Microsonic dbk+5/3CDD/M18 E+S User Manual
Microsonic Sensors
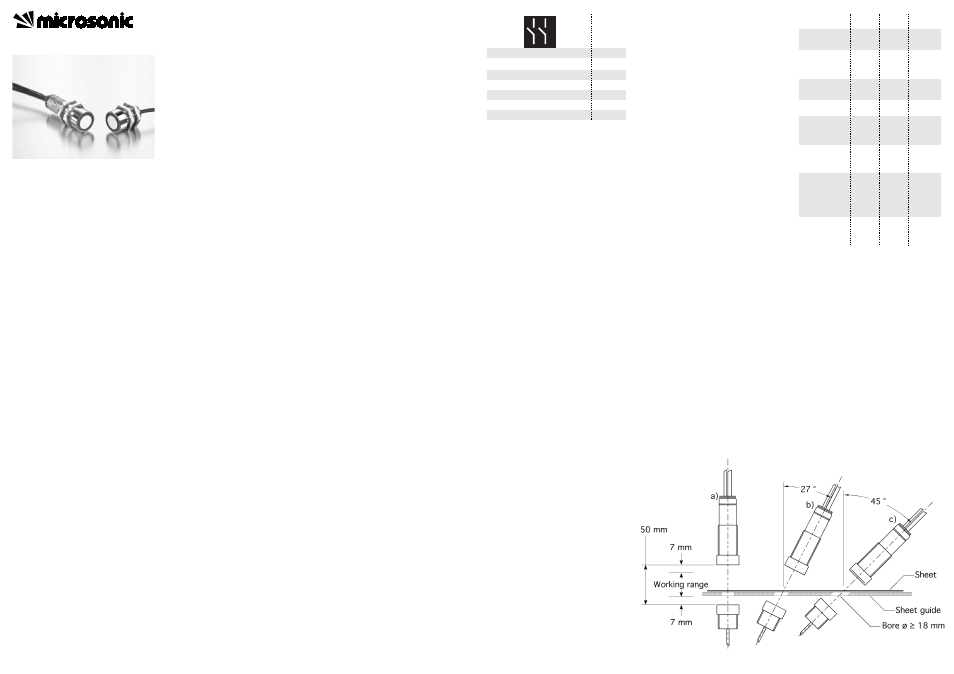
Operating Instructions
Ultrasonic double sheet detection
with 2 switched outputs
dbk+5/3CDD/M18 E+S
dbk+5/3BEE/M18 E+S
Functional principle
The function of the double sheet de-
tection is to detect two or more
sheets or other laminary materials ly-
ing one on top of the other. The sen-
sor system consists of a transmitter
and a receiver complete with integra-
ted evaluation electronics.
A high-frequency ultrasonic transmit-
ter beams from the underside
against the sheet material. The emit-
ted ultrasonic pulse excites the sheet
material into vibrations. The effect of
these vibrations is for a very small
sonic wave on the other side of the
sheet to spread. This wave is received
by the ultrasonic receiver located
there. In the case of sheet one on
top of the other (double sheet), the
receiver detects the difference in sig-
nal and sets its outputs accordingly.
Ultrasonic sensors
Product description
■ Assured detection of single, dou-
ble and multiple sheet.
■ Scanning of sheet material
weights from 100 g/m
2
to 2,000
g/m
2
, corrugated cards, sheet me-
tals, printed circuit boards, films
and plastic sheets up to several
mm thickness possible.
■ Double sheet and missing sheet
output as pnp or npn switched
outputs.
■ Vertical mounting to the sheet run-
ning through permitted.
■ Three control inputs allow for an
external setting of sensitivity for
the material to be scanned.
■ Changes to sensitivity classes un-
der ongoing operations can be un-
dertaken.
■ Additional teach-in mode e.g. for
scanning wafers glued with a wa-
ter film.
■ Optional trigger operation mode
e.g. for applications in the shin-
gled stream.
■ Parameterization via LinkControl
■ 0.5 ms response time until a dou-
ble or missing sheet in the trigger
mode is detected.
■ Transmitter-receiver spacing can
be selected from 30 to 70 mm
Safety tips
■ Read the operating instructions
before start-up.
