CONNECTIONS
A F–
B Not used
C B–
D B+
E Phase
ALTERNATOR
CONNECTOR #2
SOCKET
CONNECTIONS
A F+
B Not used
C Phase
REGULATOR CONNECTOR #1
PIN CONNECTIONS
A F–
B Energize
C B–
D B+
E Regulator OVCO Status
REGULATOR CONNECTOR #2
PIN CONNECTIONS
A Battery A +28V Sense
B Unused
C Temperature Sense +
D Temperature Sense –
E PGM
F PGM
G PGM
H Battery B +28V Sense
J Unused
K Unused
}
Do
Not
Use