Microsonic esp-4/3CDD/M18 E+S User Manual
Microsonic Sensors
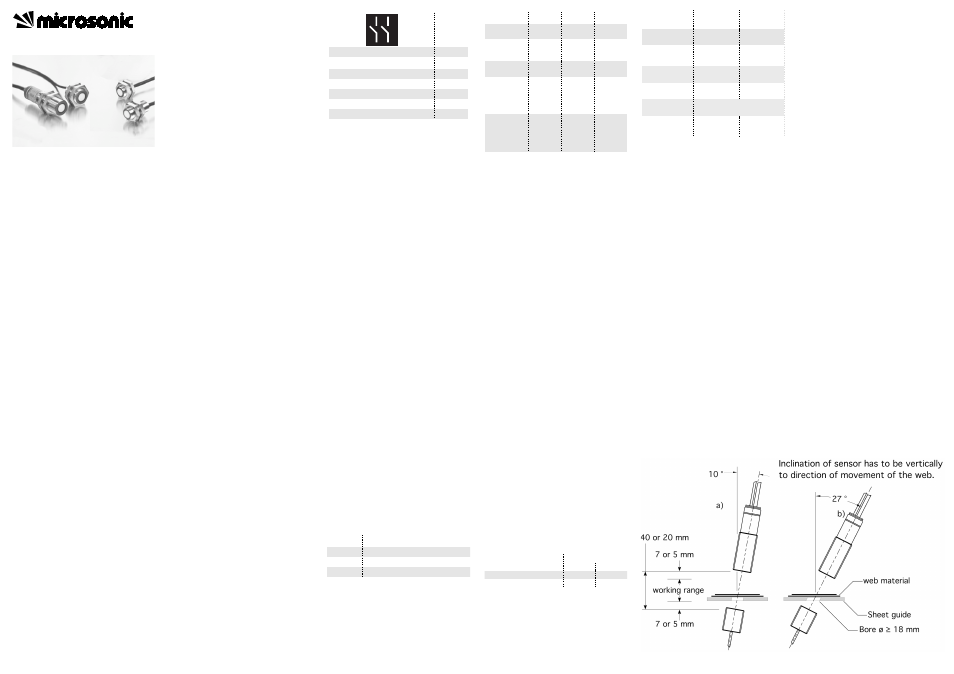
Operating Instructions
Ultrasonic label ans splice sensor
with 2 switched outputs
esp-4/3CDD/M18 E+S
esp-4/3BEE/M18 E+S
esp-4/M12/3CDD/M18 E+S
esp-4/M12/3BEE/M18 E+S
Functional principle
With a rapid pulse sequence, an
ultrasonic
transmitter
beams
upwards
against
the
backing
material. The effect of the sound
pulses inducing the backing material
to vibrate is for a markedly
weakened sonic wave to be emitted
on the opposite side. The receiver
receives this sonic wave and analyses
it.
The backing material signal level is
different to that of the label or
splice. And this difference in signal is
analysed by the esp-4. The difference
between backing material and label
and/or between sheeting and splice
can be very slight indeed. To ensure
certainty with the difference, teach-
in for the esp-4 sensor must firstly
revolver around the signal level for
the backing material/sheeting.
The esp-4 sensors can be used as a
label and splice sensor. The 3 teach-
in methods permit the esp-4 sensor
to be optimally set for each and
every assignment.
Ultrasonic sensors
Product description
■ Assured detection of labels made
of paper, metal or (transparent)
plastic.
■ Detection of splices of paper web,
plastic web or metal web.
■ Label/splice and web break output
as pnp or npn switched outputs.
■ Scanning of material weights from
<60 g/m
2
to >>600 g/m
2
; sheet
metals and plastic films up to 0,6
mm thickness.
■ 3 Teach-in modes.
■ Synchronisation.
■ Parametrization via LinkControl.
■ Response time of 300 µs until
lable/splice is detected.
■ Transmitter - receiver spacing can
be selected from 20 to 40 mm
Safety tips
■ Read the operating instructions
before start-up.
■ Only qualified personnel are to
undertake connection, mounting
and settings.
■ Not a safety component in
keeping with the EC Machinery
Directive.
Mounting
▸ Mount transmitter and receiver in
keeping with Fig 1 at the
recommended spacing of 40 mm
± 3 mm (or 20 mm ± 2 mm with
esp-4/M12/...E+S).
esp-4 can be fitted at any position.
▸ Connect the transmitter to the
receiver using the M8 connector.
