Controller features – Bronkhorst FlowPlot User Manual
Page 16
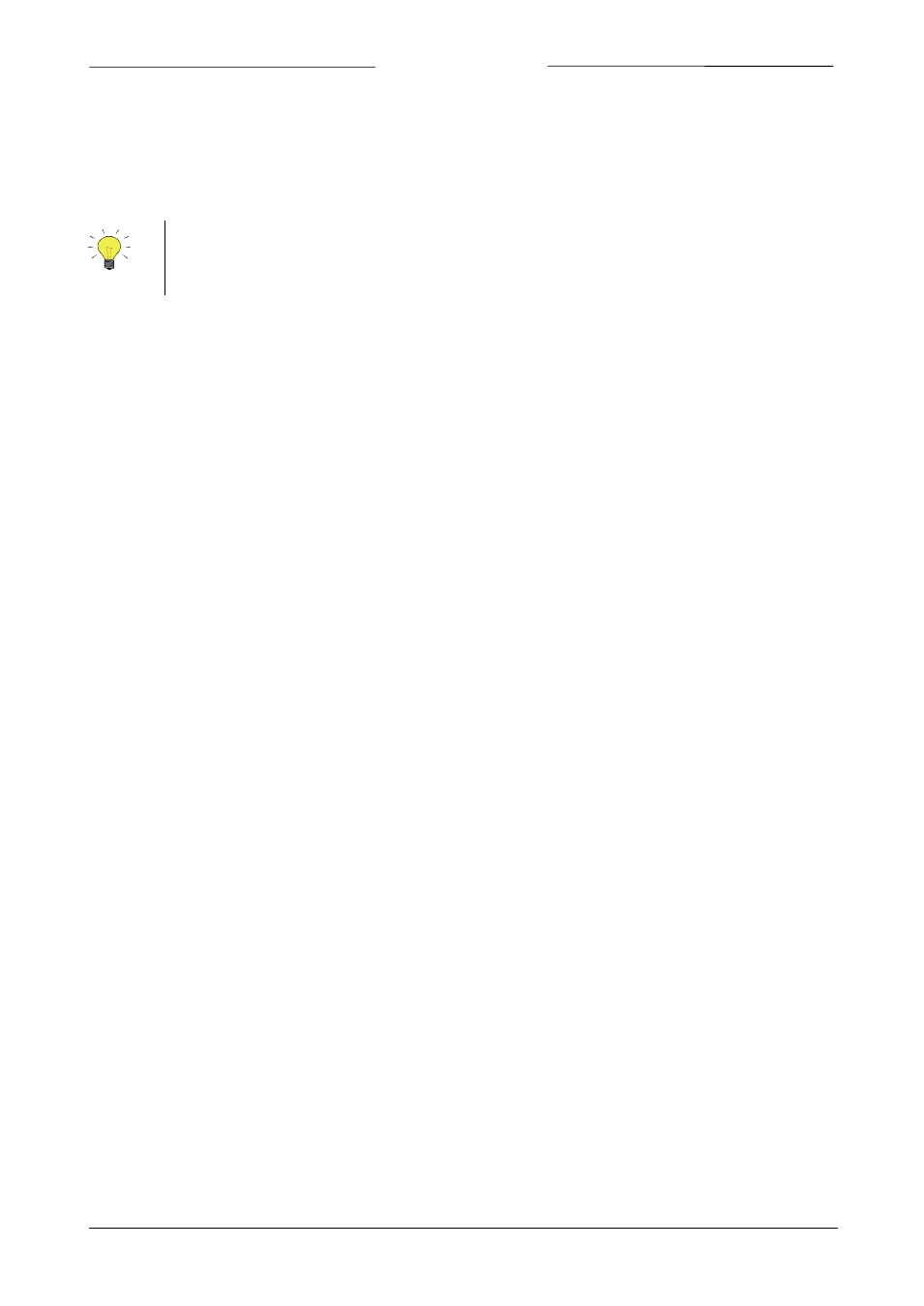
BRONKHORST
®
The actual valve open voltage or current may be determined automatically once by pressing the button Learn and
store. A setpoint step will be needed for this, so be sure to supply the correct pressure to the instrument before doing
this.
The maximum valve current can be changed in the Max box. The valve current will not exceed this value. Setting the
maximum valve current too low may result in the controller not to reach its maximum setpoint, however in this case
the valve heats a lot in case of zero pre-pressure. For current-driven instruments, the default value is 0.200 A.
When using the buttons in this window automatic correction (learning) of valve open at controller
features should be switched off, otherwise the valve open power is overwritten the next time the valve
opens.
Controller features
Several options of the controlling algorithm can be switched on or off to obtain certain behavior. Safety and
controlling speed can be adjusted for certain events. Most options are used to make difference between fast and
slower control when opening the valve from zero. These settings go together with the valve Open voltage or current
and the Open from zero response setting.
Valve in safe position after startup means that the valve output will start at 0 the first time the instrument powers
up. This will prevent a possible first overshoot, but will take more time to open the valve.
Open from zero with ramp function will ramp up the valve output from 0 until the valve opens, instead of using the
PID-output.
In both situations the response setting for open-from-zero will influence how fast the valve output will increase from
first step until point of opening.
Monitor change at setpoint step will switch off the display filter for the measure signal during a setpoint step. Though
filter settings can be already fine-tuned to give a stable signal and a fast response, sometimes it may be useful to
switch it off temporarily. It should only be used if the measured value lags the real flow/pressure too much. When
switched on, the measured value will be equal to unfiltered fast sensor value at a setpoint step until controller is in
stable situation (i.e. the measure differs less than 2% from setpoint for some time). Then, the measured value will
become normally filtered again. Advantage of this is a very fast signal at the output measure signal (the signal which is
used for the PID-controller). Disadvantage is high level of measure noise during setpoint steps.
Valve voltage drift compensation will take into account the change in open voltage due to warming-up and cooling-
down of the valve coil. It will correct voltage drift in time for better approximation of the open point. This feature was
removed from instruments that are able to current-drive the valve (i.e. MBC2 and later).
Automatic slope for pilot valves can be used for pilot valves (e.g. types 033, 002AC, 003AC/BC) in combination with a
setpoint slope. Setpoint slope with a value of at least one second is able to improve behavior of these valves regarding
overshoots. However, this setpoint slope setting will mainly have influence when the main valve opens for the first
time. Automatic slope is able to detect when this valve opens and will use the setpoint slope only then when really
necessary. This option is to be used in combination with the Setpoint slope. The setpoint slope is defined as the
(ramp) time a setpoint will need to go from 0 to 100%. See also ‘Setpoint slope’ below.
If Auto-correction valve open is enabled, the valve open power will be determined automatically each time the valve
opens. This value (minus a safety margin) will be used by the controller next time to open the valve as fast as possible.
After an eventual overshoot the first time, the next open from zero voltage will be corrected in stable situation. Using
this option should be considered carefully. Automatic correction of the valve open voltage will always be an
approximation. Under circumstances overshoots may occur. For example when a valve coil is heated-up (after several
working hours) and valve open power will be detected at a new setpoint step coming from zero, this value will be
stored. This is fine when the valve should be opened immediately afterwards, but when the valve will be closed for a
long time before a setpoint is given, the last detected value for opening the valve may be too high, and an overshoot
may occur. Using Valve in safe position after startup builds in safety here, but only after a power-up.
When no overshoots at all are allowed, it is advised to set the valve Open by Set to low or Learn and store (determine
once right after power-up when the valve is still cool). Then, the valve will start opening from a safe value, but the
controller will need more time to open it.
Page 16
FlowPlot
9.17.030