Size 048, 208v- or 230v-60-3 – Bryant 559B User Manual
Page 5
Attention! The text in this document has been recognized automatically. To view the original document, you can use the "Original mode".
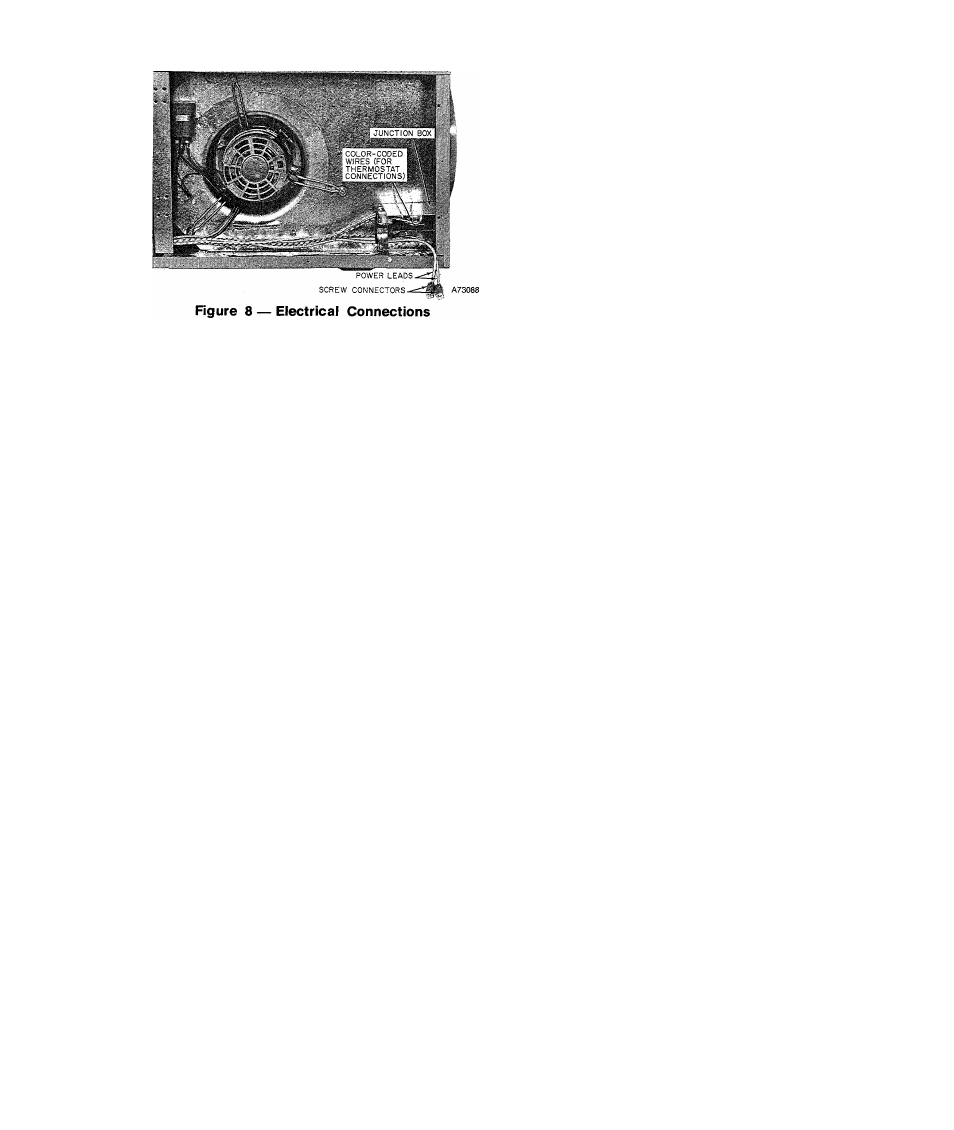
justed for proper airflow.
Recommended evaporator airflow is 350 to 450 CFM per
12,000 Btuh.
1. Set thermostat to call for cooling, thus energizing unit.
2. Measure static pressure in duct system at unit.
3. To determine airflow across evaporator coil, see Tables
III through VII.
Model 559B utilizes a direct-drive blower, factory-wired on
high-speed tap. If airflow is incorrect, blower speed can be
adjusted as follows:
1. Disconnect electric power to unit.
2. Disconnect cooling relay lead from high-speed tap
(black wire). Tape end of wire removed.
3. Refer to appropriate Air Delivery Performance Table
and connect relay lead to correct speed tap.
