Checkout list – Carrier 38GP User Manual
Page 10
Attention! The text in this document has been recognized automatically. To view the original document, you can use the "Original mode".
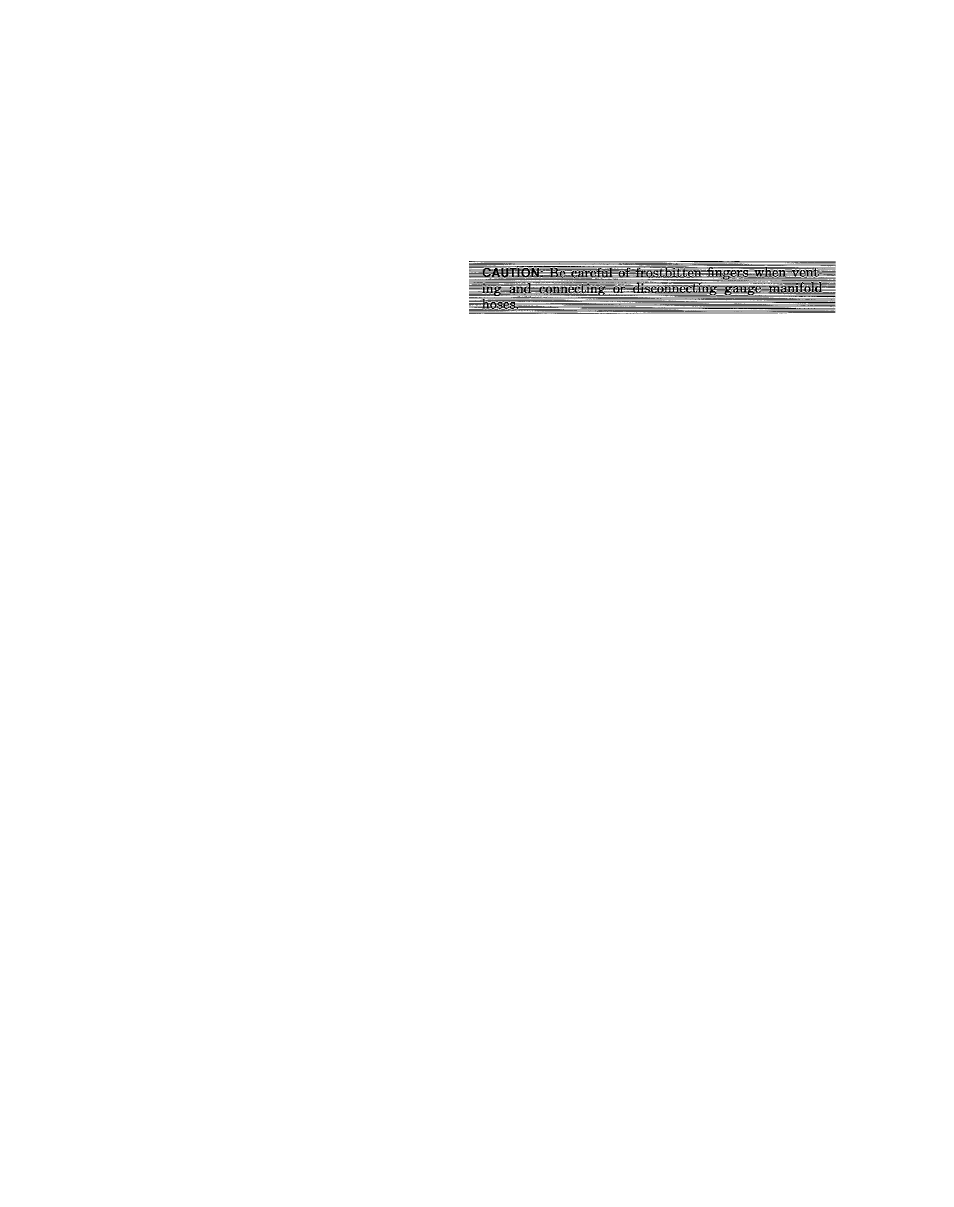
UNTIL ALL REFRIGERANT CONNECTIONS HAVE
BEEN MADE AND BOTH SERVICE VALVES HAVE
B E E N C H E C K E D F O R T H E O P E N P O S I T I O N .
(TURNED COUNTERCLOCKWISE.) IT IS NECESSARY
TO REMOVE THE VALVE STEM CAPS TO CHECK.
