4 setpoint controller, 5 basic settings, Identification – Bronkhorst FlowPlot User Manual
Page 13: Fluid settings, Output filter, Setpoint controller, Basic settings
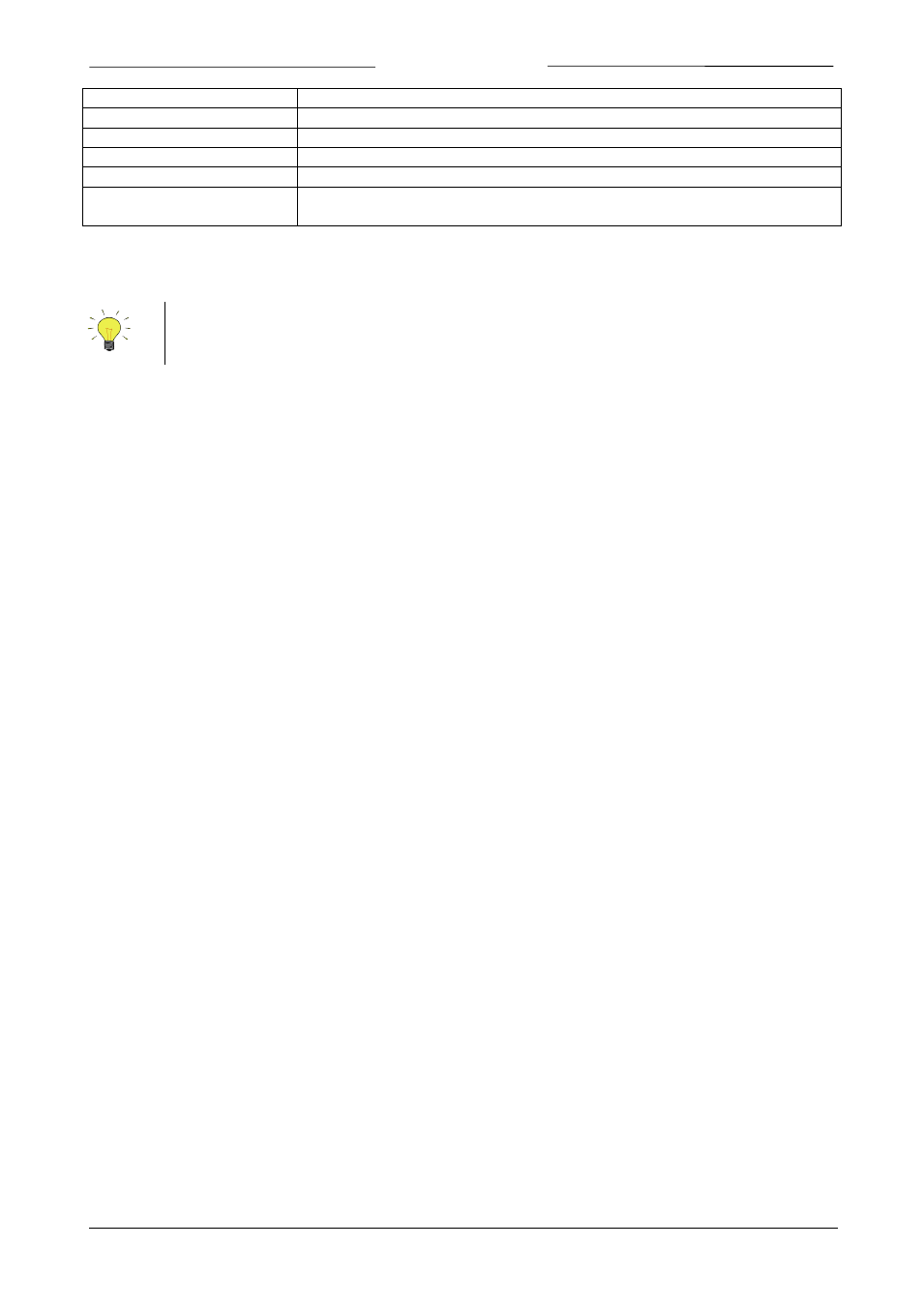
BRONKHORST
®
0 – Bus/RS232
Digital setpoint via fieldbus or RS232
1 – Analog input
Setpoint via analog input
3 – Valve fully closed
Valve fully closed and stays closed under all circumstances
8 – Valve fully open
Valve fully opened (purge) and stays opened under all circumstances
11 – Keyboard & FLOW-BUS
Setpoint via E-7000 keyboard, bus or RS232
18 – RS232
Digital setpoint via RS232 neglecting safe state (valve action when no fieldbus
communication present)
For convenience the actual readings of Measure and Valve out of the instrument are shown in percent of maximum
calibrated value and in direct reading.
More detailed information about control modes can be found in document no. 9.17.023.
2.6.4
Setpoint controller
At the Setpoint controller field FlowPlot enables the user to send setpoints to another instrument than the instrument
selected at Channel & Control mode. This can be useful when the connected instrument is not a controller, but a
meter only. It is also possible that this separate controller is connected via another instance of FlowDDE (FlowDDE2 or
vice-versa). The combo box at DDE server will be enabled as soon as FlowPlot determines that there are two FlowDDE
servers running.
Using channel enables the user to connect to a channel of the DDE server. Use the configuration window of the
specific FlowDDE to determine on which channel the instrument can be reached.
At Select setpoint several setpoint steps can be given as a help for taking points for calibration. The setpoints are the
setpoints normally used by Bronkhorst High-Tech to obtain a calibration curve. Eventually use -1% or +1% buttons to
adjust the setpoints.
2.6.5
Basic settings
The Basic tab of the Instrument Settings window is shown in 2.6.1 on page 12.
Identification
The Identification frame is used to display some of the identification properties of the instrument. The Serial number
is a unique number assigned to every instrument. In addition to the serial number, a Service number is assigned to an
instrument which has been serviced by Bronkhorst. Instruments that did not return for service, mostly have this
number set to 000000.
The Model number and the Customer model show the name of the series of the instrument.
The instrument can also be identified by a customizable Usertag, which can be used to easily recognize the
instrument.
Fluid settings
This frame shows which of the eight fluidsets an instrument can contain, is currently active. At Active fluidset the
active fluidset can be easily changed. From the active fluidset, the capacity, the unit, the fluid name and the Controller
speed are shown. The Controller speed slider can be used to adjust the controller speed (it adjusts the controller
gain). The default value is 1.
Output filter
By means of a Dynamic and a Static display factor, the filter for the measured signal going out to either fieldbus or
analog output can be adjusted. The used filter can be influenced by means of a floating point value between 0 and 1.
When the value is 0, the filter is filtering maximal and will not pass any signal change at the input to the output. When
the value is 1, filtering is minimal and the output will be equal to the input signal.
The filter switches to the dynamic factor at large changes of the sensor signal (e.g. sudden pressure or setpoint
changes), while the static factor is used when sensor signal is stable (small signal changes during over time). This
behavior can offer a low-noise sensor signal to the display/output with a relatively low lag in time compared to the
real flow (or other signal). Some advised values are given in the table below.
Page 13
FlowPlot
9.17.030