Faults and alarms – Yaskawa AC Drive - A1000 Motion Control Custom User Manual
Page 17
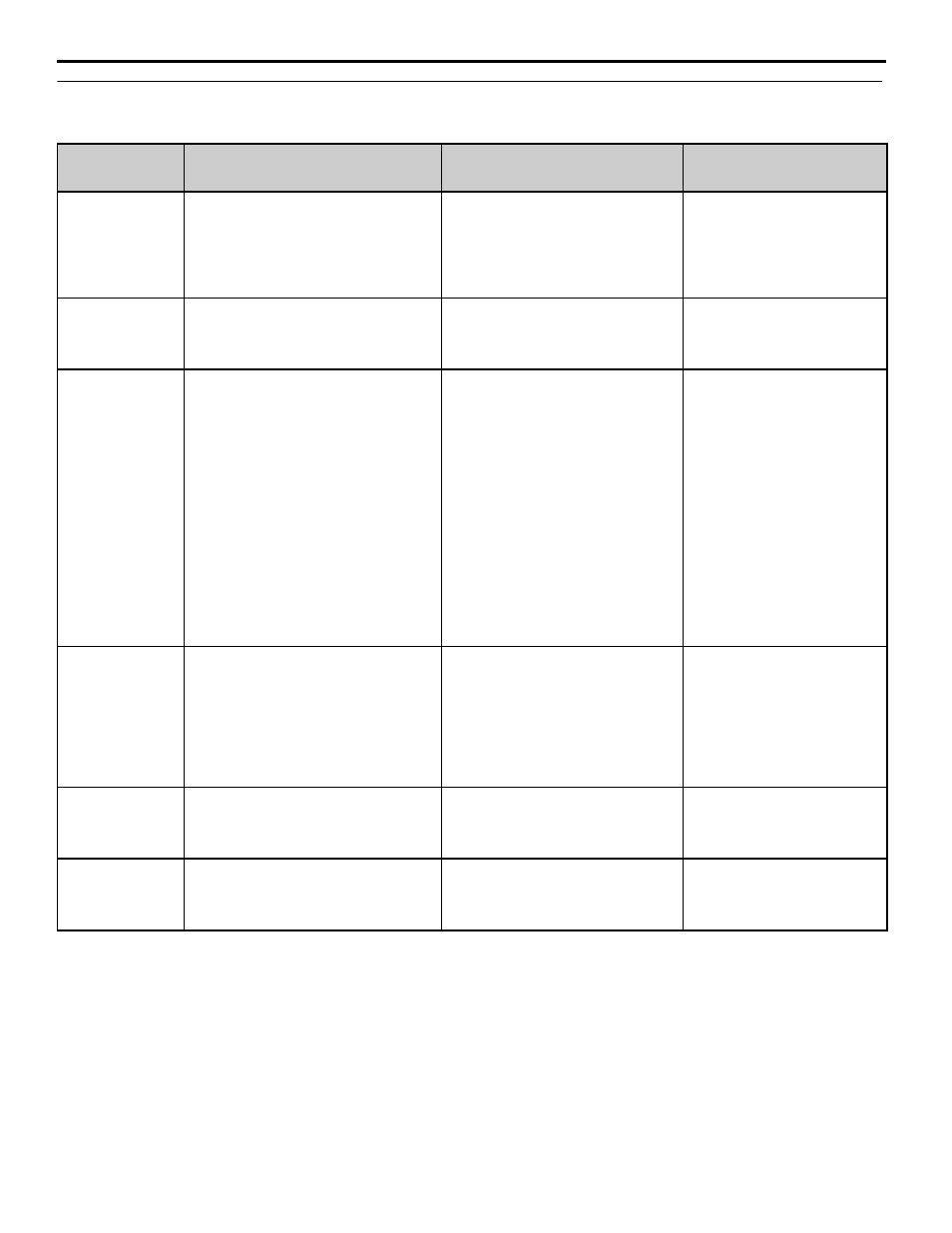
4 Related Parameters and Functions
YASKAWA TM.A1000SW.117 Motion Control Custom Software Supplement
17
Faults and Alarms
Table 13 Faults
Fault Indication
LCD
Description
<1> An OPE03 error can be caused by many other conditions as well. These conditions are listed in Section 6 of the A1000 Technical Manual
(SIEPC71061641).
Cause
Countermeasures
Multi-Function
Input Selection Error
OPE03
Terminal
Multi-function Input Selection Error.
• Motion control is enables (P1-01>0)
and 3-wire control is enabled (One of the
H1 parameters is set to 0-3-Wire Control
• Motion control is enabled
(P1-01 > 0) and Motor 2 Select is
programmed into an H1 parameter
• Disable the motion control by
setting P1-01 = 0, or reprogram
the H1 parameter that is set to 0
• Disable the motion control by
setting P1-01 = 0, or reprogram
the H1 parameter that is set to 16
Option Card
Selection Error
OPE05
Sequence Select
Option Card Selection Error
Distance Select is programmed for
Option PCB Fref (P1-02 = 2) and no
communications option is installed at
connector CN5-A
Re-program parameter P1-02, or
install communications option
board
Motion Control Setup
Error
OPE12
Motion Ctrl Stup
Motion Control Setup Error
• Absolute Encoder is selected
(P3-01 = 2) AND motion type is not
Linear Absolute (P1-01 >=2)
• Absolute Encoder is selected
(P3-01 = 2) AND a DI-A3 option board
is not installed
• The numerator (P3-03) is set more than
100 times greater than the denominator
(P3-04)
• Encoder type is set to Serial Abs Ch1
and encoder rotation is set to CW.
(P3-01 = 3 and F1-05 = 1)
• Motion Control is enabled
(P1-01>0) and either PG1 Signal Select
(F1-21) or PG2 Signal Select (F1-37) is
set to only A Phase Detection (0)
• Adjust motion type or encoder
type
• Adjust motion type or encoder
type or install a DI-A3 option
board.
• Adjust the numerator and the
denominator
• Adjust parameter F1-05 back to
zero and change PG Ch. 1
feedback wiring
• Disable Motion Control or set
PG1 and PG2 to A and B Phase
Detection
Second Encoder Fault
2ENFL
2nd Enc. Fault
There is a problem with the encoder
connected to the PG-X3 card in slot CN5-B
or with the absolute encoder connected to
the DI-A3.
• Incremental encoder connected to
PG-X3 card in slot CN5-B has opposite
rotation from the motor encoder
• Absolute encoder has either rolled over
and no longer contains valid position
data, or has opposite rotation from the
motor encoder
• Switch the polarity of the
incremental encoder connected to
the 2
nd
channel, by swapping
terminals A+ and A- on the PG-
X3 card in slot CN5-B
• Mechanically reset the absolute
encoder, or force the encoder to
count in the opposite direction
Position Overflow
Fault
POSOF
Position Ovrflow
The internal register that tracks position has
exceeded its limits, DURING a motion-
control move.
The distance from home (or home +
home offset) has exceeded 10
9
encoder
counts.
Re-home and verify position of
moving equipment.
Serial Encoder Fault
SENCF
Ser Enc Fault
Absolute Incremental Encoder fault.
The drive did NOT receive valid
data/control signals from the absolute
incremental encoder within 35 seconds
after power up or home command.
Check encoder and wiring, Check
that an analog input and output are
programmed and wired properly
for a absolute incremental encoder.