Calibration – Sensoray 518 User Manual
Page 49
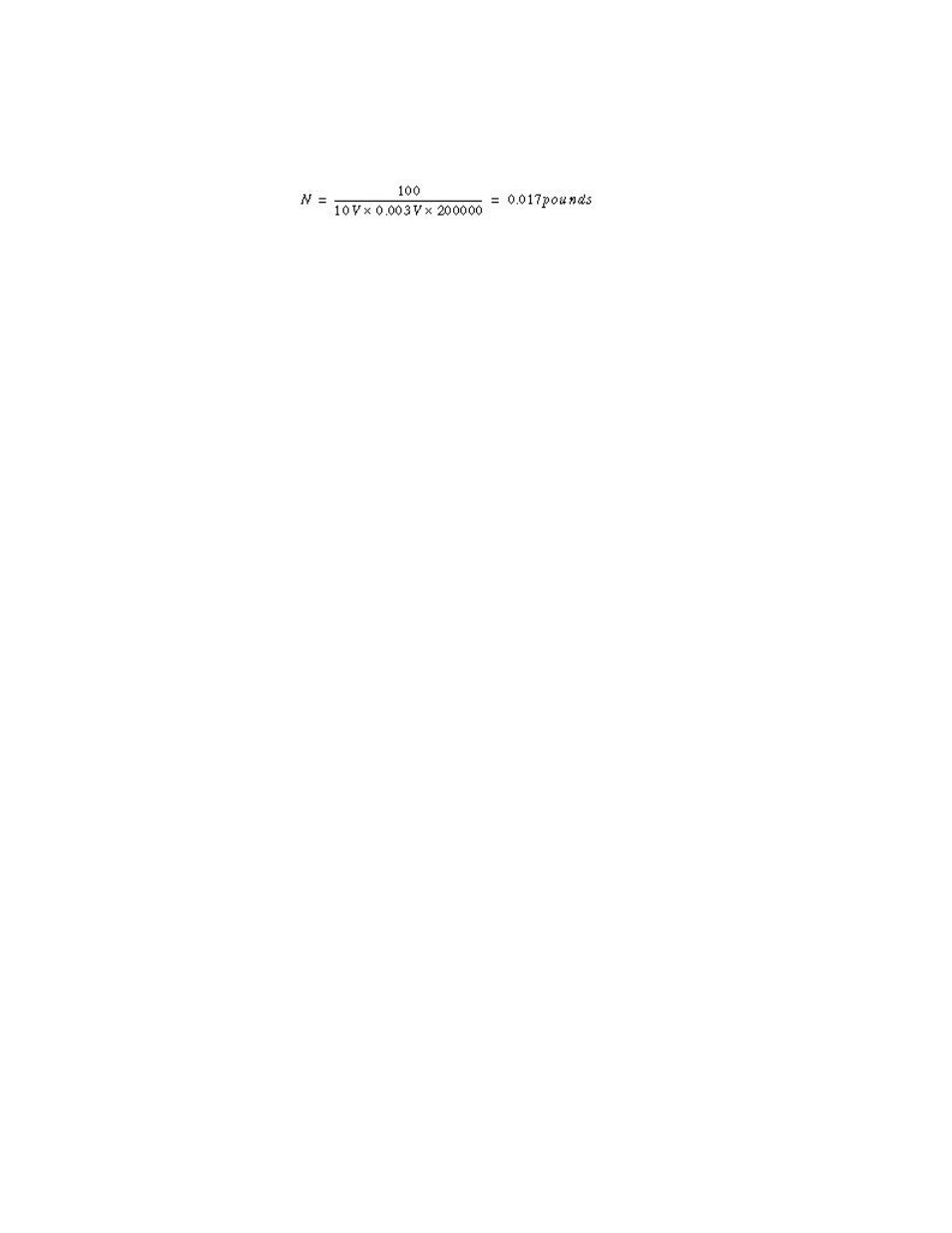
48
As an example, suppose a gage is rated at 3 mV/V at 100 PSI full scale. The 518 coprocessor
would be able to resolve a load to:
In order to successfully measure a gage with the coprocessor:
1. The gage input impedance as viewed by the coprocessor excitation source must not be
less than 120 ohms. If the input impedance is less than 120 ohms, a resistor must be
wired in series with the gage input terminals to reduce excitation circuit loading.
2. The gage output voltage must fall between -500 mV and +500 mV under all load
conditions (including any offset caused by bridge imbalance). If the gage output
exceeds these range limits, the maximum output can be reduced by decreasing the
gage excitation: connect a resistor in series with the gage input terminals.
If a resistor is wired in series with the gage excitation terminals, it should be a metal film type
with low temperature coefficient. Keep in mind that a series resistor changes the excitation
voltage as seen by the gage. The above equations for gage resolution still apply, but the
excitation value must be adjusted to compensate for the series resistance.
Calibration
Strain gages are calibrated using a two-level calibration hierarchy. At the top level the gage zero
and span values are established. This calibration function is performed once at start-up time to
define gage characteristics and at periodic intervals to compensate for the drift of gage
parameters with time, mechanical changes of the load cell, and temperature. At the second level,
the load is tared prior to each load measurement to compensate for empty container weight.
Zero and Span Adjustment
Default gage parameters are assumed by the 518 when a channel sensor is declared to be a strain
gage. These default values are very unlikely to be correct for the installed gage. As a result, the
gage zero and span must be explicitly defined for proper gage operation. Also, gage parameters
change over time, drift with temperature, and are influenced by mechanical hysteresis effects
within the load cell. To compensate for these variations we recommend that the zero and span be
recalibrated occasionally during operation, even after the initial calibration. Note that the
coprocessor does not ‘remember’ the gage calibration when it is reset or powered down, so an
initial gage calibration is always required.
The coprocessor permits gage calibration by either of two methods: load simulation, or
calibration data transfer. The load simulation procedure requires either physical or simulated
loading of the gage, while the calibration transfer method needs only data transfer between host
processor and coprocessor.