0 calibration parameter description, Calibration parameter description – TE Technology TC-36-25-RS232 User Manual
Page 26
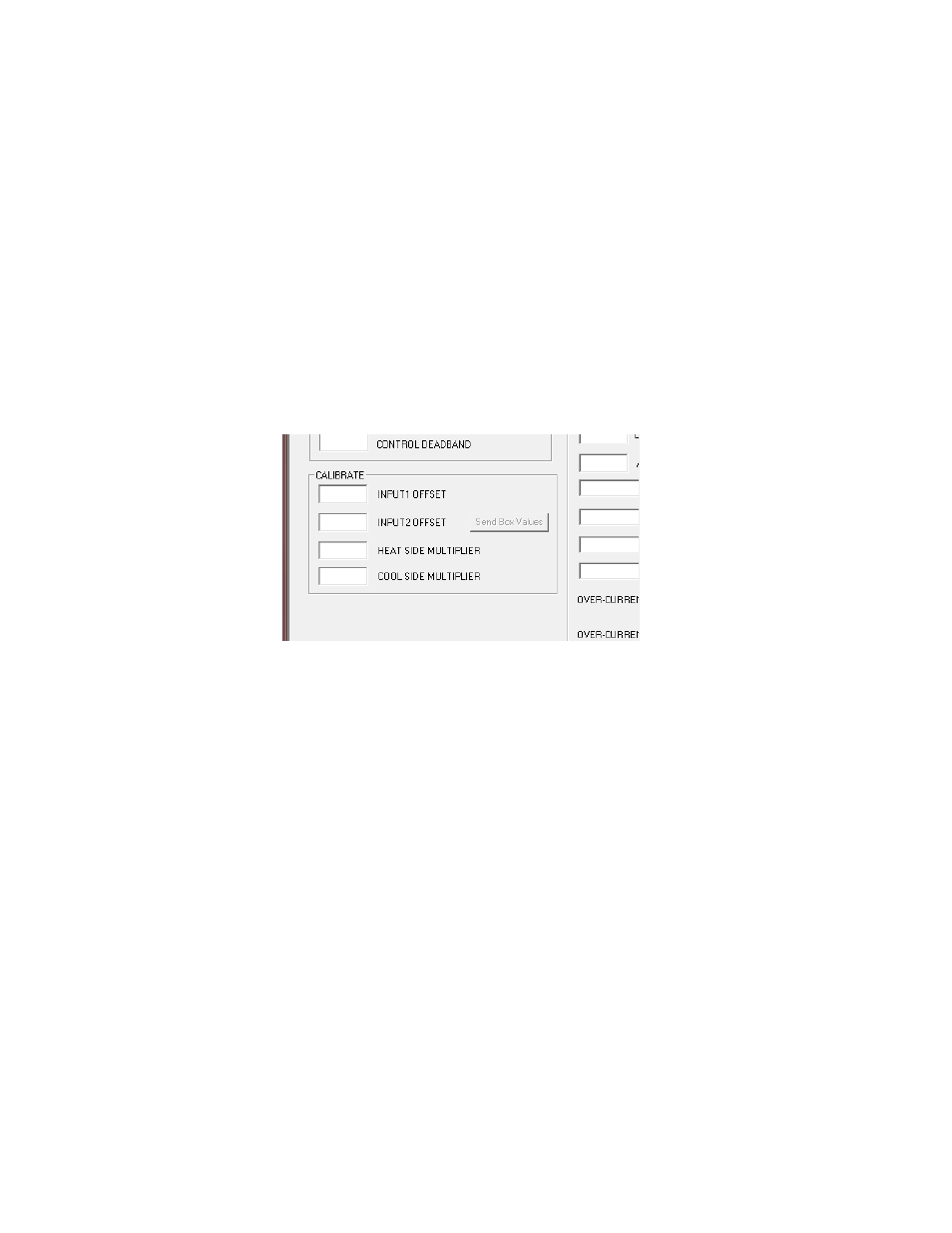
3.5
DERIVATIVE GAIN:
The acceptable values that may be entered are (0.00 to 10) cycles per minute.
The derivative gain senses the rate of change of the temperature and allows the controller to anticipate the power
needed to compensate for rapid changes in system loading. This term is generally used only on very sluggish
systems or where very quick response is necessary. It works in a way similar to the integral gain, but acts upon
change in error signal and not the actual error signal.
3.6
CONTROL DEADBAND:
The controller can be set to turn on and off by either rising or falling temperatures where no heating or cooling
takes place. This band is expressed in degrees, and the acceptable values that may be entered are 0.1 to 100. This
setting is only utilized when CONTROL TYPE is set to DEADBAND CONTROL.
4.0 Calibration Parameter Description
4.1
The CALIBRATE section provides additional variables that can be used to fine tune your system’s operation. You
may want to try controlling with the initial settings prior to entering values in this section.
4.2
INPUT 1 OFFSET is a manual method of compensating for a temperature difference between the sensor 1
temperature and actual control temperature.
4.3
INPUT 2 OFFSET is a manual method of compensating for a temperature difference between the sensor 2
temperature and actual temperature.
4.4
HEAT SIDE MULTIPLIER is a 0.00 to 2.00 numerical multiplier that compensates for the non-symmetrical response
of the thermoelectric cooler between the heat and cool modes. When the controller is in heating mode it takes
the computed PID output power value and multiplies it by this multiplier to derive the actual output level. Setting
the value to 0 makes the controller a “cool only” controller.
4.5
COLD SIDE MULTIPLIER is a 0.00 to 2.00 numerical multiplier that compensates for the non-symmetrical response
of the thermoelectric cooler between the heat and cool modes. When the controller is in cooling mode it takes
the computed PID output power value and multiplies it by this multiplier to derive the actual output level. Setting
the value to 0 makes the controller a “heat only” controller.
4.6
If you have entered values in the CALIBRATE section and they are desired settings, click the SEND BOX VALUES
button to download these constants to the controller.
26