3 mechatrolink-ii function specifications, Rotation – Yaskawa Sigma-5 Large Capacity Users Manual: Design and Maintenance-Rotary Motors-Mechatrolink-II Communication Reference User Manual
Page 31
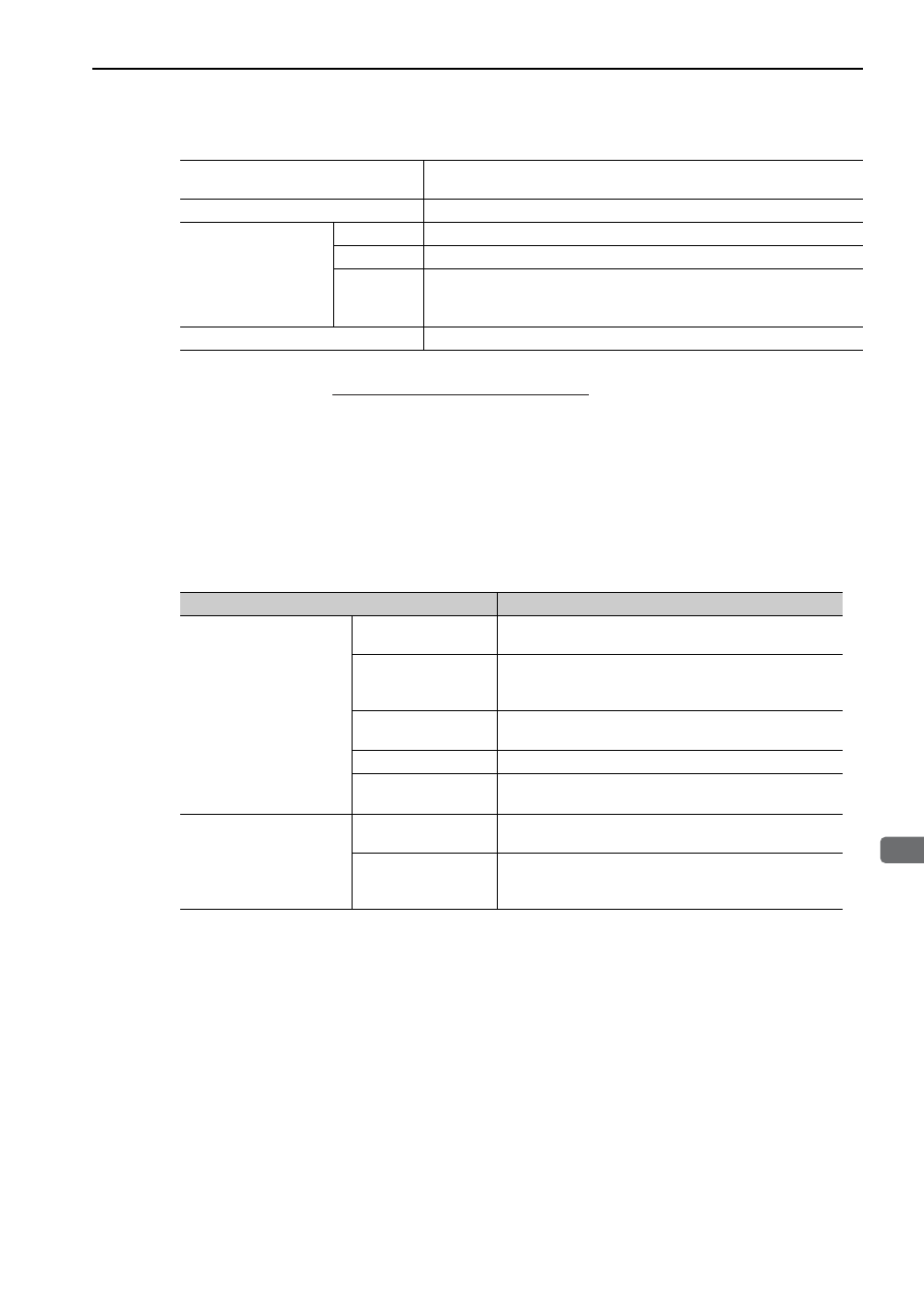
1.4 Ratings and Specifications
1-9
1
Outline
∗1. Speed regulation by load regulation is defined as follows:
∗2. Refer to 4.2.10 Velocity Control (VEL CTRL: 3CH) of
Σ
-V Series User’s Manual MECHATROLINK-II Commands
(No.: SIEP S800000 54) for details on the soft start function.
∗3. Set Pn001 to n.
2 if you do not use the dynamic brake.
∗4. Refer to 3.9 Selecting and Connecting a Dynamic Brake Unit for details on dynamic brake units.
∗5. Refer to 3.8 Selecting and Connecting a Regenerative Resistor Unit for details on regenerative resistor unit.
∗6. Implement risk assessment and confirm that the safety requirements of the machine have been met.
1.4.3 MECHATROLINK-II Function Specifications
The following table shows the specifications of MECHATROLINK-II.
Protective Function
Overcurrent, overvoltage, insufficient voltage, overload, regeneration error,
and so on.
Utility Function
Gain adjustment, alarm history, JOG operation, origin search, and so on.
Safety Function
Input
/HWBB1, /HWBB2: Baseblock signal for power module
Output
EDM1: Monitoring status of internal safety circuit (fixed output)
Standards
*6
(Application
pending)
EN 954 Category 3, IEC 61508 SIL2
Optional Module
Fully-closed module, safety module
(cont’d)
Speed regulation
=
No-load motor speed
Total load motor speed
Rated motor speed
× 100%
-
Rotation
Function
Specifications
MECHATROLINK-II
Communication
Communication Pro-
tocol
MECHATROLINK-II
Station Address
41H to 5FH (Max. number of stations: 30)
Can be selected by the combination of the rotary switch (S2)
and the DIP switch (S3).
Baud Rate
10 Mbps, 4 Mbps
Can be selected by the DIP switch (S3).
Transmission Cycle
250
μs, 0.5 ms to 4.0 ms (Multiples of 0.5 ms)
Number of Transmis-
sion Bytes
17 bytes per station or 32 bytes per station
Can be selected by the DIP switch (S3).
Reference Method
Control Method
Position, speed, or torque control with MECHATROLINK-
II communication
Reference Input
MECHATROLINK-I,MECHATROLINK-II commands
(sequence, motion, data setting/reference, monitoring, or
adjustment)