5slow speed adjustment, Slow speed adjustment, 5 slow speed adjustment – Research Concepts RC2000C User Manual
Page 25
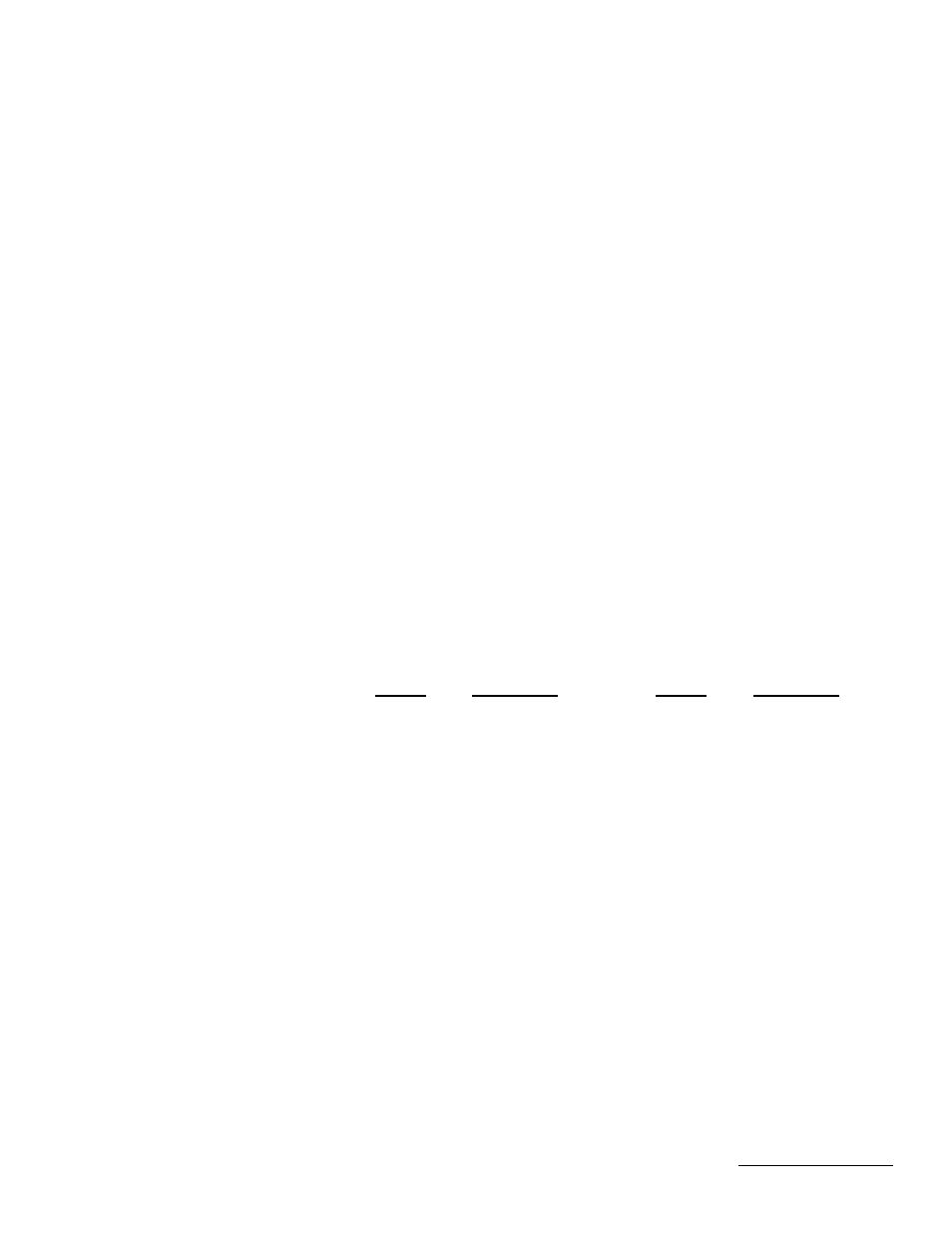
RC2000C Az/El Tracking Antenna Controller
Chapter 3
Installation/Setup
17
Research Concepts, Inc. • 5420 Martindale Road • Shawnee, Kansas • 66218-9680 • USA
www.researchconcepts.com
3.5
Slow Speed Adjustment
The Adapti-Drive slow speed control system allows the user to specify a desired slow speed. When the
antenna is moving at slow speed the controller will vary the voltage to the drive to maintain the actual
antenna slow speed at the value specified by the user. Other slow speed drive systems in use reduce
the voltage to the drive to a constant value whenever slow speed movements occur. This results in
poor speed regulation as the load on the motor varies or as friction in the drive system changes with
temperature.
For the RC2000C the user sets the slow speed for each axis independently by entering a slow speed
code via the appropriate CONFIG mode prompt. This section outlines the procedure for selecting the
appropriate slow speed code. When the system memory is reset the azimuth and elevation slow speed
codes are initialized to 254 (maximum). If the speed code for a given axis is set to 254, the slow speed
system for that axis is disabled, and full voltage is applied to the axis whenever slow speed is selected.
If the speed code is set to 254 and slow speed is selected, the slow banner and a voltage code will be
displayed, but the drive will move at fast speed and the voltage code will not change.
When slow speed movement occurs, the RC2000C determines the speed at which the actuator is
moving by measuring the rate at which position feedback pulses are received for the axis which is being
moved. The controller adjusts the voltage to the drive by using a Pulse Width Modulation (PWM)
scheme, which essentially turns the 36-volt drive voltage off and on very rapidly. Whenever the
antenna is manually jogged at slow speed (in MANUAL or SETUP mode) an indication of the voltage
delivered to the drive is displayed to the right of the 'SLOW' banner. This quantity, referred to as a
'voltage code', varies from 1 to 24. The drive voltage associated with a voltage code of 1 is the
minimum voltage that can be delivered to the actuators. A voltage code of 24 is associated with the
maximum voltage that can be delivered to the drive.
To determine the slow speed code that is appropriate for the azimuth axis, use the following procedure.
For 36-volt DC linear actuators, slow speed codes of 140 to 180 are common.
1. In MANUAL mode jog the antenna in azimuth at FAST speed for exactly 10 seconds and record the
number of counts that occur. Make sure that the antenna does not reach a limit during the move.
1. Use the following table to determine an initial setting for the speed code.
counts
speed code
counts
speed code
60
80
300
165
70
90
350
170
80
100
415
175
95
110
525
180
120
120
715
185
145
130
1100
190
170
140
1325
195
200
150
1450
200
250
160
3. Go to CONFIG mode and use the SCROLL keys to bring up the Azim Slow Speed item. Key in the
new speed code followed by the ENTER key.
4. Go to MANUAL mode, toggle the speed to SLOW, and jog the antenna in azimuth. Continue
jogging the antenna until the voltage code displayed to the right of the SLOW banner settles to a
steady state range of values. This may take 5 to 10 seconds. If a limit is reached, jog the antenna
in the opposite direction. After the voltage code settles to a steady state range of values, check the
rate of movement to make sure that it is slow enough to be useful but not so slow that the motor
stalls or moves in a jerky fashion. If the movement is not satisfactory increase or decrease the
speed code by 3 to 5 counts. Increasing the speed code results in a faster rate of slow speed
movement. Repeat steps 3 and 4 until satisfactory slow speed movement is attained.
A similar procedure is used to adjust the elevation slow speed.