Response settings, Valve powers – Bronkhorst FlowPlot User Manual
Page 15
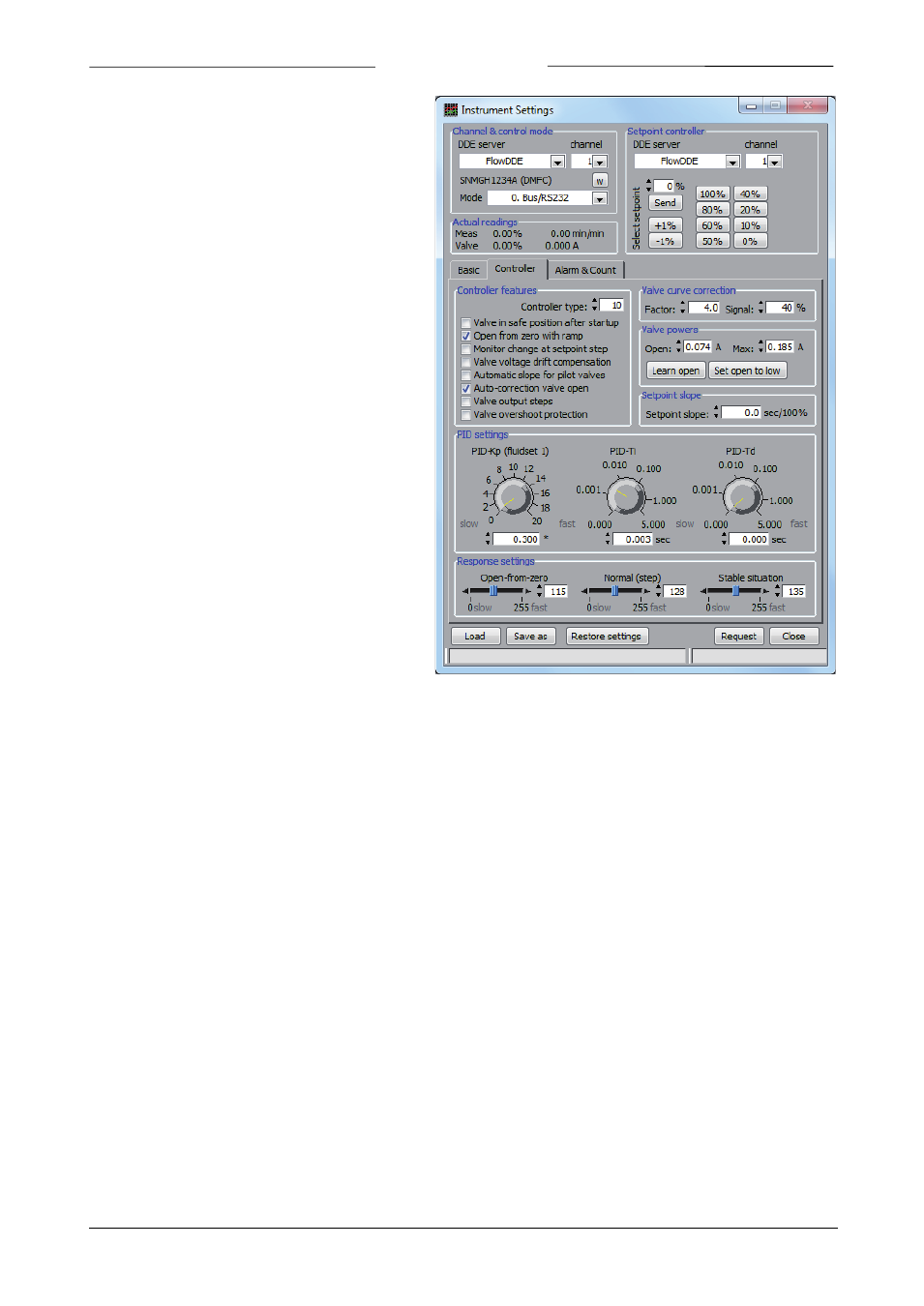
BRONKHORST
®
PID-Td is only used if the volume between the
sensor and valve is relatively large (e.g. when the
sensor and valve are mounted away from each
other).
Settings may be changed by means of
potentiometers between (common) minimum and
maximum values. It is also possible to enter value in
the text box directly, even out of the minimum-
maximum range.
Response settings
The valve output at setpoint steps from zero will go
through several stages:
-
Setpoint is zero: no action.
-
Setpoint larger than zero and measure
is still zero: the first step of the valve
output is the Valve open
voltage/current minus a safety margin
or valve output via a ramp or via PID
controller until the measure is above
2%. The initial action depends on the
controller features setting.
-
Measure differs more than 2% from
setpoint: normal situation, PID
controller is normally active.
-
Measure differs less than 2% from
setpoint for a short time: stable
situation for controller.
The last two stages are valid for all other setpoint
steps as well.
The response settings influence the controller gain by a factor depending on the stage the controller is in. The extra
factor influences the controller gain as follows, in which a setting of 128 has no effect:
total controller gain = Controller speed * PID-Kp * 1.05
(response setting – 128)
Response settings, three different stages:
-
Open from zero will influence the PID controller speed or ramp size (depends on controller features
setting) when valve is opening from 0%. Its advised value is lower than 128 to prevent overshoot. It’s
value also depends on the used valve curve correction.
-
Normal (step) is used at each setpoint step larger than 2%, not coming from 0%. Actually the measure
differs more than 2% from the setpoint in this situation. Its value should always be 128. Use this function
only in special cases; preferably adjust the PID-Kp value (factory) or the controller speed (customer) value
to adjust the overall controller speed.
-
Stable situation is when the measure differs less than 2% from the setpoint for a short time. Depending
on the situation, the value can be a bit higher or lower than 128, but should usually be between 118 and
138.
Valve powers
The value in the textbox Open is the voltage or current the valve output will get immediately after a setpoint step has
been given when actual setpoint was 0% (first step). From that point on, the valve output will be increased by a ramp
function or by the PID-controller. For current controlled instruments, the values in amperes will be the correct value,
whereas for values in volts (DC) it is only an approximation.
The button Set to low will set the Open value to a safe low voltage or current. For current-driven NC valves, this will
be 0.040 A, and for voltage-driven valves it depends on the maximum supply voltage to the valve:
-
2.5 V in case of a 15 V NC valve.
-
4.0 V in case of a 24 V NC valve.
Page 15
FlowPlot
9.17.030