Sensor filter, Sensor zero, 6 controller settings – Bronkhorst FlowPlot User Manual
Page 14: Valve curve correction, Pid settings, Controller settings
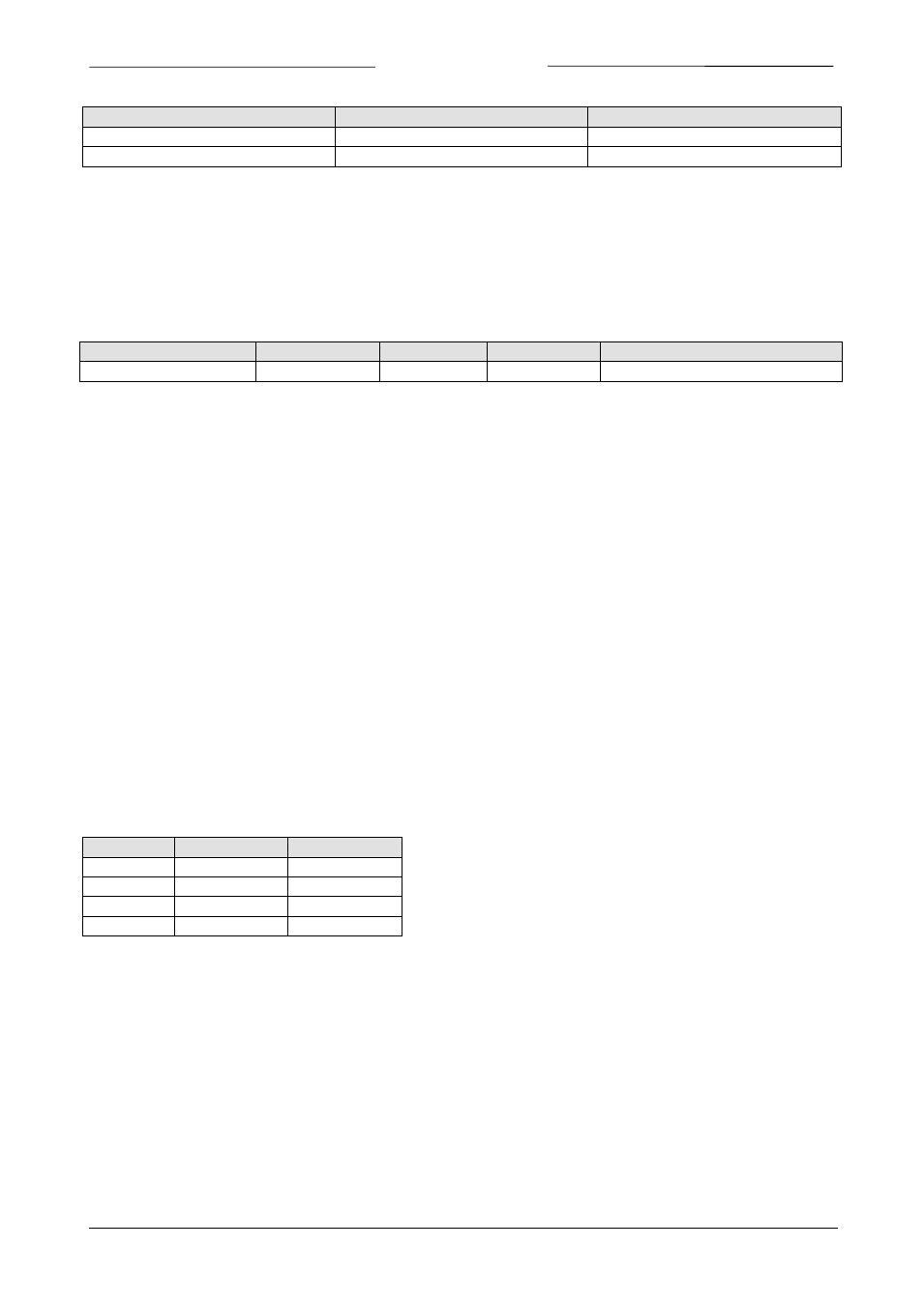
BRONKHORST
®
Factor
Responses >= 2 seconds
Responses < 2 seconds
Dynamic display factor
1.00E-3
3.00E-3
Static display factor
1.00E-2
2.00E-2
Sensor filter
The Exponential smoothing factor is used to filter the signal from the sensor circuitry before it is further processed.
For EL-FLOW types of instruments, this will be the ‘slow’ (not-differentiated), non-linearized sensor signal. Only in case
of much noise on the sensor signal, filtering needs to be enabled and another value than 1.0 should be used. It is
advised to keep this value above 0.8, so the sensor response is not slowed down to much. The default setting of 1.0
will do in most circumstances. For CORI-FLOW instruments, the table below shows some advised values.
Factor
Slow responses
Normal resp.
Fast reponses
Very fast resp.
Exponential smoothing
0.05
0.1
0.2
0.5 to 1.0 (not advised)
Sensor zero
Pressing Auto zero will perform an automatic zero action at the sensor bridge circuitry. It will adjust the potmeter
and/or zero scale factor setting to ensure the sensor output is zero at no flow. Before using this action, make sure
instrument has warmed-up for at least 30 minutes and that there has been, and is, no flow.
2.6.6
Controller settings
Valve curve correction
The valve curve correction is an extra amplification of the signal to the valve in a certain area. The valve curve
correction can be used to neutralize the influence of the valve non-linearity on the controller response. Especially pilot
valves respond slowly on low level setpoint steps, e.g. 5% to 10%, and fast on e.g. 80% to 100%.
The curve correction consists of two values: Factor and Signal. The first is the correction factor for speeding-up the
controller output. The second value is the percentage of sensor signal where this factor turns to one. The speed-up
factor will turn from the correction factor to one as function of a second grade polynomial, which is an approximation
of the valve curve.
The curve correction may also be used to speed-up the controller when opening from zero (e.g. for F-201C
instruments). The valve curve correction will influence the output of the controller. The curve correction will linearize
the controller output until the percentage where amplification becomes (almost) constant (for larger percentages the
correction factor is one (no correction)). Factor/ratio between low and high amplification can be filled in. The values
can be entered directly. The curve correction can be disabled entering the values 1.0 and 1.
Valve type
Advised factor Advised signal
001
1.0
1
002
5.0
30
003
5.0
30
004
4.0
50
PID settings
PID-Kp, PID-Ti and PID-Td can be used to adjust the controller speed. Set PID-Kp to a fixed value (e.g. 1 or 10), then
adjust PID-Ti until controller is fast without overshoot. Finally, increase PID-Kp until the controller is fastest without
overshoot. Advised setpoint step for tuning is 20%-80%-20%-80%, etc.
Page 14
FlowPlot
9.17.030