Installation, Assembly of mig system – Kemppi Protig 501L User Manual
Page 11
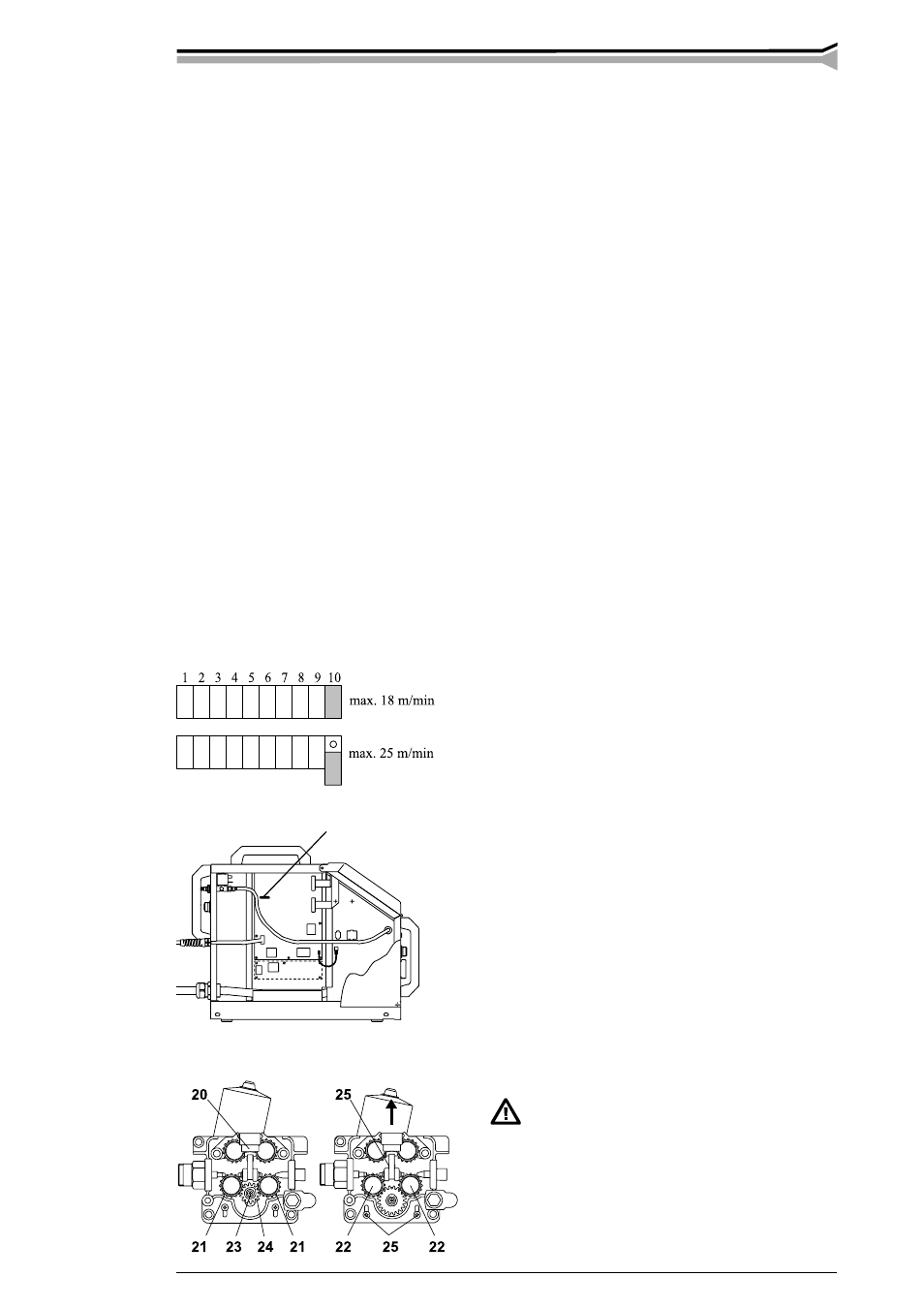
PROMIG 501, PROMIG 511/0537 – 11
© KEMPPI OY
JUMPER BLOCK
A001
2. INSTALLATION
2.1. ASSEMBLY OF MIG SYSTEM
Assemble the units in below-mentioned order and follow mounting and operation instructions
which are delivered in packages.
1. Installation of power source
Read paragraph: ”Installation” in operation instructions 1913170 for PRO power sources and
carry out the installation according to that.
2. Mounting of PRO power source to transport wagon
P40 6185261, air-cooled MIG system mounting / assembly instructions 4270450
P30W 6185262, liquid-cooled MIG system mounting / assembly instructions 4270460
3. Put the PROMIG onto the power source and lock it with bolts to handles of power source
4. Mounting of PROMIG control panel
MC 6263501, mounting instructions 4270950
ML 6263502, mounting instructions 4270950
5. Connecting cables
Connect cables according to figures on pages 6...7.
Air-cooled system on page 6. Liquid-cooled system on page 7.
You can change polarity of filler wire by interchanging the PROMIG welding current cable
and earth cable with welding cable connectors of PRO power source.
6. Max. wire feed speed
When the unit is delivered the max. wire feed speed is 18 m/min, which is enough for most
welding works. If you need a higher speed, you can increase the max. wire feed speed to 25
m/min by replacing the gear wheel on motor shaft to a bigger one. The big gear wheel D40 is
delivered with the feed unit in accessory drawer.
When necessary speed is changed according to follo-
wing:
– Open side plate and move JUMPER BLOCK’s
10 th coding piece on control card A001 to
point 25 m/min.
– Open tightening lever (20). Remove lower feed
rolls (21). Release screw (23) and its washer.
Remove gear wheel D28 (24) from motor shaft.
– Loosen screws (25) (3 pc) 1 twist. Mount the
D40 gear wheel onto motor shaft. Screw the
screw (23) with its washer back.
– Put feed rolls (21) back to their axles, however
don’t fasten yet fastening screws of feed rolls (22).
– Lift the motor so that the tooth gap between gear
wheel and both lower feed rolls is approx. 0,2 mm.
– Tighten screws (25). Check gear teeth gaps,
when necessary put the motor into a better position.
Screw on the mounting screws of feed rolls (22).
Too small gap between gear wheel and
feed rolls will overload motor.
Too big gap for its part might cause too
rapid wearing for teeth of feed rolls and
gear wheel.