Carrier 38GP User Manual
Page 8
Attention! The text in this document has been recognized automatically. To view the original document, you can use the "Original mode".
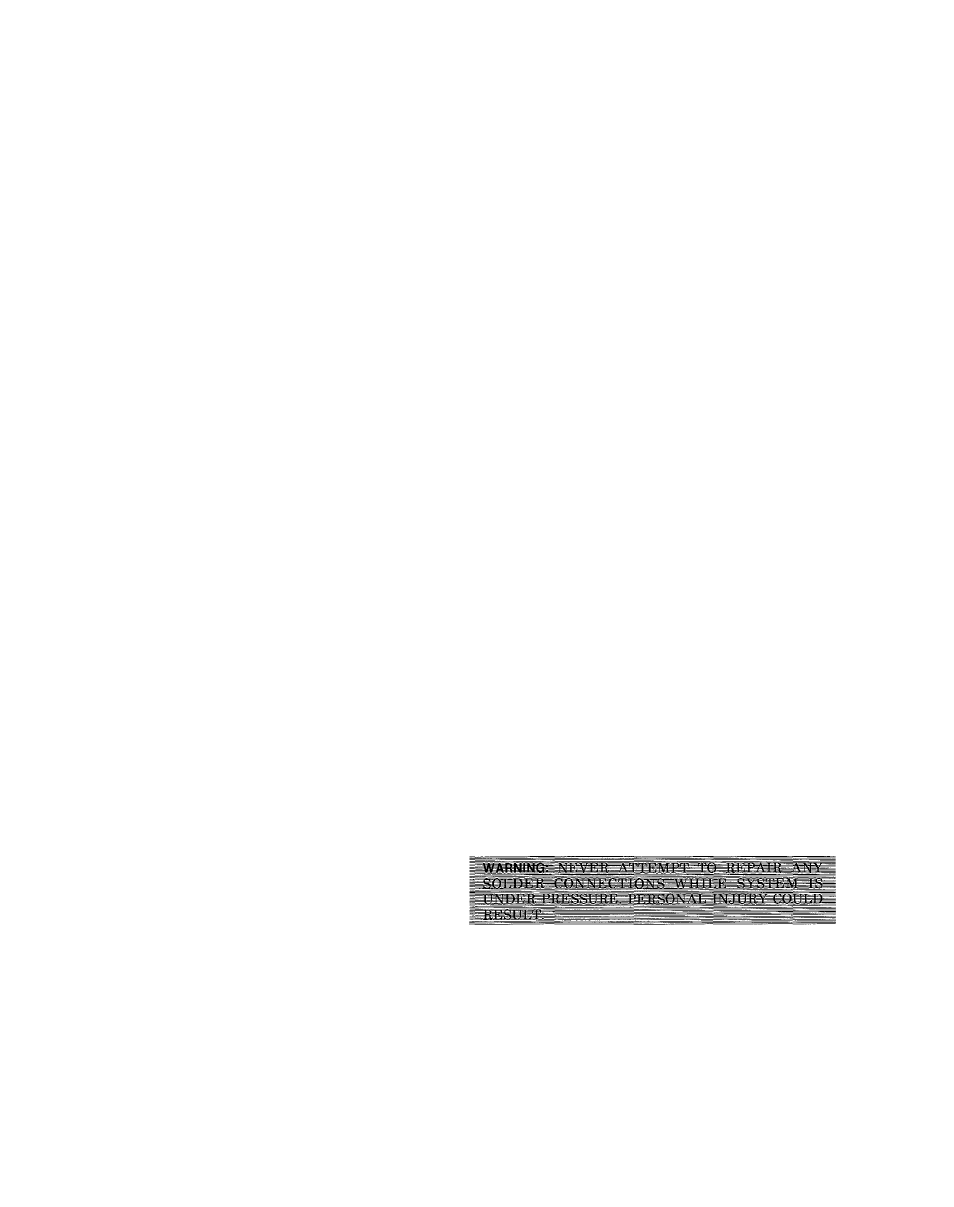
tionable, consideration should be given to a shielding
barrier. Consult your Distributor or the current pubh-
cation of ARI Standard 270 for assistance in determin
ing a suitable location with minimum of operating
sounds.
8. Keep distance between evaporator coil and condensing
unit as short as possible.
9. Consult your Distributor regarchng roof-mounted con
densing units on multilevel buildings.
OPENING AND CLOSING OF VALVES
1. Use correct tool.
2. Remove valve stem cap.
3. Front-seat—turn clockwise until valve stem bottoms.
Do not overtighten.
4. Open—turn counterclockwise until stem just contacts
snapring in valve body. Do not overtighten.
