Floscan Series 9700/97000 Standard Flow GPS Interface System (twin engine model) User Manual
Page 38
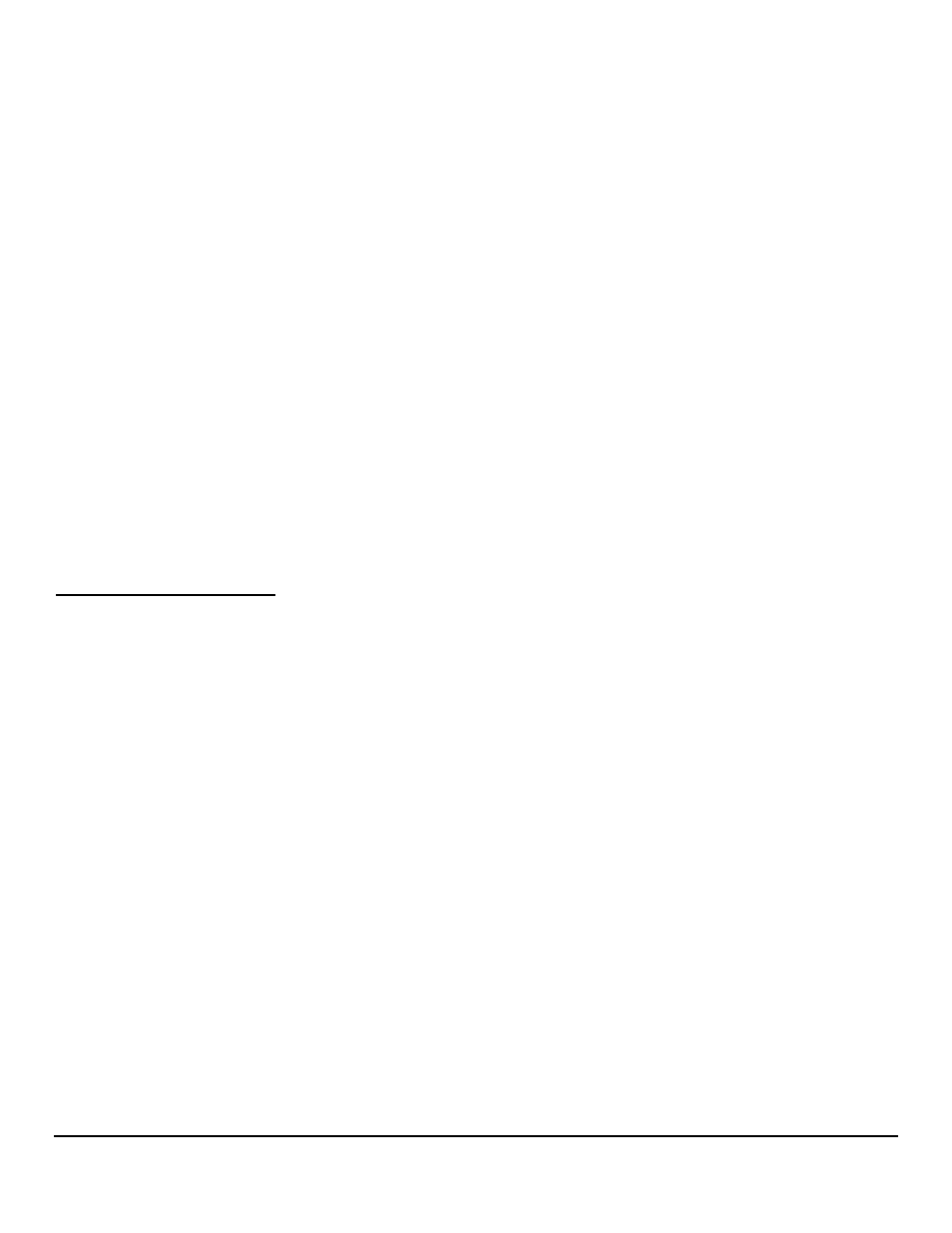
8/30/2004
7000-074-00D
FloScan Instrument Company, Inc.
