Setpoint slope, 7 alarm and counter settings, Alarm settings – Bronkhorst FlowPlot User Manual
Page 17: Alarm and counter settings
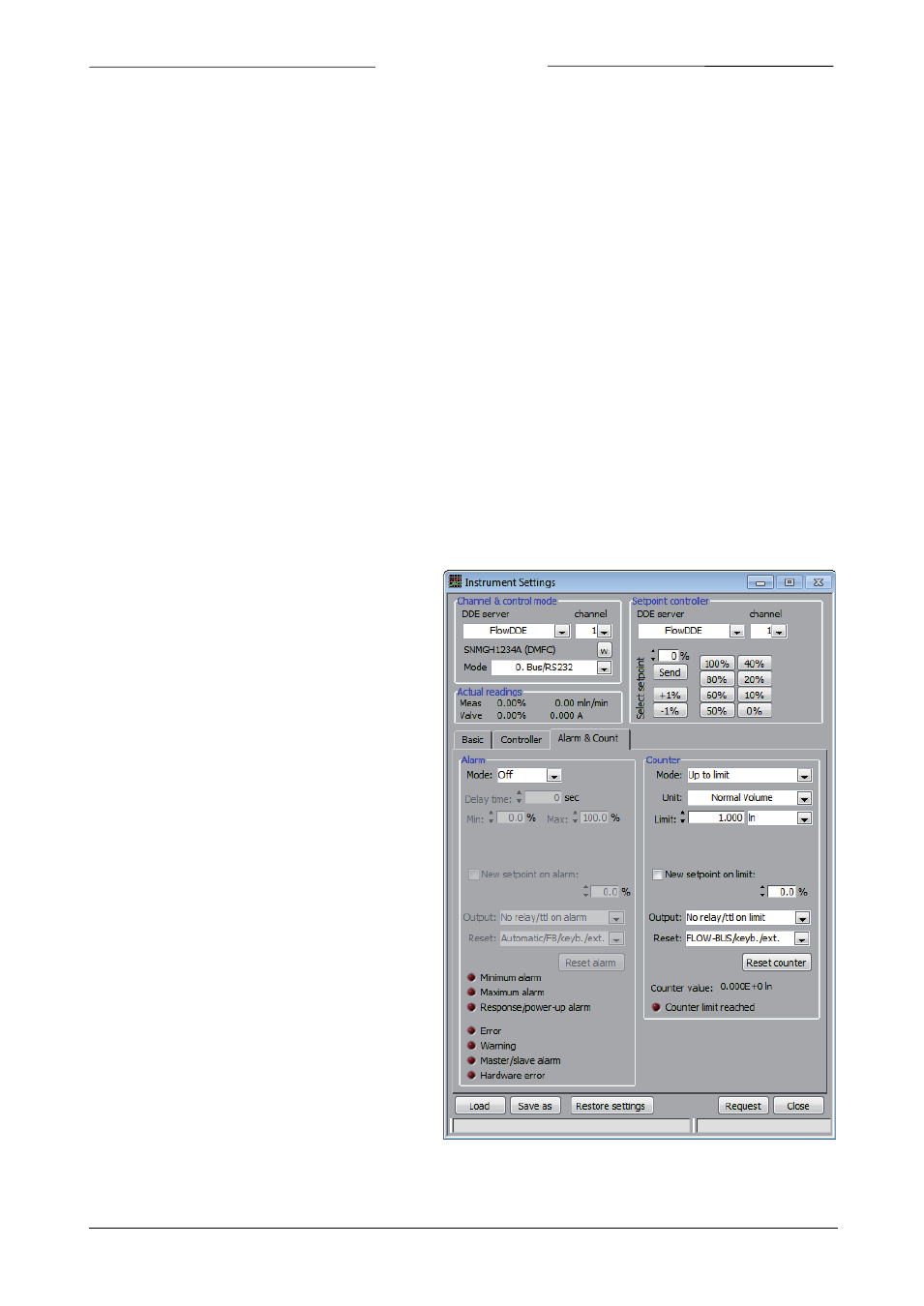
BRONKHORST
®
Valve output steps is a special feature and will set the instrument into a mode in which from the last two setpoints
the valve output values will be stored. Sending one of these setpoints to the instrument will immediately result in
setting the valve to the stored output value, than the PID-controller will take over. This option is for very special
applications only. This option is not to be used with pilot-valves because of hysteresis!
Valve overshoot protection will prevent the valve from overshooting, but still open from zero quite fast.
Setpoint slope
Smooth setpoint control can be established using the Setpoint slope. The setpoint will be linearly increased over time
from the old setpoint value to the new setpoint value. A value between 0 and 3000 seconds, with a resolution of 0.1
seconds, can be given to set the time for the integrator on the setpoint signal.
The setpoint will reach its end value after this many seconds:
0.01
* setpoint slope * | new setpoint – old setpoint |
Example: when the setpoint slope is 10 seconds, how long will it take to go from setpoint 20% to 80%?
0.01 * 10 * | 80 – 20 | = 6 seconds
Apart from the normal application purposes, the setpoint slope appeared to be very useful for the internal (software)
controlling mechanism of steering pilot operated valves (e.g. 033, 002AC, 003AC/BC). Due to the mechanical
construction of these valves (containing a small pilot and a bigger main valve), there could be a little overshoot the
first time the main valve opens. Giving setpoint slope a value of about 1 second may reduce this behavior significantly.
This option could be used in combination with special controller feature Automatic slope for pilot valves.
2.6.7
Alarm and counter settings
Alarm settings
Digital instruments contain features to raise an alarm
when a certain event happens. Some of these alarms
indicate an error or warning, showing some
diagnostic information about the state of the
instrument.
On the other hand, the user may select a scenario in
which an alarm is raised. At Mode, the desired
scenario can be selected, which can be one of the
following:
-
Min/max will raise an alarm when the
sensor signal is out of the limits set by
the Minimum and the Maximum value
in percent of the full scale capacity.
-
Reponse will raise an alarm when the
measure of a controller is out of limits
around the setpoint. The limits in
percent of the full scale capacity can be
set at Min and Max.
-
Power-up will raise an alarm when the
instrument is powered-up, e.g. after a
power loss.
To avoid excessive alarms, a Delay time can be set to
delay the alarm event. If the condition for the alarm is
met shorter than this delay time, the alarm is not
raised.
When the alarm is raised, it is possible to
automatically change the setpoint to another value.
The new value can be entered at New setpoint and the automatic setpoint change will be effective when the
checkbox Setpoint change on alarm is checked.
Page 17
FlowPlot
9.17.030