Fig. 2, Environmental protection, 6 . trouble shooting – Sealey 1250CX User Manual
Page 2: Maintenance
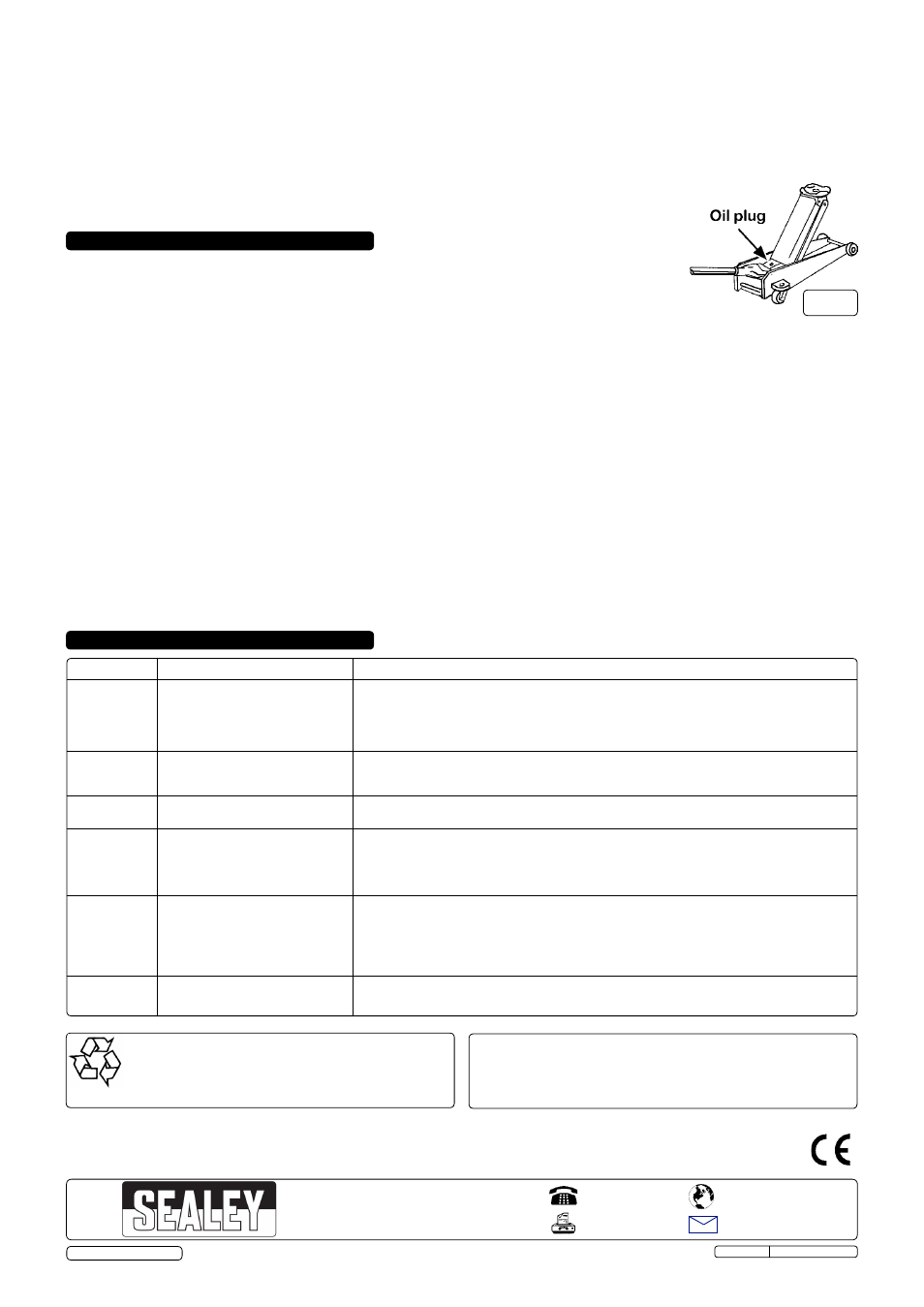
4.3. Jacking
Weight Distribution
Up to 80% of the lifted load is carried by the front jack wheels, placing exceptional stress on the point of contact with the supporting
floor. For this reason use on a hard level concrete surface only.
4.3.1. Turn the handle clockwise to close the valve and commence pumping the handle up and down using maximum strokes until the vehicle
reaches the working height.
Note: If the jack becomes overloaded, a safety excess pressure valve will open, and stop the vehicle from lifting further.
4.4. lowering
4.4.1. The lowering speed is controlled by the amount you turn the handle. Lower carefully, avoiding sudden release.
WARNING! Ensure that there are no persons or obstacles beneath the vehicle, or in the path of its descent.
6 . TROuBle shOOTING
PROBLEM
POSSIBLE CAUSE
REMEDY
Jack will not lift
the load
Jack does not lift
high enough or
feels “spongy”
Jack lifts poorly
Jack lifts but will
not hold load
Jack will not lower
completely
Jack does not
lower at all
1) Be sure to use jack with adequate capacity.
2) Top up oil level.
