Flowserve CPXV fitted with WW User Manual
Page 24
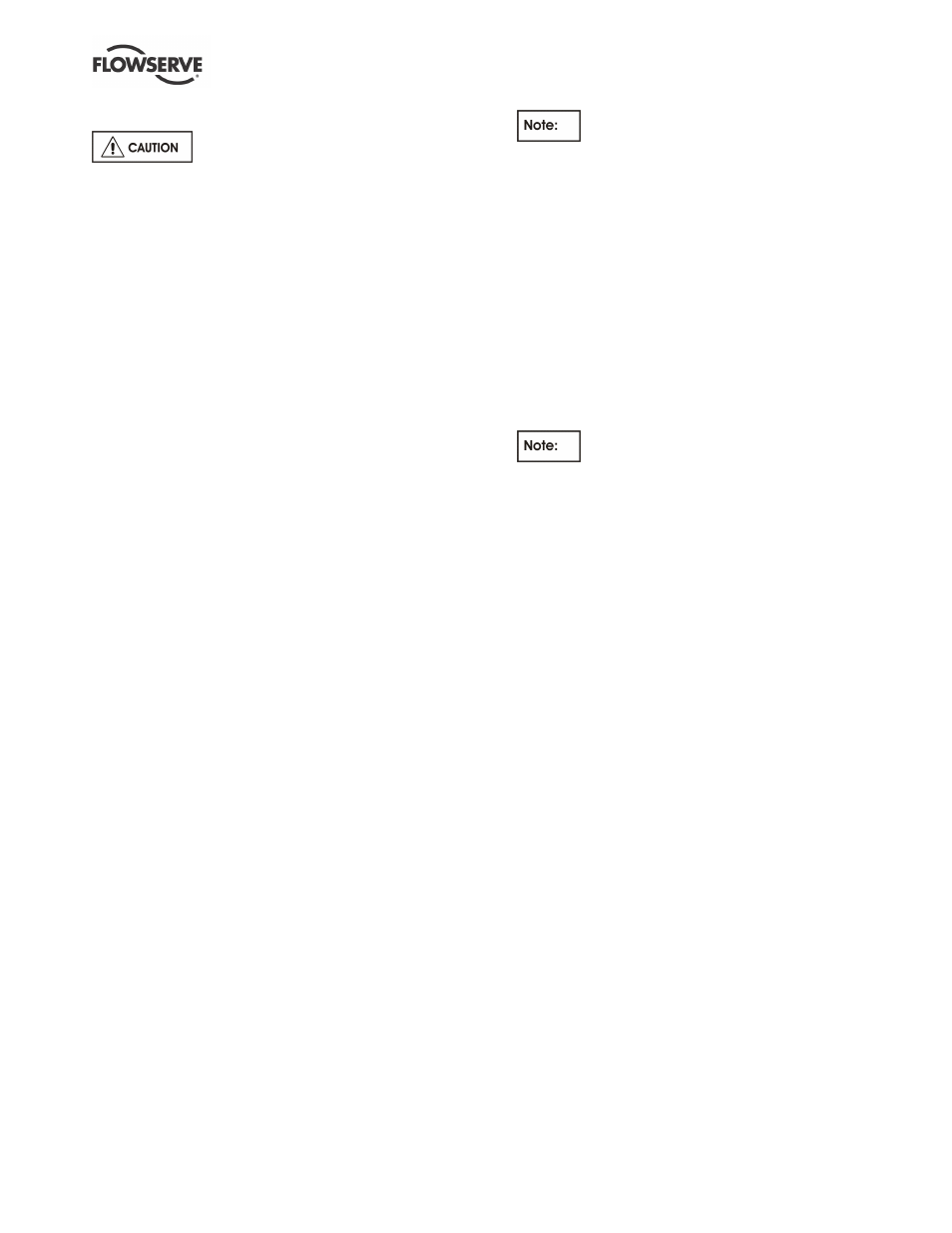
CPXV - WW/CW USER INSTRUCTIONS ENGLISH 85392698 10-09
Page 24 of 36
flowserve.com
6.10 Examination of parts
Used parts must be inspected before
assembly to ensure the pump will subsequently run
properly. In particular, fault diagnosis is essential to
enhance pump and plant reliability.
6.10.1 Casing, seal housing and impeller
Inspect for excessive wear, pitting, corrosion, erosion
or damage and any sealing surface irregularities.
Replace as necessary.
6.10.2 Shaft and sleeve (if fitted)
Obtain and fit a new shaft or sleeve if grooved, pitted
or worn.
6.10.4 Gaskets and O-rings
After dismantling, discard and replace.
6.10.5 Bearings
It is recommended that bearings are not re-used after
any removal from the shaft.
The plain bearings may be re-used if both the bearing
bush and bearing sleeve show no sign of wear, grooving
or corrosion attack. It is recommended that both the
bush and sleeve are replaced at the same time.
6.11 Assembly
To assemble the pump consult the sectional
drawings. See section 8, Parts lists and drawings.
Ensure threads, gasket and O-ring mating faces are
clean. Apply thread sealant to non-face sealing pipe
thread fittings.
6.11.1 Mechanical seal or gland packing seal
(If there is no mechanical seal or gland packing at the
soleplate, go to section 6.11.2, Thrust bearing carrier
and shaft sub-assembly.)
Where a mechanical seal is used, extreme cleanliness
is required during assembly. In many instances a pre-
assembled cartridge seal will be used. Where this is not
the case the sealing faces must be checked to be free
from scratches or other damage.
a) Use olive oil for fitting elastomers.
b) Where an anti-rotation pin is fitted ensure that
correct engagement with the slot is achieved.
c) Carefully press stationary mechanical seal seat(s)
into their housing such that these are not deformed
or damaged.
d)
Work to the specific manufacturer’s
instructions for the mechanical seal.
Where a packed stuffing box is fitted, pack the stuffing
box cover before fitting on to the shaft as follows:
a) Position each ring into the box individually, evenly
and firmly.
b) Check that the shaft sleeve freely rotates after
fitting the first ring.
c) Stagger the 45 degree scarf joints by 90 degrees
from each other in the box.
d) Insert the inner two packing rings.
e) Insert lantern ring halves (if required).
f) Insert the remaining packing rings.
g) Position the gland squarely against the last ring,
tighten the gland nuts finger-tight only and install
onto bearing housing assembly.
Jacketed sump pumps are fitted with a
gland packing seal at the soleplate.
6.11.2 Thrust bearing carrier and shaft sub-
assembly
a) Clean the inside of the bearing carrier and bores
for the bearings.
b) On grease lubricated bearings fill the bearing
carrier retaining ring internal slot with the
appropriate grease. The three thin grease rings
may now be inserted into this internal slot.
c) The bearing carrier retaining ring sub-assembly
and bearing sleeve, applicable on shaft sizes 3
and 4, should now be placed over the shaft
before fitting the thrust bearing. The retaining
ring must have the C spanner slots facing the
impeller end.
(Note 1: On units fitted with a proprietary
soleplate mechanical seal, this and any additional
housing should be passed over the shaft before
the thrust bearing outer nut.)
(Note 2: In the case of a proprietary PTFE vapor
seal, this is fitted into the locking ring as a
subassembly. Place the thrust bearing on to the
shaft. If an optional pair of thrust bearings is to
be fitted, these must be mounted back-to-back,
as described below.)
d) Press the thrust bearing onto the shaft using
equipment that can provide a steady, even load
to the inner race.
e) Oil bath lubricated thrust bearing is an option.
f)
If grease lubrication as standard, use a spatula to fill
sides of the bearing with grease of NLGI 3 grade.