Carrier 38GP User Manual
Page 9
Attention! The text in this document has been recognized automatically. To view the original document, you can use the "Original mode".
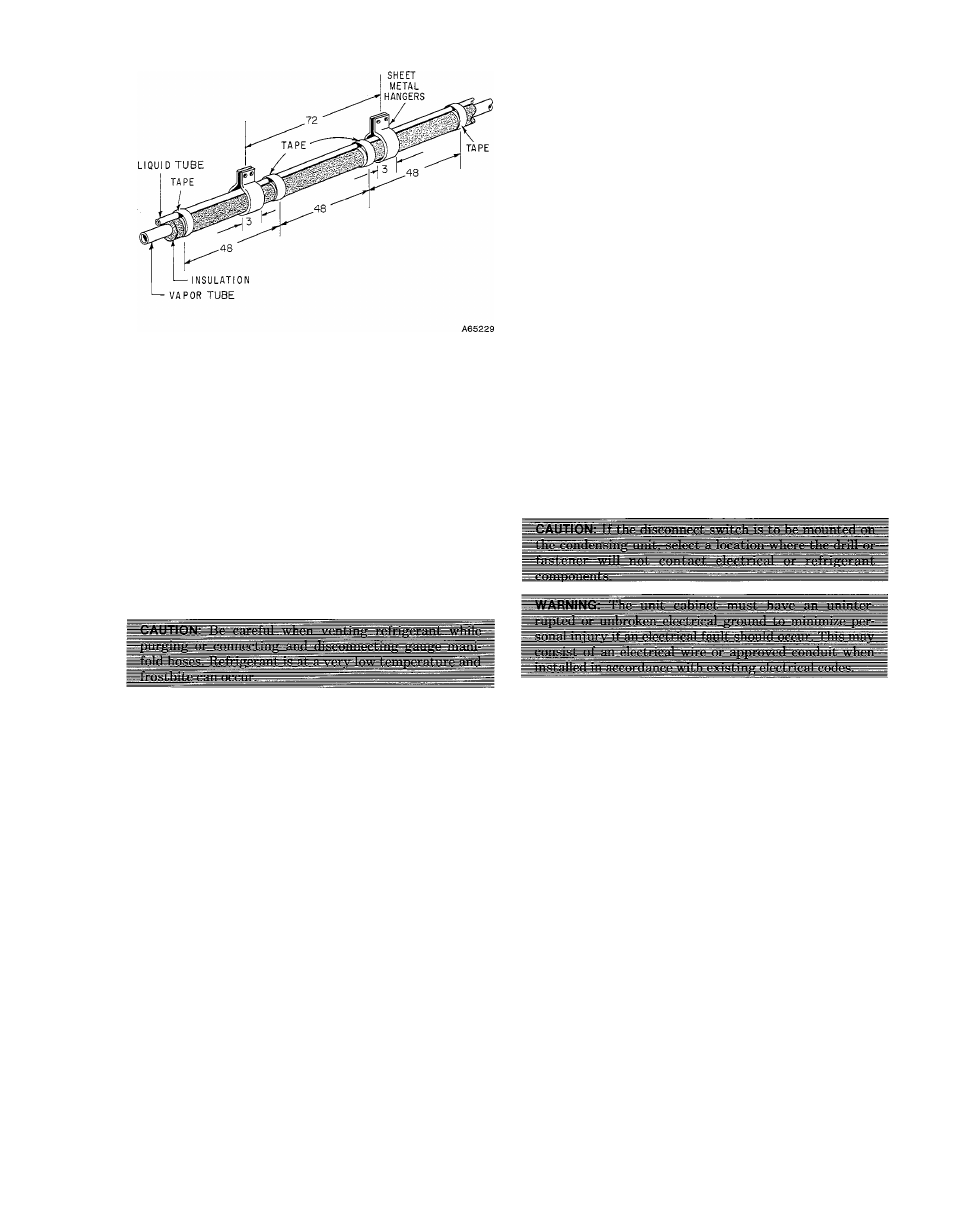
and remove gauge manifold. Replace caps on gauge
ports and valve stems. Be sure they are tight!
IV. PURGING
If either the refrigerant tubing kit or the evaporator coil is
exposed to atmospheric conditions during installation for
longer than 5 minutes, the refrigerant tubing and the evapo
rator con must be purged.