5. Replace valve stem cap and be sure that it is tight.
II. INSTALLING REFRIGERANT TUBES
IMPORTANT: The condensing unit is charged at the fac
tory. Be sure both service valves are front seated (turned
clockwise) to avoid loss of the charge. DO NOT REMOVE
REFRIGERANT TUBE CONNECTION SEALS FROM
THE CONDENSING UNIT, THE MATCHING EVAPO
RATOR COIL, OR THE REFRIGERANT TUBING,
UNTIL READY TO MAKE THE ACTUAL CONNEC
TION AT THE POINT OF SEAL.
If either refrigerant tubing or evaporator coil is exposed to
atmospheric conditions for longer than 5 minutes, they
must be purged. See Section IV, “Purging,” for the proper
method.
If other than matched refrigerant tubing is used, select an
approved (type-L) refrigerant tubing of the correct size.
(DO
NOT USE WATER TUBING.)
Flare this tubing, using a stand
ard 45-degree SAE flaring tool. Insulate the suction tube
with an insulation having an adequate vapor barrier (e.g.
Armaflex or Ensolex). It wiU be necessary to evacuate this
tubing and evaporator cod. See Section V, “Evacuation,”
for proper method.
NOTE:
All refrigerant tube joints erected on the premises
should be exposed to view for visual inspection and leak
testing before being covered or enclosed.
When a complete system (condensing unit, refrigerant tub
ing, and evaporator cofl.) is used, a filter-drier is not required
in the system. However, if other than matched refrigerant
tubing or coils are used, or if the refrigerant tubing or coil is
exposed to atmospheric conditions for longer than 10 min
utes; a filter-drier must be installed in the system at the coil.
(An appropriate size of filter-drier is available from your
Distributor.)
NOTE;
Additional refrigerant must be added to the system
and compensate for the additional volume of the filter-drier,
and different tubing lengths.
Install refrigerant tubes as follows:
1. Consult local codes or ordinances before running refrig
erant tubes.
2. Install evaporator coil in accordemce with instructions
packaged with coil.
3. If evaporator coil requires thermal expansion valve,
obtain proper valve from your Distributor and install
in accordance with instructions packaged with evapo
rator coil.
4. Run refrigerant tubes as directly as possible, avoiding
unnecessary turns and bends.
5. Tape liquid tube to top of insulated suction tube for
support. See Figure 3.
6. Suspend refrigerant tubes so they do not damage insu
lation on suction tube and do not transmit vibration to
structure. See Figure 3. Also, when passing refrigerant
tubes through wall, seal opening so vibration is not
transmitted to structure. Leave some slack in refriger
ant tubes between structure and unit to absorb
vibration.
7. If refrigerant tubes are too long, they should be rolled
into loop and placed in horizontal plane with end leav
ing loop going to compressor, coming out of bottom. If
desired, excess may be cut off and tubing braised.
8. Be sure both service valves are front seated (turned
clockwise). It is necessary to remove valve stem caps to
check.
9. When required, connect filter-drier (available from your
Distributor) in hquid tube at evaporator coil.
NOTE:
The flow directional arrow, located on the label of the
filter-drier, must point toward the evaporator coil.
10. Connect tubing to condensing unit and evaporator coil,
as shown in Figure 2. DO NOT REMOVE SEALS
UNTIL READY TO MAKE THE ACTUAL CON
N E C T I O N S A T P O I N T W H E R E S E A L I S
REMOVED.
11. Refrigerant tubing and evaporator coil is now ready for
leak testing.
III. LEAK TESTING
No installation is complete until the entire system has been
checked for leaks. This check should include aU field and fac
tory joints. To check a system for leaks, proceed as follows:
1. Remove valve stem caps from both service valves and
check to be sure valves are front seated (turned clock
wise). Remove gauge port caps.
2. Attach gauge manifold to ports on service valves.
Hoses of gauge manifold must have valve core
depressors.
3. Pressurize evaporator coil and interconnecting refriger
ant tubing with vapor from an external refrigerant cyl
inder of R-22 until system and cyUnder pressures are
equalized.
NOTE:
NEVER USE A UNIT CHARGE FOR LEAK
TESTING.
4. Leak-test with electronic detector, halide torch, or
hquid-soap solution.
5. Release pressure and repair any leaks found. Repeat
leak test as necessary.
When system is free of leaks, proceed as follows:
If system is to be purged, leave service valves in
front-seat position. Leave gauge manifold attached
to system and proceed to Section IV.
If system is to be evacuated, leave service valves in
front-seat position. Remove refrigerant cylinder
from gauge manifold and proceed to Section V.
If system is to be started and the checking charge
procedure is to follow, open (counterclockwise) both
service valves. Then proceed to step 3, Section VII.
If system is to be left in the leak-tested condition,
open (Turn counterclockwise.) both service valves
a.
b.
c.
d.
—8—