Hanna Instruments HI 504 User Manual
Page 24
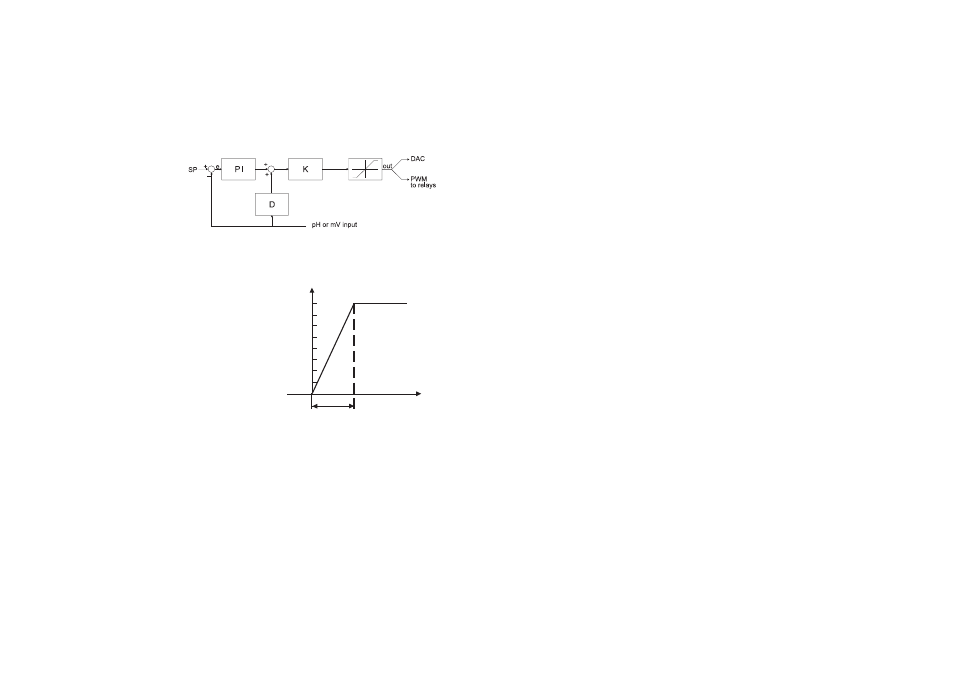
47
46
TUNING A PID CONTROLLER
The proportional, integrative, derivative terms must be tuned,
i.e. adjusted to a particular process. Since usually the pro-
cess variables are not completely known, a “trial and error”
tuning procedure must be applied to get the best possible
control for the particular process. The target is to achieve a
fast response time and a small overshoot.
Many tuning procedures are available and can be applied
to HI 504. A simple and profitable procedure is reported in
this manual and can be used in almost all applications.
The user can vary five different parameters, i.e. the setpoint
(S1 or S2), the deviation (D1 or D2), the reset time, the rate
time and the proportional control mode period T
c
.
Note
User can disable the derivative and/or integrative action (for
P or PI controllers) by setting Td = 0 and/or Ti = MAX (Ti)
respectively through the setup procedure.
SIMPLE TUNING PROCEDURE
The following procedure uses a graphical technique of ana-
lyzing a process response curve to a step input.
Note
This procedure allows only a rough setting of the PID param-
eters and could not fit all the processes.
It is suggested that I and D parameters be set by technical
personnel, because their inadequate values may cause un-
desired behaviors of the system.
Note
Connecting an external device (chart recorder or PC) to the
controller, the procedure is easier and doesn’t need the use
of hand plotting the process variable (pH or mV).
1. Starting from a solution with a pH or mV value different
from the dosed liquid (at least a 3 pH or 150mV difference)
turn on the dosing device at its maximum capacity without
the controller in the loop (open loop process). Note the
starting time.
2. After some delay the pH or mV starts to vary. After more
delay, the pH or mV will reach a maximum rate of change
(slope). Note the time that this maximum slope occurs and
the pH or mV value at which it occurs. Note the maximum
slope in pH or mV per minute. Turn the system power off.
3. On the chart draw a tangent to the maximum slope point until
intersection with the horizontal line corresponding to the initial
PID TRANSFER FUNCTION
The transfer function of a PID control is as follows:
Kp + Ki/s + s Kd = Kp(1 + 1/(s Ti) +s Td)
with Ti = Kp/Ki, Td = Kd/Kp,
where the first term represents the proportional action, the
second is the integrative action and the third is the derivative
action.
Proportional action can be set by means of the Proportional
Band (PB). Proportional Band is expressed in percentage of the
input range and is related to Kp according to the following:
Kp = 100/PB.
The proportional action is set directly as “Deviation” in pH
and mV units respectively. Relation between Deviation (D)
and PB is:
D = Range * PB/100
Each setpoint has a selectable proportional band: PB1 for
setpoint1 and PB2 for setpoint2. Two further parameters must
be provided for both setpoint:
Ti = Kp/Ki, reset time, measured in minutes
Td = Kd/Kp, rate time, measured in minutes.
Ti1 and Td1 will be the reset time and rate time for setpoint1,
while Ti2 and Td2 will be the reset time and the rate time for
setpoint2.
Error
100%
0
Proportional Band
Controller
output