Check, test & start procedures – Twin City Backward Inclined Hinged Restaurant Exhaust Fan - BHRE - IM-610 User Manual
Page 6
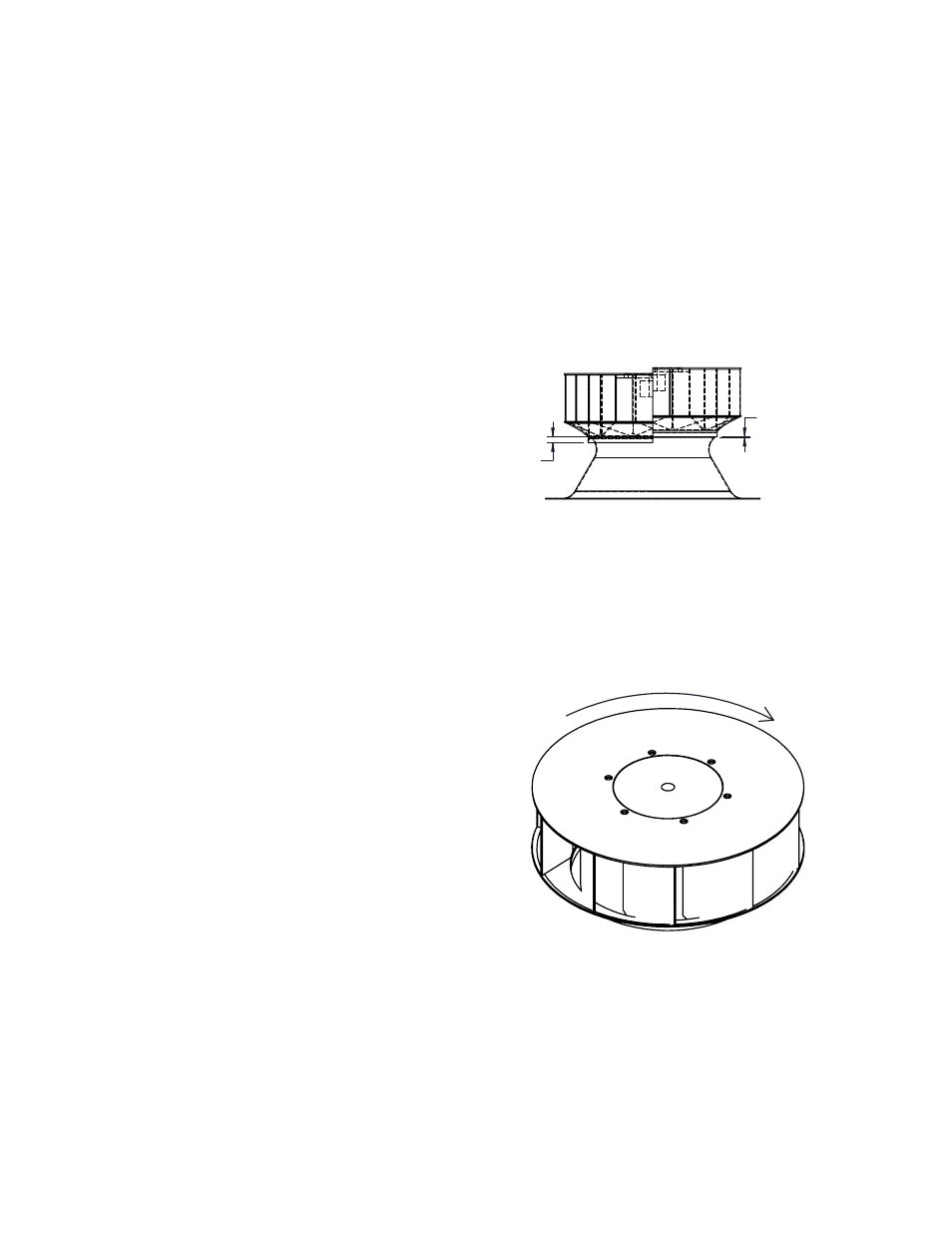
6
Twin City IM-610
Electrical Connection
1. Connect supply wiring to the disconnect switch (non-
fused standard).
2. The motor is factory set at the voltage marked on the
fan nameplate. Check the line voltage with the name-
plate voltage.
3. The main power wiring should be sized for the ampac-
ity shown on the dataplate. Size wires in accordance
with the ampacity tables in Article 310 of the National
Electrical Code. If long wires are required, it may be
necessary to increase wire size to prevent excessive
voltage drop. Wires should be sized for a maximum
of 3% voltage drop.
CAUTION: Use copper conductors only.
CAUTION: Protect wiring from sharp edges. Leave some
slack in the line to prevent damage.
4. Disconnect switches are not fused. The power leads
must be protected at the point of distribution in accor-
dance with the fan dataplate.
5. All units must be electrically grounded in accordance
with local codes or, in the absence of local codes,
with the latest edition of the National Electrical Code
(ANSI/NFPA 70). A ground lug is provided as standard
in the unit terminal box. Size grounding conductor in
accordance with Table 250-95 of the National Electrical
Code. DO NOT use the ground lug for connecting a
neutral conductor.
6. Supply voltage to the power ventilator should not vary
by more than 10% of the value indicated on the unit
dataplate. Phase unbalance must not exceed 2%.
Check, Test & Start Procedures
Warning: Electric shock hazard. Could cause severe
injury or death. Failure to bond the frame of this equip-
ment to the building electrical ground by use of the
grounding terminal provided or other acceptable means
may result in electrical shock. Disconnect electric power
before servicing equipment. Service to be performed only
by qualified personnel.
Before Start-up: Disconnect power before servicing unit
1. Check all fasteners and setscrews for tightness.
Note: The wheel position is set at the factory and the fan
was balanced and vibration tested prior to shipment.
Movement may have occurred during transport and realign-
ment may be necessary.
2. Check that the wheel is centered and free to rotate.
Centering can be changed by loosening isolator
mounts and repositioning the drive frame.
3. For optimum fan performance make sure that the
wheel to inlet venturi gap or overlap is maintained per
Figure 7. Height can be adjusted by loosening set
screws on the wheel and reposition on the fan shaft,
per the table.
4. Verify that the power supply matches the voltage on
the fan data plate and is within the 10% utilization
rate.
5. Apply power to unit and check rotation of wheel with
the directional arrow on the unit. All fans are clock-
wise, as viewed from drive side, per Figure 8.
Warning: Rotation is critical. If allowed to operate in the
wrong direction, the motor will overload and burn out. For
three-phase units, rotation can be changed by switching
any two of the three line leads. If the unit is checked with
temporary wiring, it should be rechecked when perma-
nently installed. Motor burn out or tripped overload protec-
tion devices are usually the result of wrong rotation.
6. Electrical Input Check: Perform check of fan ampere
draw and verify that motor nameplate amps are not
exceeded. Take into account the service factor of the
motor if it is above 1.0 S.F.
7. Fan RPM should be checked and verified with a
tachometer.
.44 Overlap,
Standard Fan
.13
.00 Gap, Swingout Fan
View from drive side
Figure 8.
Figure 7.
View from drive side