TE Technology TC-48-20 User Manual
Page 21
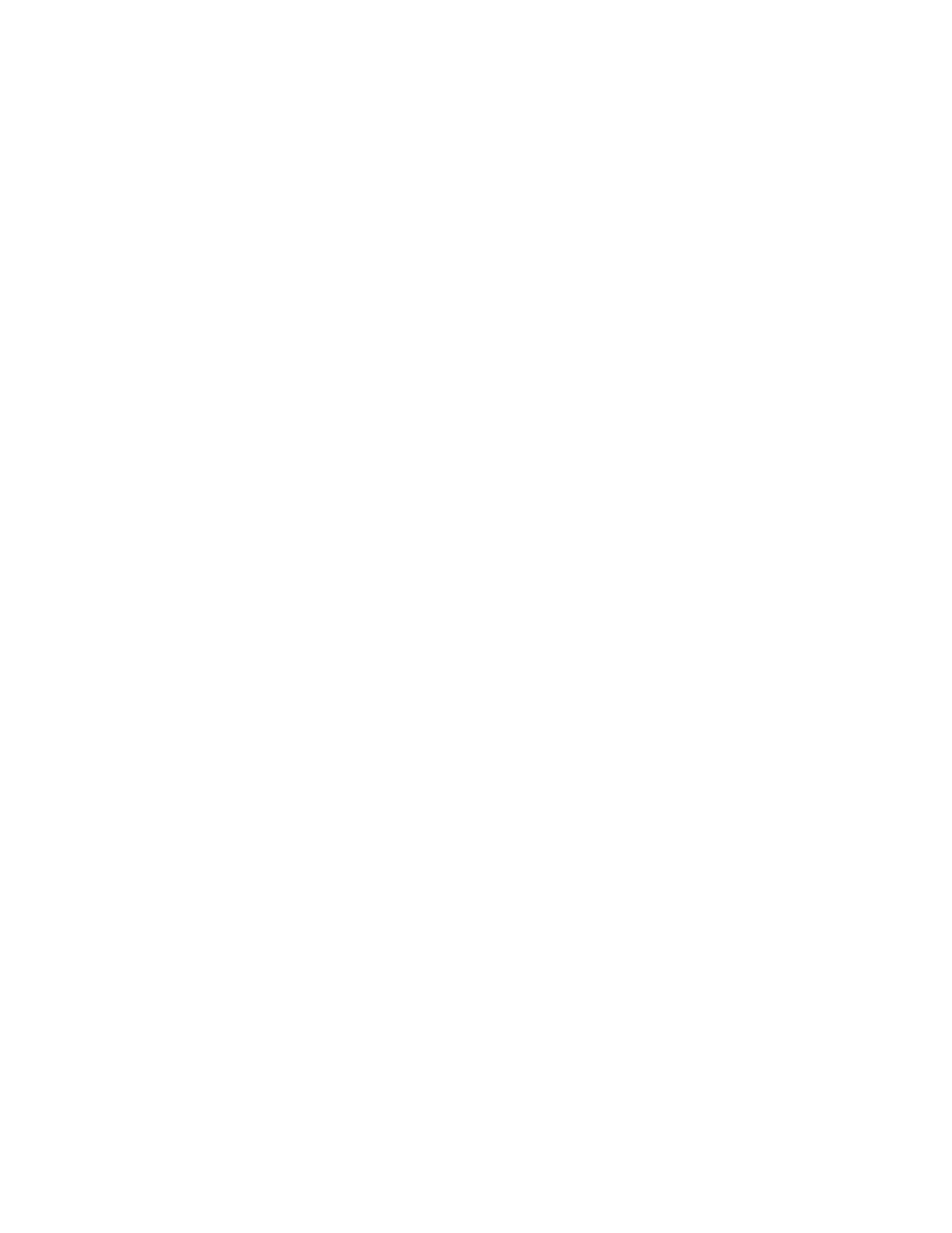
21
• Press the “MENU” button momentarily to select the parameter to be changed.
• Press the Up/Down arrow keys to adjust the parameter value.
• If there is more than one value for any given parameter the MENU key will scroll from the first value to
the next value and then on to the next parameter.
• Holding the Up/Down arrow keys will cause the value to increment faster.
• The display will return to the primary screen after eight seconds if no keys are depressed.
2.3.1 SET TEMPERATURE
Values: ‐20.0 °C to +199.0 °C, or as defined by the limits set by CONTROL RANGE
Default value = 25.0 °C
Description: SET TEMPERATURE is the control temperature that the controller tries to maintain. Note that
controller set point should not be set outside the range suitable for the temperature sensor. Consult TE
Technology for customization if you need a thermistor that can provide a different control range. Also, be
sure that the set point is also appropriate to the TE device.
2.3.2 PROPORTIONAL BW
Values: 0.5 °C to 100.0 °C
Default value = 5.0 °C
Description: The proportional bandwidth is the temperature span over which the power is proportioned
from 100% to 0% power, centered about the temperature set point. That is, the controller output
decreases to 50% power as it reaches the set point and to 0% as it reaches the end of the bandwidth
range below the set point (when in the cooling mode).
For example, suppose the controller is being operated in the cooling mode, the set point is 10.0 °C, and
the bandwidth is set to 5 °C. The controller power starts to proportionally decrease as the sensor
temperature cools below 12.5°C. The power will be reduced to 50% when the sensor is at 10.0 °C. Finally,
the power will be at 0% when the sensor is at 7.5°C. (Of course, this example presumes that the
INTEGRAL GAIN and DERIVATIVE GAIN are set to 0 and that the cooler would have enough capacity to cool
to 7.5 °C.)
If the bandwidth is set too narrow, the temperature will oscillate around the set point. If the bandwidth is
too wide, the controller will be slow to respond or may never reach set point.
2.3.3 INTEGRAL GAIN
Values: 0.00 to 10.00 (repeats per minute)
Default value = 1.00
Description: This corrects for any offset between the set temperature and the sense temperature by
averaging the offset with respect to time. This essentially shifts the proportional bandwidth.
For example, suppose the set temperature is 10.0 °C, the bandwidth is set to 5 °C, and the controller
settled to a constant 11.2 °C (corresponding to 74% power). If the integral control is then set to 1 repeat
per minute, the controller will increase the power to 98% in 1 minute, providing extra cooling to move the
temperature closer to the set temperature. In this example, after one minute of operation the controller
calculated that the difference between the desired set temperature and the actual temperature was +1.2
°C. With a bandwidth of 5 °C, the controller uses the INTEGRAL GAIN to add an additional 24% output per
minute (100% output / 5 °C * 1.2 °C = 24 %). This additional 24% output was added to the existing 74%
output to yield 98% output. The integral portion of the output is continuously recalculated at the rate
specified by the integral gain setting. The INTEGRAL GAIN always adds or subtracts from the present
output power. Of course, the maximum output is limited to 100% and the minimum is limited to 0%.
If the integral control is set too high, the temperature will oscillate. If integral control is set too low, it will
take a long time for the temperature to settle to steady state.