Tel:
(206)
524-6625
Fax:
(206)
523-4961
3016 NE Blakeley Street, Seattle, WA 98105
Email:
Http://www.floscan.com
1. Check continuity of the YELLOW and VIOLET Tachometer signal wires, (Section VI). Verify that the tachometer signal wires
are connected at the correct signal output point.
2. Disconnect either the YELLOW or VIOLET Tachometer signal wire from the Tachometer Sender. Connect an Ohmmeter to the
two sender wires and measure its’ resistance. AC Signal Generators should measure approximately 180
Ω, (±) 10%. Magnetic
Pick-ups can measure between 100 to 800
Ω depending on manufacturer.
3. Next connect an AC Voltmeter to the sender wires. Both AC Signal Generator and Magnetic Pick-up senders should produce at
least several volts at idle.
4. If the voltmeter reads “0” on an AC Signal Generator, it may not be properly attached to its drive port. Verify that its’ drive shaft
and tang are installed correctly.
5. If the voltmeter reads, “0” on a Magnetic Pick-up sender, it may not be installed correctly. With engine stopped, loosen its’ lock
nut. Turn the sender clockwise until it bottoms out. Back the sender out 1/8
th
to 1/4
th
turn. Turn the engine over by hand, or slowly
jog it to verify adequate clearance.
6. Engine alternators tend to be an inaccurate Tachometer signal source, especially at low Rpm’s. The engine may have to be revved
up before the Tachometer will read.
B. HIGH OR LOW READINGS.
1. Verify that the Tachometer is calibrated correctly.
C. FLUCTUATING READINGS.
1. Listen to your engine(s). If engine speed cycles up and down, (when idling or underway) the tachometer reading will follow.
This does not indicate a problem with the Tachometer, but may indicate engine problems.
2. Verify that wiring connections are tight, clean and dry. Check continuity while shaking the wires. Ohm readings should be
near zero and remain steady while shaking.
3. Verify that the tachometer signal wires are connected at the correct signal output point.
VIII. PULSATION PROBLEMS
A stiff anti-siphon valve(s) or miss-plumbed Pulsation Damper(s) can cause fluctuating GPH readings. These are most pronounced at
low Rpm’s and tend to disappear around mid throttle. They are annoying, but won’t affect totalizer accuracy. To eliminate, repair or
replace any defective valves, or re-plumb dampers according to the Fuel Flow Schematic Instructions.
IX. FINDING FUEL SYSTEM VACUUM LEAKS
Fluctuating GPH and High Totalizer Readings are usually caused by a small vacuum leak between the fuel tank and fuel pump inlet.
Fluctuations tend to be between 2 and 4 GPH. These vacuum leaks also affect totalizer accuracy, causing it to read 15 to 100% high.
Larger leaks produce greater fluctuations and higher readings. They generally do not affect engine performance.
Finding suction leaks can be time-consuming. When approached properly, they can usually be found and repaired quickly. Two
common places for suction leaks to occur are at the primary fuel filter - water separator, and/or a loose valve stem packing nut.
Remove the filter housing and coat all o-rings, gaskets and sealing surfaces with a medium to heavy grease, (Do not use oil) and
reassemble. Grease all valve stem packings and gently tighten gland nuts. Don’t over tighten, valve handles should turn freely.
Tighten all hose clamps and compression fittings. Don’t over tighten. Run the engine for 5 to 10 minutes observing GPH readings. If
you’ve found the problem, fluctuations should be reduced to less than ½ GPH.
If the problem persists, temporarily install a clear piece of fuel resistant hose downstream of the forward flow sensor. Run the engine
and watch for a stream of small bubbles in the clear hose, or an occasional larger bubble. Sometimes shining a light through the hose
makes bubbles easier to see.
Observe the clear hose while shaking the fuel lines. If the bubble stream continually increases or decreases you’ve found the leak area.
