Unit controls and safety devices – Carrier 380B User Manual
Page 12
Attention! The text in this document has been recognized automatically. To view the original document, you can use the "Original mode".
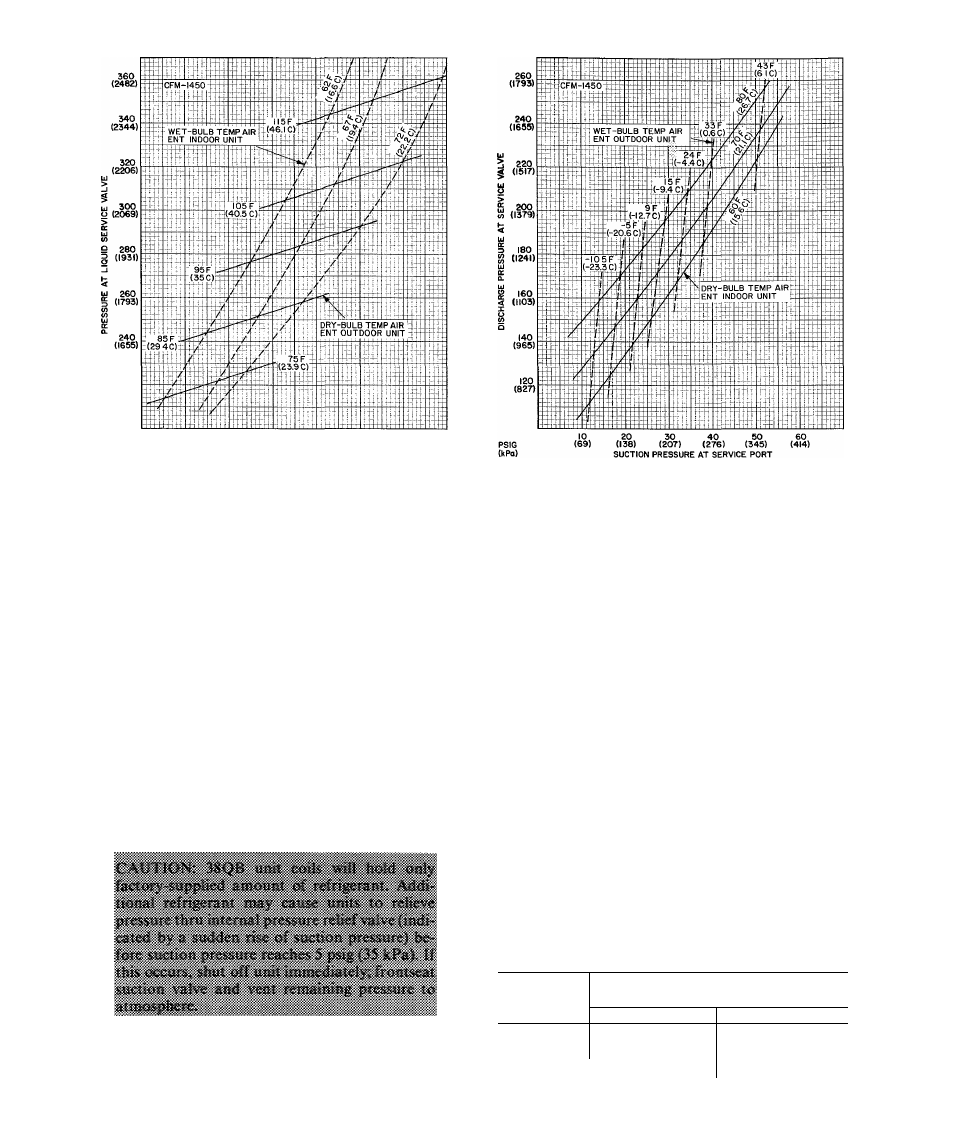
220
(1517)
PSIG
(kPa)
68
72
76
80
84
(469)
(496)
(524)
(552)
(579)
PRESSURE AT SUCTION SERVICE VALVE
Fig. 16 — 38QB042 with 40QB042
or 28HQ,VQ048
Cooling Cycle Operation Check Chart
f
Fig. 17 — 38QB042 with 40QB042
or 28HQ.VQ048
Heating Cycle Operation Check Chart
Filter Drier
— Install field-supplied filter drier
(Table 3) in system liquid line when refrigerant
system is opened for service as described under
Compressor Removal. Position drier in liquid line
at convenient location.
Pumpdown Procedure
— The system may be
pumped down in order to make repairs on low side
without losing complete refrigerant charge.
1. Attach pressure gage to suction service valve
gage port.
2. Frontseat the liquid line valve.
3. Start unit and run until suction pressure reaches
5 psig (35 kPa) (see Caution).
4. Shut unit off and frontseat suction valve.
5. Vent remaining pressure to atmosphere.
Unit Controls and Safety Devices
HIGH-PRESSURE RELIEF VALVE is located in
compressor. Relief valve opens at a pressure differ
ential of approximately 500 psig (3448 kPa) between
suction (low side) and discharge (high side) to allow
pressure equalization.
INTERNAL CURRENT AND TEMPERATURE
SENSITIVE OVERLOAD resets automatically
when internal compressor motor temperature drops
to a safe level (overloads may require up to 45
minutes to reset). When an internal overload is
suspected of being open, check by using an ohm-
meter or continuity tester. If necessary, refer to
Carrier Standard Service Techniques Manual,
Chapter 2, for complete instructions.
LIQUID LINE LOW-PRESSURE SWITCH
(LLPS) is connected in liquid line to work with
compressor internal thermostat in providing loss-of-
charge protection during the heating cycle. Control
is mounted on liquid line.
With a high-side leak, pressure gradually de
creases until low-pressure control stops the com
pressor. (Low-pressure control settings are shown
in Tables.)
Table 8 — Pressure Switch Settings
UNIT
LIQUID LINE
LOW-PRESSURE SWITCH
Cut-in
Cutout
018
024
030
036
22 ± 5 psig
7 ± 3psig
042
12