3) Check and close release valve.
4) Open release valve and air vent (if fitted) and pump the handle a few times. Close valve and re-try.
5) Clean and replace oil.
6) Replace packing.
1) Fill or remove excess oil.
2) Return jack to local service agent.
3) Open release valve and air vent (if fitted) and pump the handle a few times. Close valve and re-try.
4) Check and close release valve.
1) Replace packing and/or clean valves.
2) Replace oil.
3) Open release valve and air vent (if fitted) and pump the handle a few times. Close valve and re-try.
1) Check and close release valve.
2) Lower jack, close release valve. Place foot on front wheel and pull up lifting arm to its full height by hand.
Open the release valve to lower arm.
3) Open release valve and air vent (if fitted) and pump the handle a few times. Close valve and re-try.
4) Replace packing or contact local service agent.
5) Replace packing.
1) Oil all external moving parts.
2) Replace rod or contact local service agent.
3) Replace damaged parts or contact local service agent.
4) Open release valve and air vent (if fitted) and pump the handle a few times. Close valve and re-try.
5) Check and fully open release valve.
6) Replace spring or contact local service agent.
1) Check and fully open release valve.
1) Overloaded
2) Oil level low
3) Release valve not correctly closed
4) Air in system
5) Piston rod not functioning
6) Packing worn or defective
1) Oil level too high or too low
2) Worn seals
3) Air in system
4) Release valve not closed
1) Pump packing or valves malfunctioning
2) Oil is dirty
3) Air in the system
1) Release valve partially open
2) Dirt on valve seats
3) Air in system
4) Faulty seals
5) Packing worn or defective
1) Unit requires lubrication
2) Piston rod bent or damaged
3) Jack frame/link system distorted due
to overloading/poor positioning
4) Air in system
5) Release valve partially open
6) Jack spring damaged
1) Release valve still closed
ImpORTANT! Only fully qualified personnel should attempt maintenance or repair.
5.1. When the jack is not in use, the ram and the handle socket should be in their lowest positions to minimise
corrosion. Remove the handle to deactivate the jack.
5.2. Keep the jack clean and lubricate all moving parts with a good quality oil on a regular basis.
5.3. To check the hydraulic oil level, fully lower the jack and remove filler plug (fig.2). The correct oil level should be approximately
5mm below the filler opening. If oil level is low, fill as required. Pump unloaded jack 5 or 6 times to expel air and then refit plug.
Note: Use a good quality jack oil, such as SEALEY HYDRAULIC JACK OIL.
WARNING! DO NOT use brake fluid, or any fluid other than hydraulic jack fluid as this may cause serious damage to the jack and will
invalidate the warranty!
5.4. Before each use, check for broken, cracked, bent, or loose parts, or any visible damage to welds, ram, pump, saddle, lifting arm, frame
and all parts including nuts, bolts, pins and other fasteners. If any suspect item is found, remove jack from service and take necessary
action to remedy the problem.
DO NOT use the jack if it is believed to have been subjected to abnormal load or shock. Inspect and take appropriate action.
5.5. Every three months remove the locking rings on the caster wheels and lubricate the ball bearings with grease.
5.6. After a year of extensive use, the oil should be replaced in order to extend the life of your equipment. To drain the oil, remove the filler
cap and valve. Make sure that no dirt is allowed to enter the hydraulic system. See 5.3. for refill instructions.
5.7. Periodically check the pump piston and piston rod for signs of corrosion. Clean exposed areas with a clean oiled cloth.
ImpORTANT: NO RESpONSIBILITY IS ACCEpTED FOR INCORRECT USE OF THE mACHINE.
Hydraulic products are only repaired by local service agents. We have service/repair agents in all parts of the UK.
DO NOT RETURN jACkS TO US. Please telephone us on 01284 757500 to obtain the address and telephone number of your local agent.
If the jack is under guarantee please contact your dealer.
De-commissioning
If the jack becomes completely unserviceable, draw off the oil into an approved container and dispose of the jack and the oil according to local
regulations.
5. MAINTeNANce
fig. 2
NOTE: It is our policy to continually improve products and as such we reserve the right to alter data, specifications and component parts without prior notice.
IMPORTANT: No liability is accepted for incorrect use of this product.
WARRANTy: Guarantee is 12 months from purchase date, proof of which will be required for any claim.
INfORMATION: For a copy of our latest catalogue and promotions call us on 01284 757525 and leave your full name and address, including postcode.
01284 757500
01284 703534
sole uk Distributor, sealey Group,
Kempson Way, Suffolk Business Park
,
Bury St. Edmunds, Suffolk,
IP32 7AR
www.sealey.co.uk
W e b
Original Language Version
1250CX.V2 Issue: 1 - 31/10/13
© Jack Sealey Ltd
environmental Protection.
Recycle unwanted materials instead of disposing of them as
waste. All tools, accessories and packaging should be sorted,
taken to a recycle centre and disposed of in a manner which
is compatible with the environment.
Parts support is available for this product. To obtain a parts listing and/or
diagram, please log on to: www.sealey.co.uk, or phone: 01284 757500.