Repair or replace as needed. If this occurs one-time, you probably dislodged some trapped air.
If the leak hasn’t been found, the last step is to inspect each pipe joint. Thread sealant should be visible around each joint. If not, that
joint is suspect and must be resealed. After resealing run the engine for a few minutes to purge any remaining air. There should now
be bubble free fuel running through the clear hose. If bubbles are still present a leak was missed. Recheck your work. After all the
leaks are stopped, remove the clear hose.
- 930M-201-2K Standard Flow GPS Interface System 930M-231-2K Standard Flow GPS Interface System 930M-BOS-2K Standard Flow GPS Interface System 930M0-2012K Standard Flow GPS Interface System 930M0-2312K Standard Flow GPS Interface System 930M0-BOS2K Standard Flow GPS Interface System 93TM-235-2K Standard Flow GPS Interface System 970M-201-2K Standard Flow GPS Interface System 970M-231-2K Standard Flow GPS Interface System 970M-235-2K Standard Flow GPS Interface System 970M-BOS-2K Standard Flow GPS Interface System 970M0-2012K Standard Flow GPS Interface System 970M0-2312K Standard Flow GPS Interface System 970M0-BOS2K Standard Flow GPS Interface System 97TM-235-2K Standard Flow GPS Interface System 97TM0-2352K Standard Flow GPS Interface System Series 7500/75000 Standard Flow Multifunction Meter 750M-201-2K Standard Flow Multifunction Meter 750M-231-2K Standard Flow Multifunction Meter 750M-BOS-2K Standard Flow Multifunction Meter 750M0-2012K Standard Flow Multifunction Meter 750M0-2312K Standard Flow Multifunction Meter 750M0-BOS2K Standard Flow Multifunction Meter 75TM-235-2K Standard Flow Multifunction Meter 75TM0-2352K Standard Flow Multifunction Meter 77TM-235-2K Standard Flow Multifunction Meter 770M-201-2K Standard Flow Multifunction Meter 770M-231-2K Standard Flow Multifunction Meter 770M-BOS-2K Standard Flow Multifunction Meter 770M0-BOS2K Standard Flow Multifunction Meter 770M0-2312K Standard Flow Multifunction Meter Series 6500/65000 Standard Flow CruiseMaster 6310-201-2K Standard Flow CruiseMaster 6310-BOS-2K Standard Flow CruiseMaster 6320-201-2K Standard Flow CruiseMaster 6320-231-2K Standard Flow CruiseMaster 6320-BOS-2K Standard Flow CruiseMaster 6305-201-2K Standard Flow CruiseMaster 6505-201-2K Standard Flow CruiseMaster 6505-BOS-2K Standard Flow CruiseMaster 65080-2012K Standard Flow CruiseMaster 6510-201-2K Standard Flow CruiseMaster 6510-231-2K Standard Flow CruiseMaster 6510-BOS-2K Standard Flow CruiseMaster 6520-201-2K Standard Flow CruiseMaster 6520-231-2K Standard Flow CruiseMaster 6520-BOS-2K Standard Flow CruiseMaster 6532-231-2K Standard Flow CruiseMaster 6532-BOS-2K Standard Flow CruiseMaster 6710-BOS-2K Standard Flow CruiseMaster 6720-BOS-2K Standard Flow CruiseMaster 63040-BOS2K Standard Flow CruiseMaster 63080-BOS2K Standard Flow CruiseMaster 65040-2012K Standard Flow CruiseMaster 65040-2312K Standard Flow CruiseMaster 65040-BOS2K Standard Flow CruiseMaster 65080-2312K Standard Flow CruiseMaster 65080-BOS2K Standard Flow CruiseMaster 