The single-phase compressor motor used in this condensing
unit may be a permanent-spht-capacitor-tj^e (PSC) motor,
designed to start under low-load conditions only; therefore,
make sure that the system pressures have equahzed before
attempting to start the unit: this takes approximately 3
minutes. Do not short-cycle the unit with the thermostat or
disconnect, as this will cause the compressor to tripout on
overload. For starting under most load conditions, an
optional starting kit is available from your Distributor.
VII. CHECKING CHARGE
No installation is complete until the operating charge level
of the unit is checked. The level of refrigerant operating
charge will determine how efficiently and economically the
unit wiU operate. An overcharged or undercharged unit wiU
lead to insufficient cooling, high operating costs, and the
possibihty of a compressor failure. To check the refrigerant
charge level, proceed as follows:
1. Remove valve stem caps from both service valves and
check valve stems for open position (counterclockwise).
2. Remove gauge port cap from both service valves and
attach gauge manifold. Purge gauge manifold and
hoses.
3. Start unit and allow it to run until operating conditions
stabihze and pressures level out.
4. Evaluate system performance and refrigerant charge
level by determining following information:
a. Low-side pressure gauge reading.
b. Dry-bulb temperature of inlet air at condenser coil.
c. Wet-bulb temperature of inlet air at evaporator coil.
This may be read at central return-air grille.
d. Liquid- or suction-tube temperature at respective
service valve.
NOTE:
Use an accurate superheat, thermocouple, or
thermistor-type thermometer.
e. Compare these readings to those fisted on Unit
Charging Label located on unit. Add or remove
refrigerant as required.
NOTE:
The suction-tube connection of the compressor must
be as cool as the suction tube, and the compressor base
should be warm.
5. When correct refrigerant charge level is obtained,
remove gauge manifold.
6. Replace valve stem and gauge port caps. (Be sure they
are tight.)
NOTE:
Where applicable, stamp the total number pounds of
refrigerant charge onto the rating plate in the space
provided.
VIII. ADJUSTING CHARGE
If, after checking the operating charge level, the unit is
found to be undercharged or overcharged, refrigerant may
be added or removed through the gauge manifold and the
suction service valve.
To add refrigerant to a unit, proceed as follows:
1. Connect clean, dry cylinder of R-22 to center port con
nection of gauge manifold. Purge hose and connect
gauge manifold to service valves.
2. With refrigerant cylinder in upright position, open
valve on cylinder and slowly open valve on low-pres
sure gauge of manifold. Add refrigerant in vapor form
until proper amount has been added.
3. When correct refrigerant charge level is obtained, close
valves on refrigerant cylinder and gauge manifold.
4. Remove gauge manifold from service valves. Replace
valve stem and gauge port caps. (Be sure they are
tight.)
To remove refrigerant from a unit, proceed as follows:
1. Slowly open valve on low-pressure gauge side of mani
fold and vent refrigerant (slowly) through center port
connection of gauge manifold.
2. When desired amount of refrigerant has been removed
to obtain correct refrigerant charge level, close valve on
low-pressure gauge side of manifold.
3. Remove gauge manifold from both service valves.
Replace both valve stem and gauge port caps. (Be sure
they are tight.)
CHECKOUT LIST
WITH ELECTRIC POWER OFF:
1. Check all electrical wiring (both factory and field) for
completeness and tighten all electrical connections
(contactor, capacitors, relays, etc.).
2. Check condenser fan blade for proper insertion depth in
orifice plate.
3. Check evaporator blower puUey and motor pulley (belt-
drive units only) for proper belt alignment and tight
ness. (Should have 1 in. of sag with normeil finger
pressure.)
4. Tighten all setscrews (evaporator blower, blower pul
ley, motor sheave, and condenser fan blade).
5. Check condenser airflow for obstructions.
6. Clean or replace air filters. Do not operate system with
out air filters in place.
7. Leak-test all refrigerant connections (fittings, joints,
gaskets, flanges, etc.)—both factory and field—with a
halide torch or electronic leak detector.
8. Replace all caps on service valves. Be sure they are
tight.
9. Check to be sure all tools and loose parts have been
removed from unit.
10. Check to be sure all panels, covers, and screws are in
place.
11. Following initial inspection, start unit and:
a. Check condenser fan and evaporator blower for
proper rotation.
b. Adjust furnace or evaporator blower for proper air
flow (approximately 400 cfm/ton).
c. Check fine and low voltage. (Should be within oper
ating voltage range stamped on unit rating plate.)
d. Check unit for proper operating refrigerant charge.
(See unit head pressure charging chart.)
e. Check compressor current draw in eunps.
f. Check unit for excessive noise, refrigerant tubing
for excessive vibration and for contact with other
parts. Correct as necessary.
g.
Do not leave installation until unit has been
observed through one or two complete cycles. Make
-10-