■ Only qualified personnel are to un-
dertake connection, mounting and
settings.
■ Not a safety component in keep-
ing with the EC Machinery Direc-
tive.
Mounting
▸ Mount transmitter and receiver in
keeping with Fig 1 at the recom-
mended spacing of 50 mm ± 3
mm .
dbk+5 can be fitted at any posi-
tion .
▸ Connect the transmitter to the re-
ceiver using the M8 connector.
▸ Connect the receiver 7-strand con-
trol line in keeping with Fig 2.
Pointer
■ If required, spacing between trans-
mitter and receiver can be ad-
justed to the local circumstances in
the 30 to 70 mm range; see under
»Teach-in spacing between trans-
mitter and receiver«.
■ The coaxiality of transmitter and
receiver must be ≤ 0.5 mm.
■ Transmitter and receiver are not to
be inclined to each other in excess
of 2°.
■ Vertical mounting to the sheet is
recommended for papers (Fig 1a).
■ In case of vertical mounting to the
sheet, the spacing between trans-
mitter and/or receiver and the
sheet running through is not to be
under 7 mm.
■ In case of certain sheet metals or
thicker plastic films, the dbk has to
be mounted at an inclination to
sheet normal depending on the
material (Fig. 1b). If necessary the
optimum mounting position has
to be determined in a test.
■ Thick papers and paperboard re-
sponsible for faulty switching in
case of vertical mounting can of-
ten be scanned at a 27° to 45°
mounting angle to sheet normal.
Corrugated cards have to be mea-
sured obliquely to the waves (Fig
1c).
■ Other materials may make a special
fitting position necessary. Do con-
tact microsonic when you work
with these special materials.
■ The max. torque of the nuts is 15
Nm for the M18 sleeves.
■ The drill hole must be ≥ 12 mm
given that the transmitter is re-
cess-mounted or a sheet feed is
envisaged between transmitter
and receiver. The recommendation
is for a 18 mm diameter (see Fig
1).
■ The line between transmitter and
receiver is not to be bridged with
an external potential.
Fig. 2: Colour coding of the control line
Start-up
▸ Select the »Standard« sensitivity
class by placing all the 3 control
inputs onto logic 0 (see Figs 3 and
4) or leave them unconnected.
Switch on the dbk+5 voltage sup-
ply.
Pointer
■ The »Standard« sensitivity class
corresponds to the setting of
predecessor model dbk-5.
Check the function with a test sheet.
▸ Hold a single test sheet within the
working range between transmit-
ter and receiver.
The LED must light up green for
"Single sheet detected«. (Should the
LED light up red, then check on the
dbk+5 fitting dimension and the se-
lected test sheet.)
▸ Hold a double test sheet within
the working range between trans-
mitter and receiver.
The LED must light up red for "Dou-
ble sheet detected«.
▸ Remove all the sheets between
transmitter and receiver.
The LED must flash red for "Missing
sheet detected«.
+U
B
-U
B
Colour
Brown
Blue
Single/missing sheet output
Double sheet output
Control input C1
Control input C2
Black
White
Violet
Pink
Control input C3/Com
Grey
Pointer
■ You can use a material of a high
sheet weight as the test sheet or
the test sheet itself obtainable as
an accessory with the »dbk test
sheet« article name. This test
sheet works as critical material at
the ambient temperature in the
»Standard« sensitivity class and
can be used to examine the cor-
rect adjustment and function.
Factory setting
The dbk+5 are delivered with the fol-
lowing factory settings:
■ Free-run mode with 3 sensitivity
classes and teach-in
■ Missing sheet output on NCI
■ Double sheet output on NCI
■ 50 mm spacing
Fig. 9: LED displays
Condition
single sheet
single sheet
overmodula-
tion
LED 1
LED 2
Green
Green
Green
Green
+ Red =
Orange
static on
static on
double sheet
missing sheet
Teach-in
activated
Teach-in
dismissed
Red
Red
Red
Red
Green
Red
Green
Red
static on
flashing
flashing
mutually
flashing
mutually
Teach-in spac-
ing transmit-
ter-receiver
Teach-in
dismissed
Red
Red
Green
Red
flashing
mutually
flashing
mutually
Fig. 1: Mounting and installation positions