65160-2312K Standard Flow CruiseMaster 65160-BOS2K Standard Flow CruiseMaster Series 9500/95000 Standard Flow GPS Interface System (single engine model) 910M-201-2K Standard Flow GPS Interface System 910M-231-2K Standard Flow GPS Interface System 910M-BOS2K Standard Flow GPS Interface System 910M0-2012K Standard Flow GPS Interface System 910M0-2312K Standard Flow GPS Interface System 910M0-BOS2K Standard Flow GPS Interface System 91TM-235-2K Standard Flow GPS Interface System 950M-201-2K Standard Flow GPS Interface System 950M-231-2K Standard Flow GPS Interface System 950M-BOS-2K Standard Flow GPS Interface System 950M0-2012K Standard Flow GPS Interface System 950M0-2312K Standard Flow GPS Interface System 950M0-BOS2K Standard Flow GPS Interface System 95TM-235-2K Standard Flow GPS Interface System 95TM0-2352K Standard Flow GPS Interface System Series 9600/96000 High Flow GPS Interface System (single engine model) 920M-3BB-2K High Flow GPS Interface System 920M-3CB-2K High Flow GPS Interface System 920M-3DC-2K High Flow GPS Interface System 920M-3ED-2K High Flow GPS Interface System 920M0-3BB2K High Flow GPS Interface System 920M0-3DC2K High Flow GPS Interface System 920M0-3ED2K High Flow GPS Interface System 92TM-6CB-2K High Flow GPS Interface System 92TM-6CC-2K High Flow GPS Interface System 92TM-6DC-2K High Flow GPS Interface System 92TM-6DD-2K High Flow GPS Interface System 92TM0-6CB2K High Flow GPS Interface System 92TM0-6ED2K High Flow GPS Interface System 960M-3BB-2K High Flow GPS Interface System 960M-3CB-2K High Flow GPS Interface System 960M-3CC-2K High Flow GPS Interface System 960M-3DC-2K High Flow GPS Interface System 960M-3DD-2K High Flow GPS Interface System 960M-3ED-2K High Flow GPS Interface System 960M-3EE-2K High Flow GPS Interface System 960M-3FE-2K High Flow GPS Interface System 96EM-6DC-2K High Flow GPS Interface System 96EM-6ED-2K High Flow GPS Interface System 96EM-6FE-2K High Flow GPS Interface System 960M0-3BB2K High Flow GPS Interface System 960M0-3CB2K High Flow GPS Interface System 960M0-3CC2K High Flow GPS Interface System 960M0-3DB2K High Flow GPS Interface System 960M0-3DC2K High Flow GPS Interface System 960M0-3DD2K High Flow GPS Interface System 960M0-3ED2K High Flow GPS Interface System 960M0-3FE2K High Flow GPS Interface System 96TH -6DB-2K High Flow GPS Interface System 96TM-6BB-2K High Flow GPS Interface System 96TM-6CB-2K High Flow GPS Interface System 96TM-6CC-2K High Flow GPS Interface System 96TM-6DB-2K High Flow GPS Interface System 96TM-6DC-2K High Flow GPS Interface System 96TM-6DD-2K High Flow GPS Interface System 96TM-6ED-2K High Flow GPS Interface System 96TM-6FD-2K High Flow GPS Interface System 96TM-6FE-2K High Flow GPS Interface System 96TM0-6BB2K High Flow GPS Interface System 96TM0-6CB2K High Flow GPS Interface System 96TM0-6CC2K High Flow GPS Interface System 96TM0-6DC2K High Flow GPS Interface System 96TM0-6DD2K High Flow GPS Interface System 96TM0-6ED2K High Flow GPS Interface System 96TM0-6FE2K High Flow GPS Interface System 96TM0-6FD2K High Flow GPS