9 piping system installation – Glow-worm Xtramax User Manual
Page 16
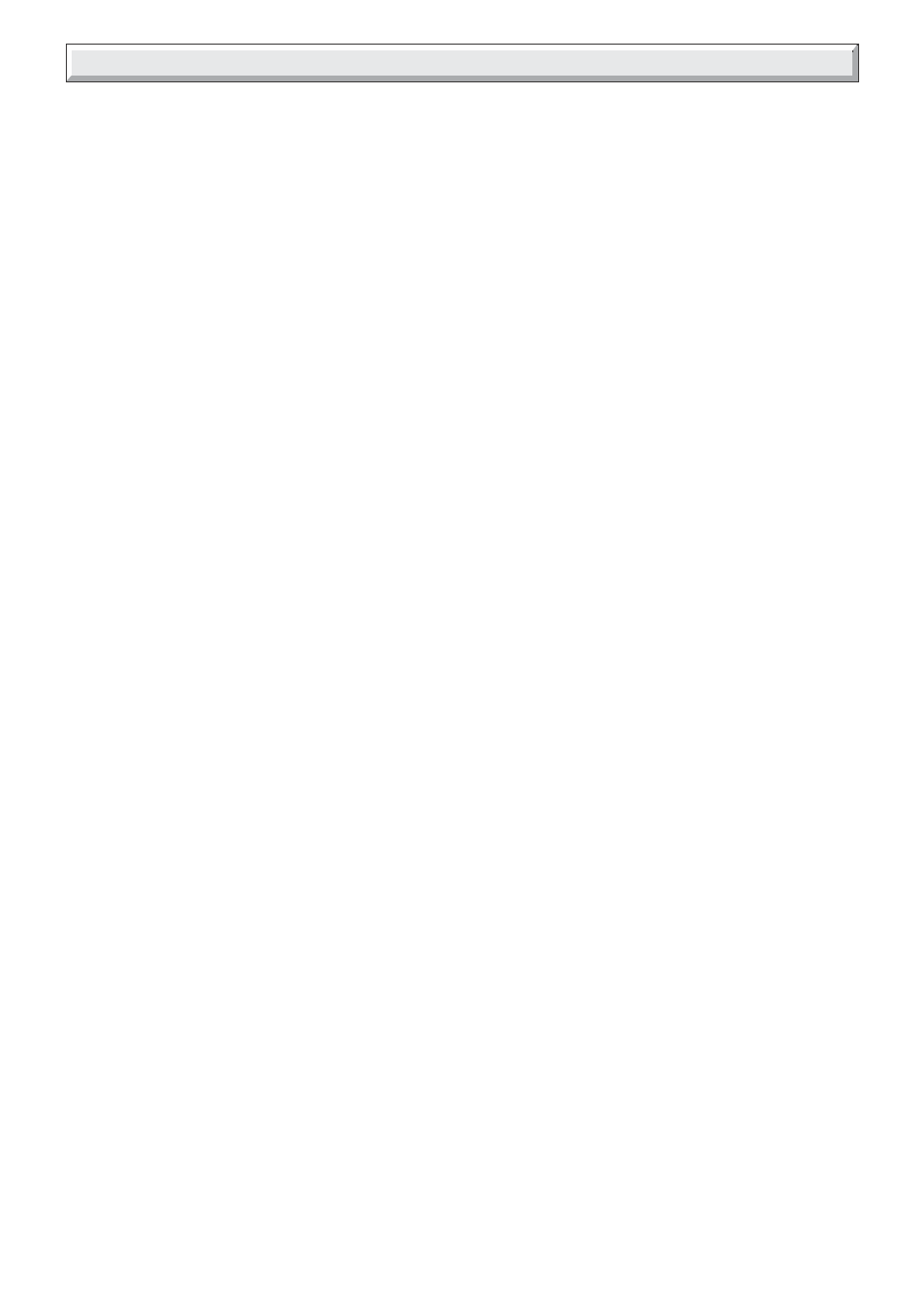
16
4000116705-2
9 Piping System Installation
9.1 Fixing jig, refer to diagram 8.1
• Remove the contents of the fixing jig pack.
• Secure the left and right hand support brackets to the isolating
valve plate with the securing screws (4 off) supplied.
Connect the copper connections supplied, to the fixing jig
fittings.
• Heating system connections - Pipe Ø 22mm
• Hot water system connections - Pipe Ø 15mm
• Gas connection - Pipe Ø 22mm
• Tundish connection - Pipe Ø 22mm
• Safety valve discharge - Diagram 7.1.
9.2 Cutting the flue hole
• Remove the wall template, follow the instructions given on the
wall template.
• Determine the flue application, length and terminal position
before starting.
