Service – Carrier 38VH User Manual
Page 9
Attention! The text in this document has been recognized automatically. To view the original document, you can use the "Original mode".
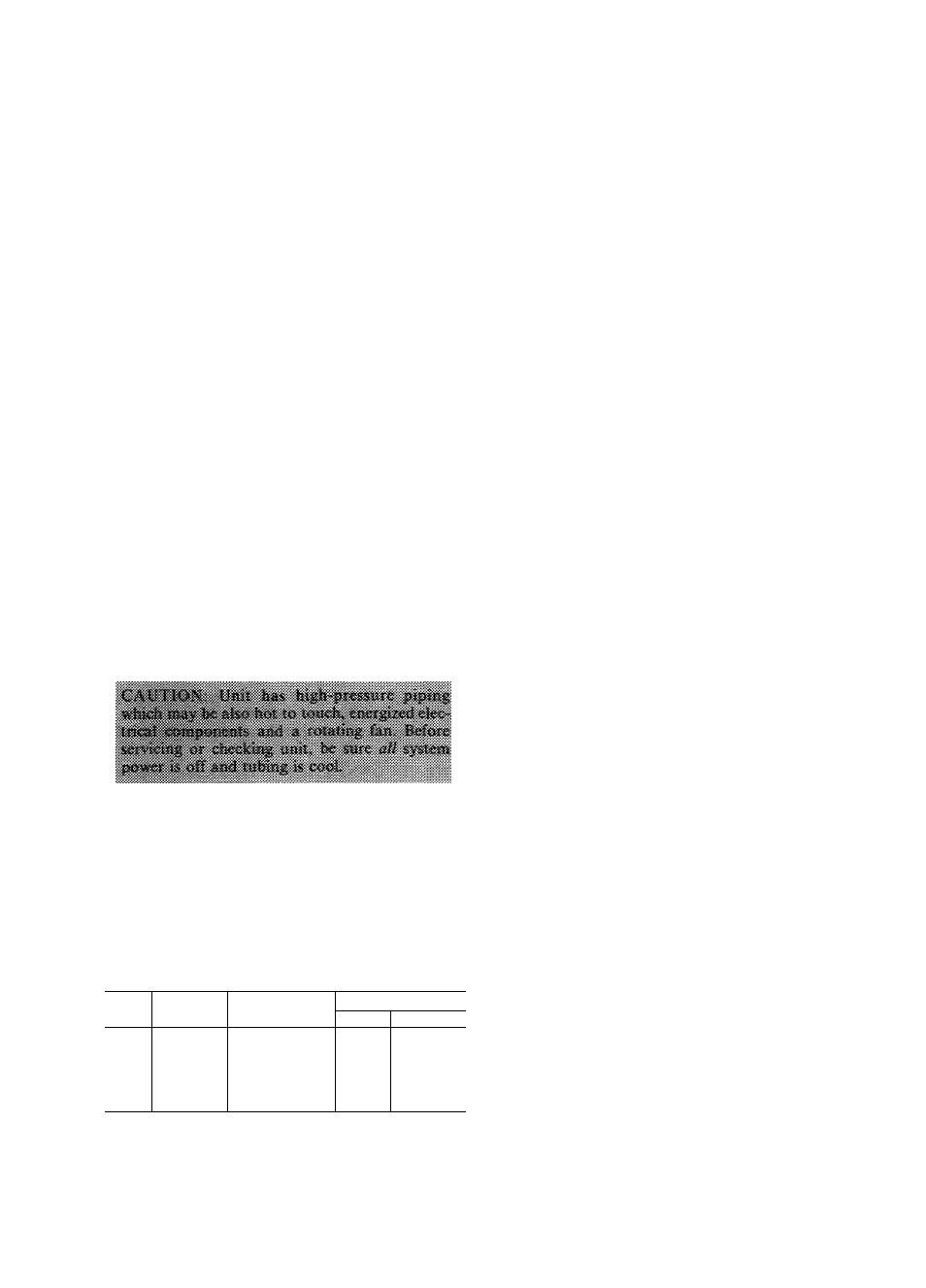
8. Add charge by slowly opening Chargemaster
valve. If necessary, reduce charge by bleeding
at liquid line service valve. Check outdoor air
and evaporator temperature during procedure.
