OSRAM ORBEOS Components User Manual
Page 6
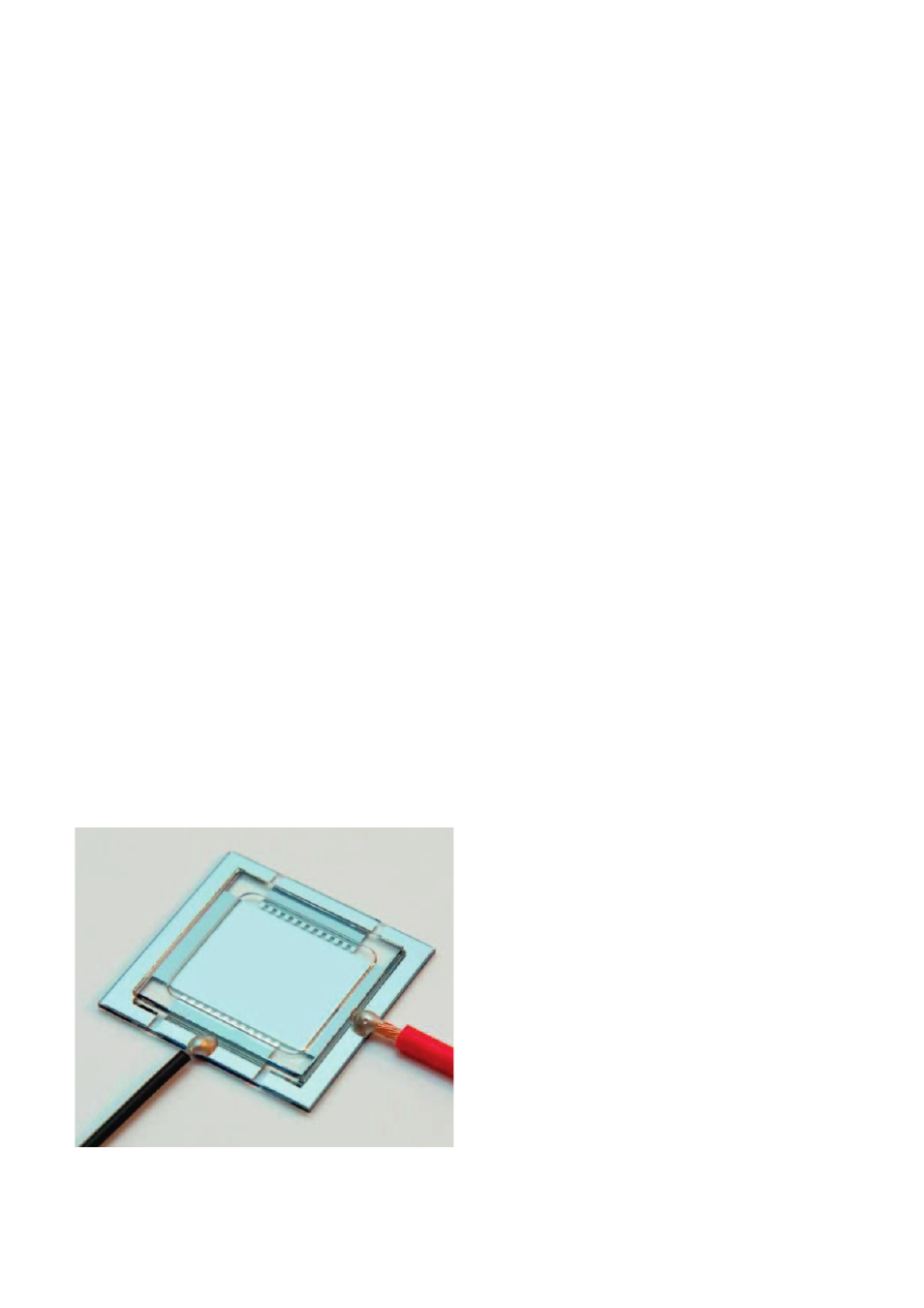
6
OLED INTEGRATION
On the following pages, several techniques for interconnec-
ting OLEDs are described. To interconnect OLED devices,
their contact surfaces have to be free of dust and grease.
If necessary, use isopropyl alcohol (IPA) to carefully wipe the
contact ledges clean.
1.3. Interconnection
1.4. Contacting of OLED tiles via conductive glue
In general, the interconnection should be applied without heat
introduction into the active area of the device. Furthermore,
avoid mechanical stress. Exercise caution in order to avoid
glass chipping and breakage when applying the interconnec-
tion at the substrate edges.
The conductive epoxy used in this application example can
be obtained through R+S Components (conductive epoxy
CW2400, Stock No.: 496-265).
Mix equal amounts of part A and part B thoroughly for at least
2 minutes. The mixed components have to be applied within
a short period. The pot life is only 10 minutes at 24 °C. After-
wards, apply the epoxy to the contact surface and attach
the wire. For better adhesion, fan out the strands of the wire
slightly before attaching it. The wire should have a cross-
sectional area of 0.25 – 0.5 mm². The curing time of the epoxy
is 4 hours at room temperature (24 °C). However, to achieve
maximum conductivity and adhesion, you may expose the ep-
oxy to a temperature of 66 °C – 80 °C for 10 minutes and sub-
sequently allow it to cool. Please note that the heat should be
applied to the contact ledges only.
Fig. 3. Rear side of an OLED device. Two wires are attached to the contact ledges with
conductive epoxy.