Instructions – Sealey VSE3157 User Manual
Page 2
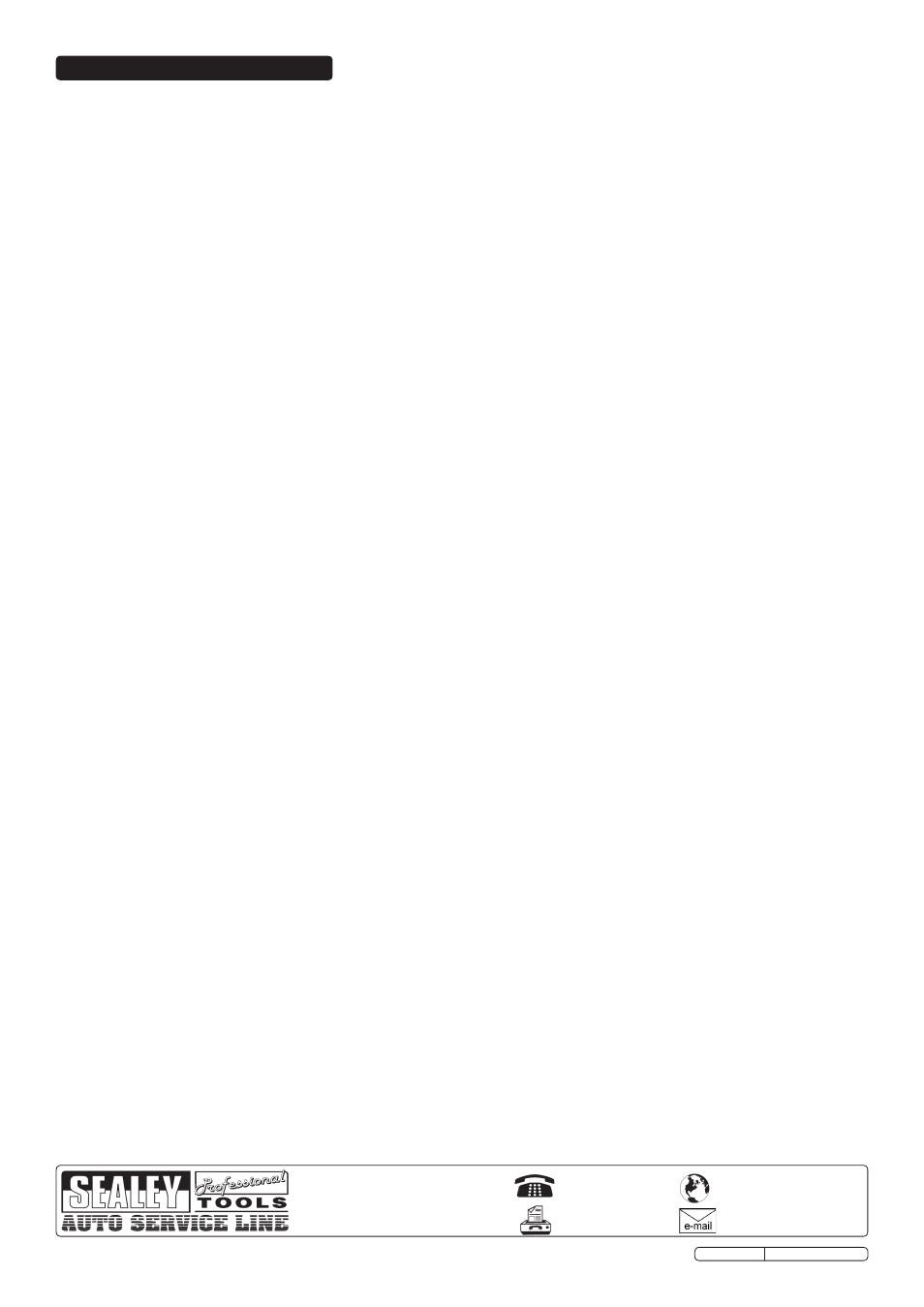
VSE3157 Issue No: 1 - 15/12/10
NOTE: It is our policy to continually improve products and as such we reserve the right to alter data, specifications and component parts without prior notice.
IMPORTANT: No liability is accepted for incorrect use of this product.
WARRANTY: Guarantee is 12 months from purchase date, proof of which will be required for any claim.
