TE Technology TC-36-25-RS232 User Manual
Page 12
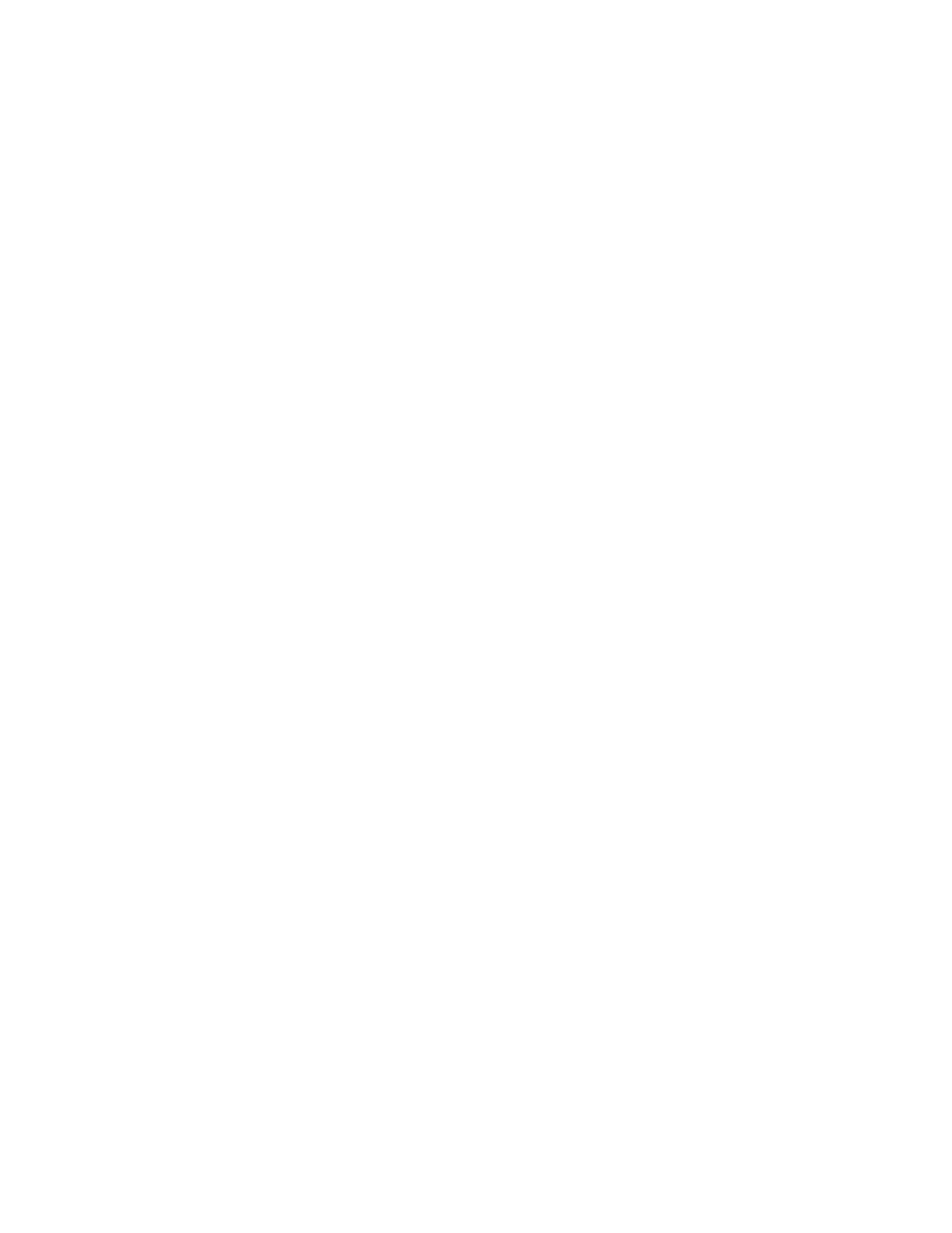
Multiple Control Configurations
Depending on the input voltage required for the TE device, the TC-36-25 RS232 can be used with either one or two
separate power supplies. When using one power supply, an input supply voltage ranging anywhere from (12 to 36) VDC is
required to power both the controller and the TE device. The output voltage during the “ON” time is approximately equal
to the input voltage.
When using two power supplies, one power supply, ranging anywhere from (12 to 36) VDC, can be used to power the
controller itself; and a second power supply, ranging anywhere from (0 to 36) VDC, can be connected to the H-bridge of
the controller. This second power supply allows the controller to control TE devices that must operate at a voltage less
than 12 V. The self-contained H-bridge output transistors can deliver load currents from (0.1 to 25) A. (NOTE: consult
appropriate installation instructions for power supply and heat sinking requirements for high current operation).
The controller tuning structure allows designation of a variety of control features:
1) The Computer Set Value provides for manual control of the output from 0% to ±100% of load power. This
allows a remote device or computer to designate what output % the controller should deliver.
2) Proportional bandwidth (P) in degrees, Integral reset (I) in repeats per minute, and the Derivative rate (D) in
minutes may be configured for P, PI, PD, or PID control.
3) Deadband control (on/off) with an adjustable hysteresis may also be selected. However, this control mode is
not generally recommended with TE devices.
4) Differential temperature control is provided when two input sensing thermistors are used. The unit will control
the differential between Input 2 (reference temperature) and Input 1 (actual system temperature).
A control temperature range of –20 °C to +100 °C is standard when using TE Technology’s supplied thermistor sensor
probe (MP-3193) for the primary sense temperature. Other temperature ranges are available with optional thermistors.
The set point of the controller can be changed in a variety of ways by using either a computer, a remote set-temperature
potentiometer, a (0 to 5) VDC signal, a (0 to 20) mA current loop, or the MP-2986 Display and Keypad accessory. A
secondary thermistor can also be used for differential control (or it could be used for alarm condition sensing). All
temperatures may be consistently displayed in °C or °F.
Two types of control output modes may be selected. This determines the direction of the current flow through the
thermoelectric when heating is desired. This current flow may be from Wire Point WP1+ to Wire Point WP2-.
Alternatively, this current flow may be reversed from WP2+ to WP1- as selected in the configuration menu.
Several alarm settings may be selected, some of which provide an output current of 25 mA for alarm signaling. The
settings can be selected for no alarm function, tracking alarm, and fixed-value alarm. Alarm temperature values can be
entered in the setup menu using the supplied software. The computer-controlled selection is available for additional
embedded controller input/output options. The alarm setup menu also provides for selection of an alarm latching
condition. The alarm sensor may be either the control temperature sensor or a secondary thermistor sensor.
The various alarms have the ability to determine the status of the output power to the thermoelectric cooler or auxiliary
heater. The main output power may be maintained during an alarm condition or shut down, depending on the user’s
setting.
12