Interface System 96TM0-6EE2K High Flow GPS Interface System Series 7600/76000 High Flow Multifunction Meter 760M-3BB-2K High Flow Multifunction Meter 760M-3CB-2K High Flow Multifunction Meter 760M-3CC-2K High Flow Multifunction Meter 760M-3DB-2K High Flow Multifunction Meter 760M-3DC-2K High Flow Multifunction Meter 760M-3DD-2K High Flow Multifunction Meter 760M-3ED-2K High Flow Multifunction Meter 760M-3EE-2K High Flow Multifunction Meter 760M-3FC-2K High Flow Multifunction Meter 760M-3FE-2K High Flow Multifunction Meter 760M0-3BA2K High Flow Multifunction Meter 760M0-3BB2K High Flow Multifunction Meter 760M0-3CB2K High Flow Multifunction Meter 760M0-3CC2K High Flow Multifunction Meter 760M0-3DB2K High Flow Multifunction Meter 760M0-3DC2K High Flow Multifunction Meter 760M0-3DD2K High Flow Multifunction Meter 760M0-3ED2K High Flow Multifunction Meter 760M0-3FE2K High Flow Multifunction Meter 76EM-6DC-2K High Flow Multifunction Meter 76EM-6ED-2K High Flow Multifunction Meter 76EM-6FE-2K High Flow Multifunction Meter 76TH-6DB-2K High Flow Multifunction Meter 76TH-6ED-2K High Flow Multifunction Meter 76TM-6BB-2K High Flow Multifunction Meter 76TM-6CB-2K High Flow Multifunction Meter 76TM-6CC-2K High Flow Multifunction Meter 76TM-6DB-2K High Flow Multifunction Meter 76TM-6DC-2K High Flow Multifunction Meter 76TM-6DD-2K High Flow Multifunction Meter 76TM-6EC-2K High Flow Multifunction Meter 76TM-6ED-2K High Flow Multifunction Meter 76TM-6FC-2K High Flow Multifunction Meter 76TM-6FD-2K High Flow Multifunction Meter 76TM-6FE-2K High Flow Multifunction Meter 76TM0-6BB2K High Flow Multifunction Meter 76TM0-6CB2K High Flow Multifunction Meter 76TM0-6CC2K High Flow Multifunction Meter 76TM0-6DB2K High Flow Multifunction Meter 76TM0-6DC2K High Flow Multifunction Meter 76TM0-6DD2K High Flow Multifunction Meter 76TM0-6EC2K High Flow Multifunction Meter 76TM0-6ED2K High Flow Multifunction Meter 76TM0-6EE2K High Flow Multifunction Meter 76TM0-6FD2K High Flow Multifunction Meter 76TM0-6FE2K High Flow Multifunction Meter 780M-3BB-2K High Flow Multifunction Meter 780M-3CB-2K High Flow Multifunction Meter 780M-3DD-2K High Flow Multifunction Meter 78TM-6FE-2K High Flow Multifunction Meter 78TM-6CB-2K High Flow Multifunction Meter Series 6600/66000 High Flow CruiseMaster 6320-3CB-2K High Flow CruiseMaster 6332-3BB-2K High Flow CruiseMaster 66100-3CB2K High Flow CruiseMaster 66100-3CC2K High Flow CruiseMaster 66100-3DB2K High Flow CruiseMaster 66100-3DC2K High Flow CruiseMaster 66100-3DD2K High Flow CruiseMaster 66100-3EC2K High Flow CruiseMaster 66100-3ED2K High Flow CruiseMaster 66100-3EE2K High Flow CruiseMaster 66100-3FE2K High Flow CruiseMaster 6620-3BB-2K High Flow CruiseMaster 6620-3CB-2K High Flow CruiseMaster 66200-3EE2K High Flow CruiseMaster 66200-3FD2K High Flow CruiseMaster 66200-3FF2K High Flow CruiseMaster 6632-3BA-2K High Flow CruiseMaster 6632-3BB-2K High Flow CruiseMaster 6632-3CB-2K High Flow CruiseMaster 6632-6DB-2K High Flow CruiseMaster 6632-3DD-2K High Flow CruiseMaster 6650-3BB-2K High Flow CruiseMaster 