• Position the wall template, taking due regard of the minimum
clearances for the selected flue application, see diagram 9.1.
Rear hole cutting
• Mark correct position of top rear flue outlet hole from template.
Side hole cutting
• Mark the horizontal centre line for the hole on the rear wall.
Extend the horizontal centre line to the side wall and mark the
vertical centre line of flue hole as shown in diagram 9.1.
Important: When cutting the flue hole and when extending the
flue centre line to a side wall, remember that the flue system
must have a fall of about 35mm per metre of flue DOWNWARD
towards the terminal. There must NEVER be a downward
incline towards the boiler.
• Making allowance for the slope of the flue, cut hole in external
wall, preferably using a core drill. For installations with internal
and external access use a 105 mm diameter core drill.
For installations with internal access only use a 125 mm
diameter core drill.
• Reposition the wall template over hole in wall.
• Mark the position of the holes for the hanging bracket and jig.
• Drill, plug and fix the hanging bracket to the wall using suitable
screws (not supplied).
• Check that the hanging bracket is level.
• Drill plug and fix the fixing jig to the wall.
9.3 Water connection
Connect the system pipework to the copper connections on the
fixing jig observing the correct flow and return format as shown
in diagram 9.2. Do not subject the isolating valves to heat.
9.4 Safety valve discharge
There are two sets of two safety valves fitted to this appliance.
One is located on the jig diagram 8.1, (10) heating safety valve
3 bar. The other is located inside the boiler (diagram 5.1,) (27)
temperature pressure/relief safety valve 7 bar/90°C, and (24)
expansion valve 6 bar.
9.5 Tundish discharge
The internal safety valves, 24 and 27, have been tee’d together
and the discharge pipe run so that it exits at the right hand
bottom of the boiler (diagram 5.1 and 7.1) (D2). The tundish
(supplied) must be used with this outlet within the normal
guidelines and code of practice and must be installed so that it
is visible to the occupants and positioned away from any
electrical devices.
It is necessary, during installation, to connect a 22 mm diameter
metal discharge pipe to a suitable position outside the building.
It is permissible to use copper pipe, see diagram 7.1.
WARNING. The discharge pipe from the tundish should
terminate in a safe place where there is no risk to persons in the
vicinity of the discharge, be of metal and:
a. Be at least one pipe size larger than the nominal outlet size
of the safety device unless its total equivalent hydraulic resistance
exceeds that of a straight pipe 9m long i.e. discharge pipes
between 9m and 18m equivalent resistance length should be at
least larger than the nominal outlet size of the safety device,
between 18m and 27m at least 3 sizes larger, and so on. Bends
must be taken in to account in calculating the flow resistance.
See table and diagram 7.1.
b. Have a vertical section of pipe at least 300mm long, below the
tundish before any elbows or bends in the pipework.
c. Be installed with a continuous fall.
d. Have discharges visible at both the tundish and the final point
of discharge but where this is not possible or practically difficult
there should be clear visibility at one or these of these locations.
Examples of acceptance discharge arrangements are:
1. ideally below a fixed grating and above the waterseal in a
trapped gully.
2. downward discharges at a low level; i.e. up to 100 mm above
external surfaces such as car parks, hard standing, grassed
areas etc. are acceptable providing that where children may
play or otherwise come in to contact with discharges, a wire
cage or similar guard is positioned to prevent contact, whilst
maintaining visibility.
3. discharges at high level; e.g. into metal hopper and metal
down pipe with the end of the discharge pipe clearly visible
(tundish visible or not) or onto a roof capable of withstanding
high temperature discharges of water and 3m from any plastics
guttering systems that would collect such discharges (tundish
visible).
4. where a single pipe serves a number of discharges, such as
in blocks of flats, the number served should be limited to not
more than 6 systems so that any installation can be traced
reasonably easily. The single common discharge pipe should
be least one pipe size larger than the largest individual discharge
pipe to be connected. If unvented hot water storage systems
are installed where discharges from safety devices may not be
apparent i.e. in dwellings occupied by blind, infirm or disabled
people, consideration should be given to the installation of an
electronically operated device to warn when discharge takes
place.
Note: The discharge will consist of scalding water and steam.
Asphalt, roofing felt and non-metallic rainwater goods may be
damaged by such discharges.
9.6 Domestic hot water supply options
The domestic hot water storage temperature inside the boiler
must be set 60° C. It is recommended that the boiler storage
temperature is set by the user to the maximum of 60°C - this will
ensure a more plentiful supply of hot water.
It may be desirable to provide hot water to separate outlets at
different temperatures (for example, to provide a limited
temperature to prevent the risk of scalding). To be able to do
this, a thermostatic mixing valve is supplied with the Xtramax
boiler (factory set to 43°C) and can be fitted during the installation
procedure.