NOTE:
DO NOT USE THE UNIT CHARGE TO PURGE
THE REFRIGERANT TUBING. To purge the refrigerant
tubing and the evaporator coil, proceed as follows:
1. Disconnect hose from low side of gauge manifold.
2. Open valves on R-22 refrigerant cylinder and high side
of gauge manifold. Allow approximately 1/2 to 1 pound
of refrigerant vapor to flow through system and out
hose attached to gauge port on suction service valve.
3. Pressurize system with refrigerant to 10 psig and close
valves on refrigerant cylinder and gauge manifold.
Reattach hose to low side of gauge manifold.
4. Open (Turn counterclockwise.) both service valves.
Remove gauge manifold from gauge ports of service
valves and replace valve stem and gauge port caps (Be
sure they are tight.) if system is to be left in the purged
condition, it wiU not be necessary to remove gauge
manifold if checking charge procedure is to follow.
V. EVACUATION
It is extremely important to have an installation in which
aU refrigerant tubes and system components are completely
free of air and moisture. If, during the installation, the
refrigerant tubing kit or the evaporator coil becomes con
taminated with moisture or liquid water, or other than
matching components are used; the refrigerant tubes and
evaporator coü must be evacuated.
If the installer can pull the system down to a reading of
1000 microns or less with his deep vacuum equipment, he
can consider the system free of air and moisture when this
level is reached.
If, however, the installer has an evacuation pump (one
which will only pull a vacuum of approximately 28 inches)
rather than a deep vacuum pump, he must triple-evacuate
the system with the required number of purges and holding
periods. The initial preparation for evacuation of the refrig
erant tubing and evaporator coil is as follows:
1. Connect evacuation equipment to system through
gauge manifold.
2. Evacuate system, following appropriate steps for type
of evacuation equipment used.
3. Pressurize system with refrigerant to 10 psig and open
(Turn counterclockwise.) both service valves.
4. Remove gauge manifold. Replace valve stem and gauge
port caps on both service valves (Be sure they are
tight.) if system is to be left in evacuated condition. It
wfll not be necessary to remove gauge manifold if
checking-charge procedure is to follow.
VI. ELECTRICAL CONNECTIONS
IMPORTANT: Before proceeding with the electrical con
nections, make certain that the volts, hertz, and phase cor
respond to that specified on the unit rating plate. Also,
check to be sure that the service provided by the utility is
sufiicient to handle the additional load imposed by this
equipment. Refer to the Ratings and Performance table in
the detailed unit instruction and unit rating plate for equip
ment electrical requirements.
The attached wiring diagrams show the proper field high-
and low-voltage wiring. Make all electrical connections in
accordance with the National Electrical Code and any local
codes or ordinances that might apply.
Use a separate branch electrical circuit for this unit. A dis
connecting means must be located within sight of, and
readily accessible to, the unit.
NOTE:
We require the use of copper wire between the dis
connect switch and the unit. Whenever aluminum wire is
used in the branch circuit wiring with this unit, adhere to
the following recommendations: Connections must be made
in accordance with the National Electrical Code, using con
nectors approved for aluminum wire. The connectors must
be UL approved (marked Al/Cu with the UL symbol) for the
application and wire size. In preparing the wire, just before
installing the connector, all aluminum wire must be “brush-
scratched” and coated with a corrosion inhibiter such as
Pentrox A. When it is suspected that the connection wfll be
exposed to moisture, it is very important to cover the entire
connection completely to prevent an electrochemical action
that will cause the connection to fail very quickly. Do not
reduce the effective size of wire, such as cutting off strands
so that the wire wfll fit a connector. Proper size connectors
should be used.
If aluminum conductors are to be used, the wire size
selected must have a current capacity not less than that of
the copper wire specified, and must not create a voltage
drop between the service panel and the unit in excess of 2%
of the unit rated voltage.
Check all electrical connections (both factory and field) for
tightness. This should also be done after the unit has
reached operating temperatures, especially if aluminum con
ductors are used.
MR. E L E C T R I C I A N , P L E A S E N O T E : D O N O T
ATTEMPT TO OPERATE THIS CONDENSING UNIT
—9—