Tool rest position, Mounting the work – Delta 46-715 User Manual
Page 11
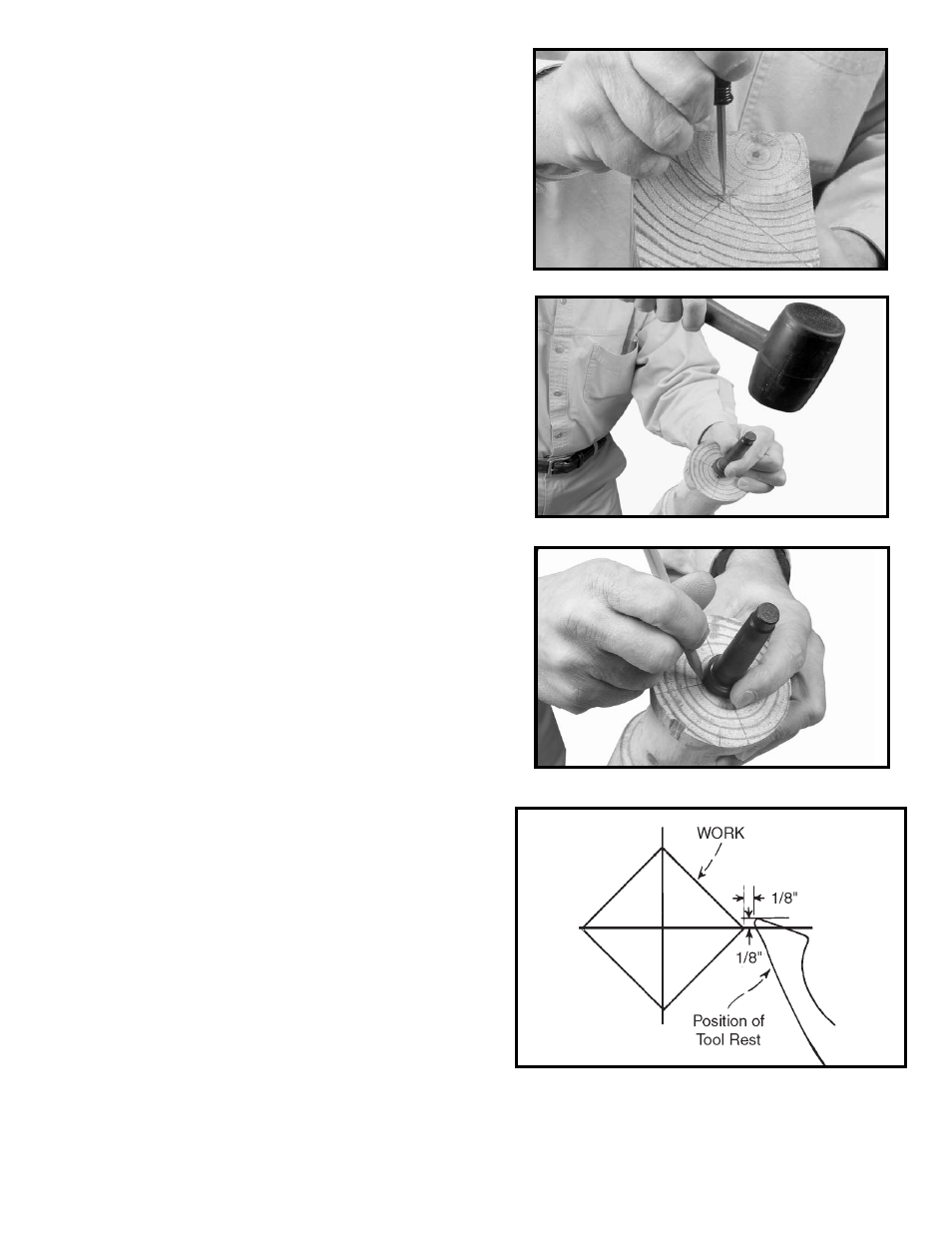
11
Fig. 29
Fig. 30
TOOL REST POSITION
Mount the tool rest in place about 1/8" away from
the work and 1/8" above the work centerline (Fig. 32.)
This position may be varied to suit the work and the
operator. Place a guide mark on the tool rest shank as
an aid to quick and accurate resetting.
CAUTION: CLAMP THE TOOL REST FIRMLY BEFORE
OPERATING THE LATHE.
MOUNTING THE WORK
Mount the work by moving the tailstock to a position
about 1" or 1-1/2" from the end of the workpiece, and
locking it in this position. Advance the tailstock center
by turning the feed handle until the center cup makes
contact with the work. Do not support the work on the
center pin alone. Always have the rim of the center cup
imbedded at least 1/8" into the work. Continue to
advance the center while slowly rotating the work by
hand. After it becomes difficult to turn the work, slack
off on the feed about one-quarter turn and lock the tail-
stock spindle.
After marking each end, mark the true center with a
punch awl or dividers (Fig. 29). If the stock is hardwood,
the centers should be drilled to a depth of about 1/8".
The spur or live center is then placed against one end of
the work and seated by striking with a mallet (Fig. 30). In
hardwood, make a starting seat for the spur center by
sawing on the diagonal lines, and drilling a small hole at
the intersection. After driving the center, hold the center
and the work together and fit both immediately into the
headstock spindle. If you are not using a ball bearing
center, the end of work at tailstock center should be
oiled. Place the lubricant on the wood either before or
after it is put on the lathe. Many turners use beeswax,
tallow, or a wax-and-oil mixture as a lubricant. A ball
bearing center is ideal because it eliminates lubricating.
If the work is to be removed from the lathe before com-
pletion, an index mark should be made as a guide for re-
centering (Fig. 31). A permanent indexer can be made by
grinding off one corner of one of the spurs.
Fig. 31
Fig. 32