6650-3CB-2K High Flow CruiseMaster 6650-3CC-2K High Flow CruiseMaster 6650-3DB-2K High Flow CruiseMaster 6650-3DC-2K High Flow CruiseMaster 6650-3DD-2K High Flow CruiseMaster 6650-3ED-2K High Flow CruiseMaster 6650-3FF-2K High Flow CruiseMaster 66080-3BB2K High Flow CruiseMaster 66080-3CB2K High Flow CruiseMaster 66080-3CC2K High Flow CruiseMaster 66160-3BB2K High Flow CruiseMaster 66160-3CB2K High Flow CruiseMaster 66160-3CC2K High Flow CruiseMaster 66160-3DB2K High Flow CruiseMaster 66160-3DC2K High Flow CruiseMaster 66160-3DD2K High Flow CruiseMaster 66500-3BB2K High Flow CruiseMaster 66500-3CB2K High Flow CruiseMaster 66500-3CC2K High Flow CruiseMaster 66500-3DB2K High Flow CruiseMaster 66500-3DD2K High Flow CruiseMaster 66500-3DC2K High Flow CruiseMaster 66500-3ED2K High Flow CruiseMaster 66500-3EE2K High Flow CruiseMaster Series 9800/98000 High Flow GPS Interface System (twin engine model) 940M0-3CB2K High Flow GPS Interface System 940M0-3ED2K High Flow GPS Interface System 940M-3BB-2K High Flow GPS Interface System 940M-3CB-2K High Flow GPS Interface System 940M-3DC-2K High Flow GPS Interface System 940M-3ED-2K High Flow GPS Interface System 94TM0-6CB2K High Flow GPS Interface System 94TM0-6ED2K High Flow GPS Interface System 94TM-6CB-2K High Flow GPS Interface System 94TM-6DC-2K High Flow GPS Interface System 94TM-6DD-2K High Flow GPS Interface System 980M0-3BB2K High Flow GPS Interface System 980M0-3CB2K High Flow GPS Interface System 980M0-3CC2K High Flow GPS Interface System 980M0-3DB2K High Flow GPS Interface System 980M0-3DC2K High Flow GPS Interface System 980M0-3DD2K High Flow GPS Interface System 980M0-3ED2K High Flow GPS Interface System 980M0-3FE2K High Flow GPS Interface System 980M-3BB-2K High Flow GPS Interface System 980M-3CB-2K High Flow GPS Interface System 980M-3CC-2K High Flow GPS Interface System 980M-3DB-2K High Flow GPS Interface System 980M-3DC-2K High Flow GPS Interface System 980M-3DD-2K High Flow GPS Interface System 980M-3ED-2K High Flow GPS Interface System 980M-3EE-2K High Flow GPS Interface System 98EM-6DC-2K High Flow GPS Interface System 98EM-6ED-2K High Flow GPS Interface System 98EM-6FE-2K High Flow GPS Interface System 98TH-6DB-2K High Flow GPS Interface System 98TM0-6BB2K High Flow GPS Interface System 98TM0-6CB2K High Flow GPS Interface System 98TM0-6CC2K High Flow GPS Interface System 98TM0-6DB2K High Flow GPS Interface System 98TM0-6DC2K High Flow GPS Interface System 98TM0-6DD2K High Flow GPS Interface System 98TM0-6ED2K High Flow GPS Interface System 98TM0-6FD2K High Flow GPS Interface System 98TM0-6FE2K High Flow GPS Interface System 98TM-6BB-2K High Flow GPS Interface System 98TM-6CB-2K High Flow GPS Interface System 98TM-6CC-2K High Flow GPS Interface System 98TM-6DB-2K High Flow GPS Interface System 98TM-6DC-2K High Flow GPS Interface System 98TM-6DD-2K High Flow GPS Interface System 98TM-6EC-2K High Flow GPS Interface System 98TM-6ED-2K High Flow GPS Interface System 98TM-6FD-2K High Flow GPS Interface System 98TM-6FE-2K High Flow GPS Interface System