▸ Connect the receiver 7-strand
control line in keeping with Fig 2.
Fig. 2:
Colour coding of the control line
Pointer
■ The coaxiality of transmitter and
receiver must be
≤ 0.5 mm.
■ Transmitter and receiver are not to
be inclined to each other in excess
of 2°.
■ In case of thicker plastic films the
esp-4 is to be mounted at a 27°
inclination to sheet normal (Fig.
1b).
■ Other materials may make a spe-
cial fitting position necessary. Do
contact microsonic when you
work with these special materials.
■ The max. torque of the nuts is 15
Nm for the M18 and 8 Nm for the
M12 sleeves respectively.
■ The drill hole must be ≥ 12 mm
given that the transmitter is
recess-mounted or a sheet feed is
envisaged between transmitter
and receiver.
■ The line between transmitter and
receiver is not to be bridged with
an external potential.
Start-up
▸ For normal opperation mode leave
all
the
3
control
inputs
unconnected (see Figs 3 and 4).
▸ Switch on the esp-4 voltage sup-
ply.
Fig. 3:
Function of control inputs
+U
B
-U
B
Colour
Brown
Blue
lable/splice output D1
web break output D2
control input C1
control input C2
White
Black
Violet
Pink
control input C3
Grey
Input
C1
C2
Function
Teach-in
Automatic tracking on/off
C3
Synchronization/communication
1) C3 must not be connected to -U
B
Fig. 4:
Assignment of control inputs
Teach-in
Teach-in is carried out via contol in-
put C1.
There are 3 Teach-in methods:
■ Dynamic teach-in of backing ma-
terial and label
■ Separate teach-in for backing ma-
terial and labels
■ Teach-in only for sheeting
▸ Place the web material between
transmitter and receiver of the
esp-4 and carry out one of the 3
Teach-in methods.
Pointer
■ During Teach-in the control input
C2 has to be left unconnected or
connected to -U
B
and C3 has to
be unconnected.
Operation
The esp-4 performs measurements
cyclically and depending on the
measurement result it sets the two
switched outputs.
The automatic tracking can be put
on/off during runnig operation.
The conditions of LED 1 and 2 are
shown in Fig. 6.
Fig. 5:
Voltage level of the logic states at
the control inputs
Mode
normal
operation
Teach-in
C1
C2
open
or -U
B
See »Te-
ach-in
modes«
open
or -U
B
open
or -U
B
C3
open
1
open
1
automatic
tracking
sychro-
nization
automatic
tracking
and syn-
chronizati-
on
open
or -U
B
open
or -U
B
+U
B
open
or -U
B
open
or -U
B
+U
B
open
1
C3 con-
nected
with
each
other
C3 con-
nected
with
each
other
Logical state
0
Voltage level
pnp
-U
B
npn
+U
B
1
+U
B
-U
B
Fig. 6:
LED displays
Factory setting
The esp-4 are delivered with the
following factory settings:
■ Output label/splice output D1 on
NOC.
■ Output D2 on fuction web break.
■ Ouput web break on NOC.
■ 40 or 20 mm spacing.
■ Operation mode on automatic
tracking on/off via input C2.
Automatic tracking
After a Teach-in the esp-4 can track
the working point automatically. In
this way variations in the material to
be scanned and fluctuation in the
ambient temperature can be com-
pensated.
Via control input C2 the automatic
tracking can be put on and off.
Condition
operation
backing
material
LED 1
LED 2
Green
Green
Green
Green
label/splice
web break
Teach-in
Teach-in
dismissed
Red
Green
Green
Red flashing
See »Teach-in methods«
Green
Red flashing
Synchronization
If two or more esp-4 shall work close
together they may influence one
another. To avoid this the esp-4 can
be synchronized. To do this all contol
inputs C3 have to be connected with
each other.
Parameterization with
LinkControl
The esp-4 can be extensively
parameterized under LinkControl.
Here you need the optionally
available LinkControl adapter LCA-2
and the LinkControl software for
Windows©.
Operation onto LinkControl
▸ Install the LinkControl software
onto your PC.
Connect the LinkControl adapter
to your PC with the USB cable.
▸ Connect esp-4 to the LCA-2 in
keeping with the Fig 7 table. For
this, use the adapter cable in the
LCA-2 case.
▸ Connect the voltage supply cable
to the LCA-2 on the other side of
the T connector.
▸ Start the LinkControl software and
follow the instructions on the
screen.
Fig. 1:
Mounting and installation positions