Blue wire med speed
Orange wire med-low speed
Red Wire low speed
4. Recheck system static pressure.
The air conditioner has been tested and factory sealed.
There is no need to check refrigerant charge. If it is
necessary to open refrigerant circuit, contact your Bryant
Distributor for proper procedure. The type and amount of
refrigerant are listed on rating plate.
Typical Sequence of Operation
Do not leave installation until unit has been observed
throughout one or two complete cycles. Installer, should
make certain during this time that all components are
operating in correct sequence. Refer to line-to-line wiring
diagrams. Figure 10 or 11. The following sequence of
operation pertains to the units shown; however, the
sequence of operation of all units is very similar.
NOTE: Although the unit wiring may vary slightly from
that shown in Figure 10 or 11, the sequence of operation
will not be affected.
Sizes 024, 030, and 036, 230V-60-1
Line voltage is supplied through terminals LI and L2 to
compressor contactor (2D) and to primary of control trans
former (lAl). An external low-voltage thermostat is con
nected across low-voltage wires R, Y, and G.
Set system switch to COOL and fan switch to AUTO on
thermostat. On call for cooling, power is supplied from con
trol transformer (lAl) through wire R, external thermostat,
wire Y, low-pressure switch (7C), and contactor holding coil
(2D) to other side of control transformer (lAl), closing con
tactor contacts (2D).
When contactor contacts (2D) close, condenser fan motor
(3C) is energized through run capacitor (4A2), starting con
denser fan. In addition, power flows through compressor
motor run capacitor (4A3), compressor start capacitor
(4Cl), start relay (2K), and compressor motor (3J), starting
compressor motor.
When cooling fan relay contacts (2A) close, power flows
through run capacitor (4A1) and blower motor (3D1)
starting blower motor.
When thermostat ceases to require cooling, it breaks circuit
between wires R and Y and wires R and G, shutting down
unit.
Size 048, 208V- or 230V-60-3
Line voltage is supplied through terminals Ll, L2, and L3
to compressor contactors (2D) and to control transformer
(lAl). An external low-voltage thermostat is connected
across low-voltage wires R, Y, and G. Set system to COOL
and fan switch to AUTO on thermostat.
On a demand for cooling by the external thermostat, power
is supplied from control transformer (lAl) through ter
minal R. Terminal R makes to terminals Y and G through
the thermostat.
As R makes to G, the coil of the cooling fan relay (2A1) is
energized, closing the fan relay contacts (2A1). Power is
now allowed to flow through blower motor run capacitor
(4A1), and the blower motor (3D1) starts.
As terminal R makes to terminal Y through the thermostat,
the coil of cooling relay (2A2) is energized, closing the
cooling relay contacts (2A2). Power is now allowed to flow
through the low-pressure switch (7C), the compressor in
ternal thermostat (7H), compressor overload contacts (8A),
and the Bryant COMPROTEC'" circuit which includès
timer motor (3M), and the coil of the holding relay (2C).
The energized coil of the holding relay (2C) closes its nor
mally open contacts and opens its normally closed contacts.
Timer motor (3M) runs through a 15-second (approx.) cy
cle. The timer motor contacts are then switched. Power is
now allowed to flow through the coil of compressor con
tactor (2D), which closes the normally open contacts of
compressor contactor (2D).
When compressor contactor contacts (2D) are closed, power
is allowed to flow through compressor overloads (8A) and
compressor motor (3L) starts. At this same time, power is
allowed to flow through low-ambient condenser fan switch
(7K), condenser fan run capacitor (4A2), and the two-speed
condenser fan motor (3D2) starts. When outdoor tem
perature drops to 85°F, low-ambient condenser fan switch
(7K) will switch contacts, energizing a lower speed of con
denser fan motor (3D2).
When the demand for cooling is satisfied, the external ther
mostat breaks the circuit between terminal R and terminals
Y and G. Breaking this circuit deenergizes compressor
holding coil (2D), cooling relay coil (2A2), and cooling fan
relay coil (2A1). The condenser fan motor (3D2), com
pressor motor (3L), and blower motor (3D1) are now
deenergized.
At the same time, the holding relay coil (2C) is deenergized,
opening its normally open contacts and closing its normally
closed contacts. Power now flows through normally closed
contacts of holding relay (2C) and timer motor (3M). In ap
proximately 4 minutes 45 seconds, the timer motor contacts
switch, breaking circuit to timer motor. The unit is now in a
“standby” position, ready for the next demand for cooling
by the external thermostat.
-
5
-