Nonlinear axis error compensation – HEIDENHAIN ND 231 B v.1 User Manual
Page 25
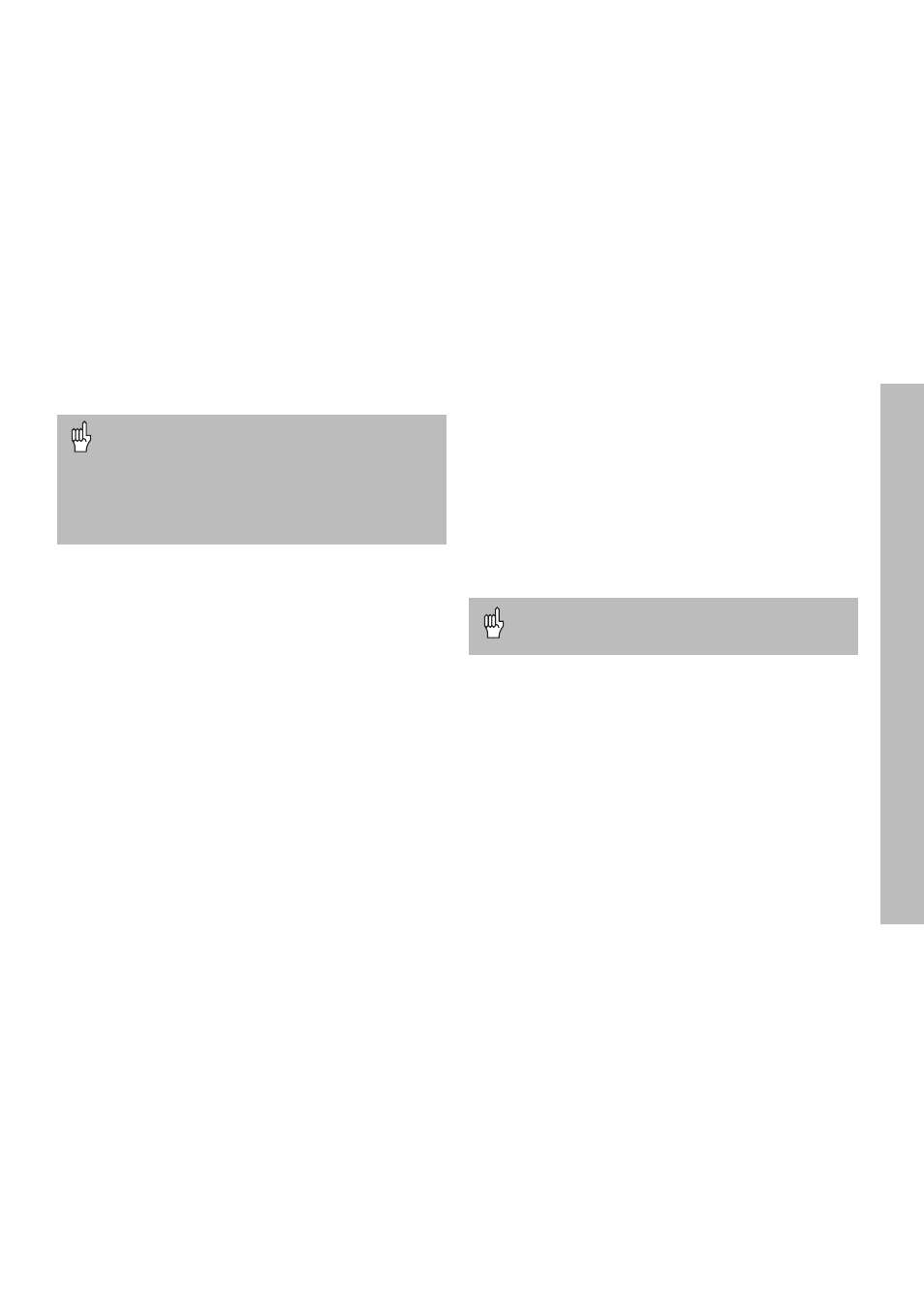
25
The letter “R.1” or “R.2” at the left of the display indicates that
the displayed position value is given with respect to the refer-
ence mark. If “R.1” or “R.2” blinks, you must traverse the
reference mark.
Entries in the compensation value table
•
Axis to be error-compensated: X1 or X2
•
Error-causing axis: X1 or X2
•
Datum:
Here you enter the point at which the compensation is to
begin. This point indicates the absolute distance to the
reference point.
Do not change the datum after measuring the axis
error and before entering the axis error into the
compensation table.
•
Spacing of the compensation points:
The spacing of the compensation points is expressed as:
Spacing = 2
x
[µm].
Enter the value of the exponent
x into the compensation
value table.
Minimum input value:
6 (= 0.064 mm)
Maximum input value:
20 (= 1048.576 mm)
Example: 900 mm traverse with 15 compensation points
==> 60.000 mm spacing between points.
Nearest power of two: 2
16
= 65.536 mm (see
“Table for determining the point spacing”)
Input value in the table: 16
•
Compensation value:
You enter the measured compensation value (in milli-
meters) for the displayed compensation point. Compensa-
tion point 0 always has the value 0 and cannot be changed.
Nonlinear Axis Error Compensation
If you want to use the nonlinear axis error
compensation feature, you must:
•
Activate the feature with operating parameter
40 (see “Operating Parameters”),
•
Traverse the reference marks after switching
on the display unit,
•
enter a compensation value table
Nonlinear Axis Error Compensation
Your machine may have a nonlinear axis error due to factors
such as axis sag or leadscrew errors. Such deviations are
usually measured with a comparator measuring system (such
as the HEIDENHAIN VM 101).
An axis can be error-compensated only with respect to an
error-causing axis. A compensation table with a total of up to
64 compensation values can be entered for every axis.
You select the compensation table through P00 CODE and by
entering the code number 10 52 96 (see Operating
Parameters).
Ascertaining the compensation values
To ascertain the compensation values (e.g. with a VM 101)
you must select the compensation table and then press the
“–” key to select the REF display.