If they change, refer back to Chargemaster
Charging Chart.
Correct use of Chargemaster ensures than an opti
mum refrigerant charge will be in system when
conditions and system components are “normal.”
However, the Chargemaster does not solve or fix
systems abnormalities. It indicates correct charge
for condition of the system. It will not make correc
tions for dirty filters, slow fans, excessively long or
short suction lines or other abnormal conditions.
This charging device ensures that a correct relation
ship exists between outdoor temperature, evap
orator temperature, and suction line temperature
on a specific system.
SIGHT GLASS METHOD — (Field-supplied sight
glass installed in liquid line.) A satisfactory oper
ating charge can be obtained on thermal expansion
valve systems only by charging to a clear sight glass.
For optimum charge, increase high-side pressure
to 380 ± lOpsig by blocking condenser fan dis-
eharge or air entering condenser. Charge to a clear
sight glass while holding constant high-side pres
sure. For peak efficiency, adjust charge to yield a
liquid refrigerant temperature at the evaporator
that is approximately the same as outdoor dry-bulb
temperature.
SERVICE
Compressor Removal
— See Table 9 for com
pressor information and Fig. 6 for component
location. Shut off power to unit. Remove refrig
erant from unit using refrigerant removal methods
described in Carrier Standard Service Techniques
Manual, Chapter 1, Refrigerants.
Follow safety codes. Wear safety glasses and
work gloves. Have quenching cloth available.
Table 9 — Compressor Data
UNIT
38VH
V/PH
PRODUCTION
COMPRESSOR*
OIL RECHARGE (oz)t
Typical
Additional
001
208-230/1
ÂH8520E J
/
0 25
^ 002
208-230/1
CRB1-0175-PFV
J/ 51
05
003
208-230/1
CRFI-0250'PFV-^
/
05
004
208-230/1
CRH1-0275;PFVv
1
05
045
208-230/1
AH8543E J ,
42
05
005
230/1
PC5016BD y
72
1 0
•Refer to Carrier Service Parts Catalog for replacement com
pressor model numbers
f'Typical ' refers to systems having refrigerant piping up to 50 ft
long Where piping exceeds 50 ft add additional quantity of oil
shown for e a c h 10 ft beyond 50 feet
2
.
1. Turn off power to unit. Failure to do so may
result in electric shock. Open door and remove
top access panel if so equipped. See Fig. 6.
Remove unit top cover. Remove 6 screws
holding fan motor orifice assembly in place.
Lift assembly and position it near unit being
careful not to strain fan motor ends.
3. Compressor sound shield is snapped together.
Undo those snaps which are under piping
connections, then lift the assembly off the
compressor.
4. Remove compressor terminal box cover. Dis
connect and remove compressor power leads.
5. Be sure refrigerant has been removed so that
system pressure is 0 psig.
6. Using a tubing cutter, cut suction and discharge
lines at convenient place near compressor to
allow easy reassembly to new compressor by
using field-supplied copper coupling connected
at these points.
M
iumy
a break
7. Remove compressor hold-down bolts. Lift out
compressor thru front of unit.
8. Carefully unbraze suction and discharge line
piping stubs from compressor. If oil vapor in
piping stubs ignites, use quenching cloth.
9. Braze piping stubs (removed in Step 7) onto new
compressor.
10. Install new compressor in unit. Have fire ex
tinguisher and/or quenching cloth available in
case oil vapor ignites. Braze suction and dis
charge lines to compressor piping stubs (at
points where cut, Step 6) using field-supplied
copper couplings. Replace compressor hold
down bolts. Reconnect wiring.
11. Clean system. If a compressor failure was
caused by a major motor-winding burnout,
contaminants (burnout by-products) can cause
future system operating problems if left in
system. Install a filter-drier in the suction line
near the compressor. Also install a drier in the
liquid line ahead of the refrigerant control
device. Run unit for 48 hours to remove con
taminants. Remove suction line filter-drier
and liquid line drier. Discard both driers.
Clean AccuRater™ refrigerant control as de
scribed in evaporator installation instructions.
Install new liquid line filter-drier. If burnout
was minor, install or replace liquid line filter-
drier, run for 48 hours, then discard filter-drier.
Install new filter-drier.