INFORMATION: For a copy of our latest catalogue and promotions call us on 01284 757525 and leave your full name and address, including postcode.
01284 757500
www.sealey.co.uk
01284 703534
Web
Sole UK Distributor, Sealey Group,
Kempson Way, Suffolk Business Park
,
Bury St. Edmunds, Suffolk,
IP32 7AR
Original Language Version
3.1.
Overview of compression testing.
When an engine’s performance is down, or if misfiring occurs which cannot be attributed to the ignition or fuel systems, a compression
test can provide diagnostic clues as to the engine’s condition.
Compression should build up quickly in a healthy engine. A very low compression reading on the first stroke, followed by gradually
increasing pressure on successive strokes, indicates worn piston rings. A low compression reading on the first stroke, which does not
build up during successive strokes, indicates leaking valves or a faulty head gasket (a cracked head could also be the cause).
Deposits on the undersides of the valve heads can also cause low compression. If the pressure in any cylinder is considerably lower than
the others, introduce a small quantity of clean oil into that cylinder through the glow plug hole, and repeat the test. If the addition of oil
temporarily improves the compression pressure, this indicates that bore or piston wear is responsible for the pressure loss. If there is no
improvement, it suggests that the leakage is around the valves, or a faulty head gasket. A low reading from two adjacent cylinders
suggests a faulty head gasket between the two cylinders. The presence of coolant in the engine oil will confirm this.
If the compression is unusually high, the combustion chambers are probably coated with carbon deposits. If this is the case, the cylinder
head should be removed and de-carbonised.
As a rough guide, engines having a compression pressure in excess of 100psi (6.9 bar), should not exceed a compression loss of more
than 10psi (0.69 bar). On older engines with lower compression pressure, loss should not exceed 0.35 bar (5psi).
3.2.
Compression Testing.
3.2.1.
Check the engine oil is at the correct level.
3.2.2.
Remove all of the glow plugs from the engine.
3.2.3.
Select the applicable adaptor from one of the accompanying kits and screw it into the first glow plug port, ensuring there is a good seal
with the O-ring (if fitted). Connect the coupling on the pressure gauge hose to the adaptor, ensuring it locks into place.
3.2.4.
Turn over the engine using the starter motor and observe the gauge, looking for a steady increase in the reading (see 3.1) and note the
maximum reading obtained. Refer to the vehicle/engine manufacturer’s workshop manual for compression results data.
3.2.5.
Depress the Re-set Valve (situated under the gauge) to release the pressure. The Re-set Valve allows the test to be repeated if required
without disconnecting the tester from the glow plug port.
WARNING! Always release pressure via the Re-set Valve BEFORE disconnecting the Tester.
3.2.6.
Disconnect the compression tester from the adaptor and remove the adaptor from the glow plug port. Install them into the next cylinder’s
glow plug port and repeat the tests. Continue the tests for all of the remaining cylinders in turn.
NOTE: A variation in compression readings between cylinders is often a better indication of engine problems than the individual values of
compression.
3.3.
TDC Indicator Tool.
3.3.1.
Remove the glow plug from cylinder number 1. It may also be necessary to remove all glow plugs to facilitate manual turning over of the
engine.
3.3.2.
Select the applicable adaptor from one of the accompanying kits and screw it into the glow plug port of cylinder number 1. Ensure that
there is a good seal with the O-ring (if fitted). Connect the coupling on the TDC finder to the adaptor, ensuring it locks into place.
3.3.3.
Position the indicator in a vertical position, in a suitable viewable location, using the magnetic hook if needed.
3.3.4.
Turn the engine over manually, using a spanner or socket on the crankshaft pulley, in the direction of engine rotation and watch for the
float to rise in the tube. As the piston rises on the compression stroke, the float will rise to the top of the tube and stay there, when the
piston goes past TDC and compression is lost, the float will suddenly sink. Note position and temporarily make suitable marks to indicate
TDC, or compare with existing timing marks.
3.3.5.
Turn the engine over a further 1¾ turns and the float should start to rise again as the piston rises on the compression stroke. Continue
to slowly turn the crankshaft towards TDC (watching the timing marks) - note the exact point when the float drops. Alter the timing mark if
required.
3.3.6.
Repeat the procedure, turning the engine over a further 2 turns to re-check for accuracy.
3.3.7.
Disconnect the TDC tool from the adaptor and remove the adaptor from the glow plug port.
3. INSTRUCTIONS